The spelling of "mold" or "mould" depends on regional language conventions. In American English, the word is spelled as "mold," while in British English, it is spelled as "mould." Both spellings refer to the same concept, whether it’s the fungal growth or the tool used in shaping materials. The difference lies solely in regional spelling preferences, with no impact on meaning or usage.
Key Points Explained:
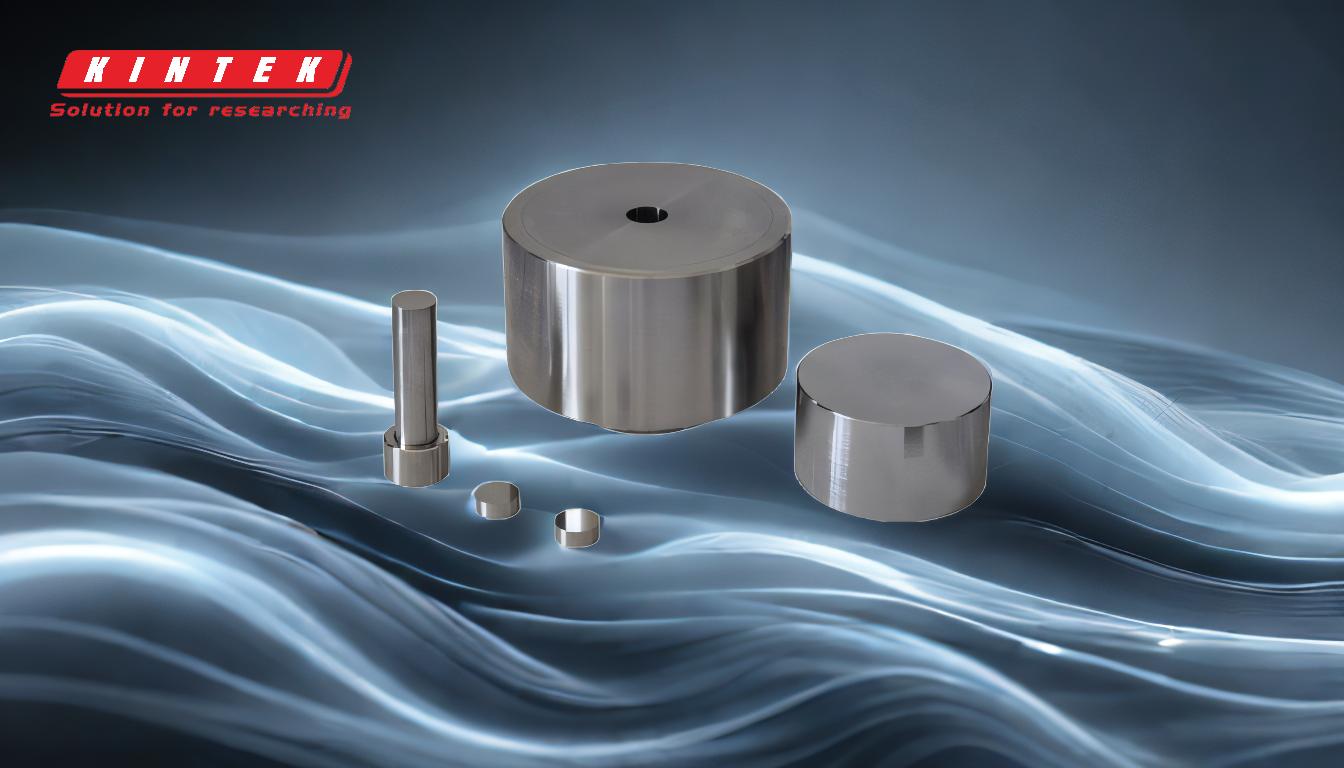
-
Regional Spelling Differences:
- American English: The word is spelled as "mold."
- British English: The word is spelled as "mould."
- Explanation: This distinction is part of broader differences between American and British English, such as "color" vs. "colour" or "center" vs. "centre." The choice of spelling depends on the audience or region.
-
Meaning and Usage:
- Both "mold" and "mould" refer to the same concepts:
- A fungus that grows in damp environments.
- A hollow container used to shape materials like plastic, metal, or concrete.
- Explanation: The spelling variation does not affect the meaning or application of the term. It is purely a linguistic preference based on regional norms.
- Both "mold" and "mould" refer to the same concepts:
-
Contextual Considerations:
- When writing for an American audience, use "mold."
- When writing for a British or international audience, use "mould."
- Explanation: Understanding the target audience is crucial for effective communication, especially in technical or professional contexts like equipment and consumable purchasing.
-
Practical Implications:
- For equipment or consumable purchasers, the spelling difference may arise in product descriptions, manuals, or specifications.
- Explanation: Ensuring consistency in spelling based on the intended audience can enhance clarity and professionalism in documentation.
-
Conclusion:
- The choice between "mold" and "mould" is a matter of regional spelling conventions, not meaning or functionality.
- Explanation: Recognizing and adapting to these differences is essential for clear and effective communication in global markets.
Summary Table:
Aspect | American English | British English |
---|---|---|
Spelling | mold | mould |
Meaning | Fungus or shaping tool | Fungus or shaping tool |
Usage Context | Use for American audiences | Use for British or international audiences |
Need help with technical documentation or product descriptions? Contact us today for expert guidance!