Induction heating is often described as "instant," but this term requires clarification. While induction heating is significantly faster than traditional heating methods like gas or electric stovetops, it is not truly instantaneous. The speed of induction heating depends on factors such as the material being heated, the power of the induction system, and the size of the object. Induction heating generates heat directly within the object through electromagnetic induction, bypassing the need for external heat transfer, which makes it highly efficient and rapid. However, the term "instant" is relative, as the process still takes some time to raise the temperature of the material to the desired level.
Key Points Explained:
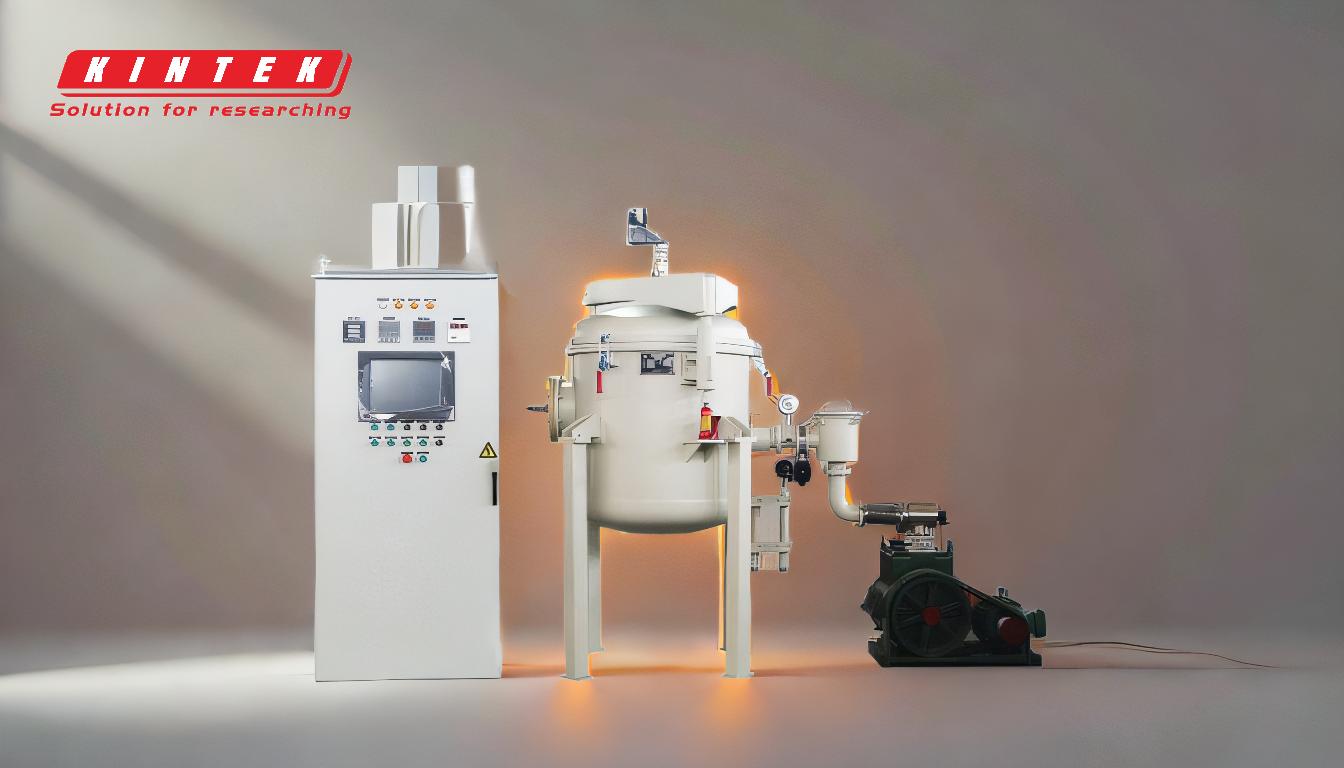
-
How Induction Heating Works:
- Induction heating uses electromagnetic induction to generate heat inside conductive materials like metals.
- A high-frequency alternating current passes through a coil, creating a magnetic field.
- This magnetic field induces eddy currents within the metal, generating heat directly inside the material.
- No direct contact or external flame is required, making the process clean and efficient.
-
Speed of Induction Heating:
- Induction heating is faster than traditional methods because heat is generated directly within the material, eliminating the need for heat transfer through conduction or convection.
- The speed depends on factors like the material's electrical conductivity, magnetic permeability, and the power of the induction system.
- For example, on an induction cooktop, water can boil in under a minute, which is significantly faster than gas or electric stovetops.
-
Why Induction Heating is Considered "Instant":
- The term "instant" refers to the immediate generation of heat within the material as soon as the induction system is activated.
- There is no preheating time required, unlike traditional methods where the burner or heating element must first warm up.
- The heat is localized and controllable, allowing for precise temperature adjustments without lag.
-
Factors Affecting the Speed of Induction Heating:
- Material Properties: Metals with high electrical conductivity and magnetic permeability heat up faster.
- Power Output: Higher-powered induction systems can generate more heat in less time.
- Size and Thickness: Smaller and thinner objects heat up faster than larger or thicker ones.
- Frequency of the Induction System: Higher frequencies are more effective for heating smaller objects, while lower frequencies are better for larger objects.
-
Advantages of Induction Heating:
- Efficiency: Around 90% of the energy is used for heating, making it highly efficient compared to gas or electric stovetops.
- Control: Temperature adjustments are immediate and precise, reducing the risk of overheating.
- Safety: The cooktop surface remains relatively cool, and there is no open flame, reducing the risk of burns or fires.
- Cleanliness: No combustion byproducts or residue, making it a clean heating method.
-
Limitations of Induction Heating:
- Material Restrictions: Only conductive materials like metals can be heated using induction.
- Initial Cost: Induction systems, especially high-powered ones, can be expensive to purchase and install.
- Power Requirements: Induction systems require a stable and sufficient power supply, which may not be available in all settings.
-
Applications of Induction Heating:
- Domestic: Induction cooktops are widely used in kitchens for their speed and efficiency.
- Industrial: Used for metal hardening, welding, and melting due to its rapid and localized heating capabilities.
- Medical: Sterilization of instruments and heating of medical implants.
- Automotive: Heat treatment of engine components and other metal parts.
In conclusion, while induction heating is not truly instantaneous, it is significantly faster and more efficient than traditional heating methods. The term "instant" reflects the immediate generation of heat within the material and the lack of preheating time, making it a highly effective and controllable heating solution for various applications.
Summary Table:
Aspect | Details |
---|---|
How It Works | Uses electromagnetic induction to generate heat directly in conductive materials. |
Speed | Faster than gas/electric stovetops; depends on material, power, and size. |
Why Called 'Instant' | Immediate heat generation; no preheating required. |
Key Advantages | High efficiency (90%), precise control, safety, and cleanliness. |
Limitations | Only works with conductive materials; high initial cost and power needs. |
Applications | Domestic (cooktops), industrial (welding), medical (sterilization), automotive. |
Discover how induction heating can revolutionize your applications—contact our experts today!