The thickness of the die on a pellet mill, specifically the effective length, plays a critical role in determining the quality and compactness of the pellets produced. The effective length is the portion of the die thickness that actively compresses the feed material into pellets. A greater effective length results in denser and more compact pellets, while a shorter effective length produces less compact pellets. The inlet depth, which is the depth of the countersink where the feed enters the compression area, also influences the pellet formation process. Understanding these dimensions is essential for optimizing pellet mill performance and achieving the desired pellet quality.
Key Points Explained:
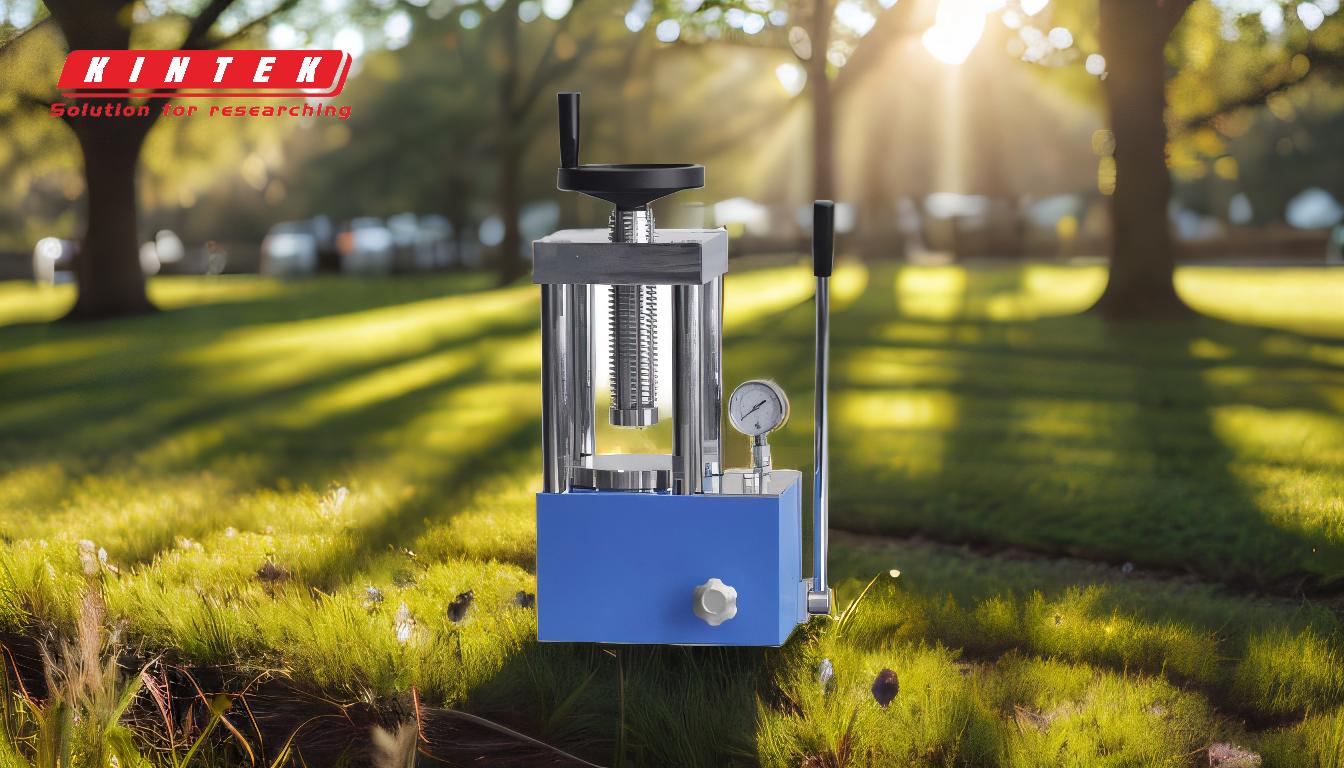
-
Effective Length (E) of the Die:
- The effective length is the part of the die thickness that directly compresses the feed material into pellets. It is a crucial factor in determining pellet density and compactness.
- A longer effective length increases the compression time and force applied to the feed, resulting in denser and more durable pellets.
- Conversely, a shorter effective length reduces compression, leading to less compact and potentially weaker pellets.
- The choice of effective length depends on the type of feed material and the desired pellet characteristics.
-
Inlet Depth:
- The inlet depth refers to the depth of the countersink at the entrance of the die where the feed material is introduced into the compression area.
- This dimension influences how the feed material is initially guided into the die and can affect the uniformity of pellet formation.
- Proper inlet depth ensures smooth feeding and consistent compression, which is essential for producing high-quality pellets.
-
Relationship Between Effective Length and Inlet Depth:
- The effective length and inlet depth work together to optimize the pelletizing process. The inlet depth ensures proper feed introduction, while the effective length determines the compression and final pellet quality.
- Balancing these dimensions is critical for achieving the desired pellet density, durability, and production efficiency.
-
Importance for Equipment Purchasers:
- When selecting a pellet mill, understanding the die thickness, effective length, and inlet depth is essential for matching the equipment to specific production needs.
- Different materials (e.g., biomass, animal feed, or fertilizers) may require varying die thicknesses and effective lengths to achieve optimal results.
- Equipment buyers should consult with manufacturers to ensure the die specifications align with their production goals and material characteristics.
By focusing on these key points, equipment purchasers can make informed decisions about pellet mill dies, ensuring they meet their production requirements and achieve the desired pellet quality.
Summary Table:
Factor | Description | Impact on Pellet Quality |
---|---|---|
Effective Length (E) | The portion of the die thickness that compresses feed material into pellets. | Longer E = denser, more durable pellets; Shorter E = less compact, weaker pellets. |
Inlet Depth | Depth of the countersink where feed enters the compression area. | Ensures smooth feeding and consistent compression for uniform pellet formation. |
Die Thickness | Total thickness of the die, including effective length and inlet depth. | Determines overall compression and pellet density. |
Material Type | Type of feed material (e.g., biomass, animal feed, fertilizers). | Influences required die thickness and effective length for optimal results. |
Need help selecting the right pellet mill die for your production needs? Contact our experts today!