High temperature furnaces are constructed using specialized materials and components designed to withstand extreme heat while maintaining structural integrity and efficiency. These furnaces are typically made of refractory materials like graphite, ceramic, or steel, depending on the specific type and application. Heating elements, often composed of metals such as tungsten, molybdenum, or graphite, are used to achieve the desired temperatures. Additionally, advanced temperature control systems, including thermocouples and programmable controllers, ensure precise operation. The design and materials vary based on the furnace type, such as tube furnaces, box furnaces, or muffle furnaces, each optimized for specific temperature ranges and applications.
Key Points Explained:
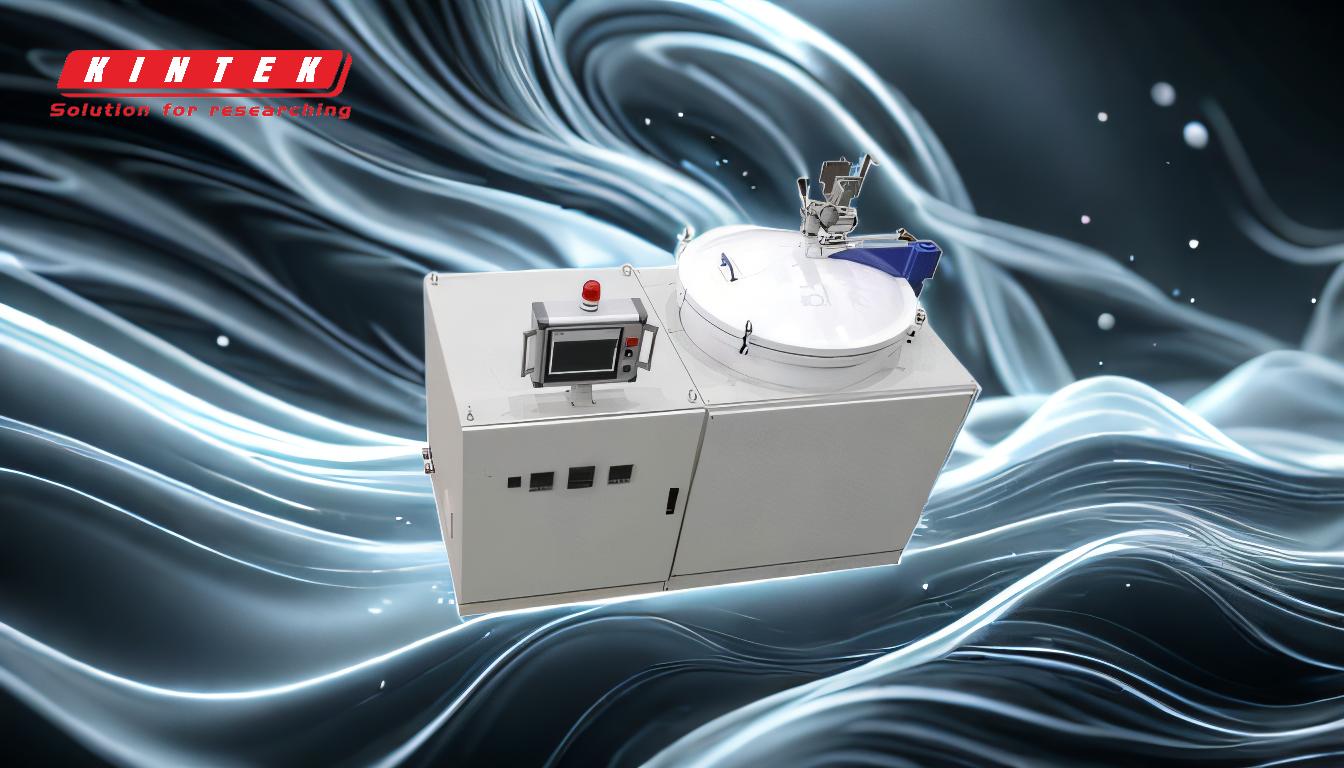
-
Refractory Materials:
- High temperature furnaces are primarily constructed using refractory materials, which are capable of withstanding extreme heat without degrading. Common materials include:
- Graphite: Used for its high thermal conductivity and ability to withstand temperatures up to 3000°C in inert or vacuum environments.
- Ceramic: Often used in muffle furnaces due to its ability to endure temperatures up to 1400°C without melting.
- Steel: Used in laboratory chamber furnaces for its durability and ability to prevent radiant heat loss.
- High temperature furnaces are primarily constructed using refractory materials, which are capable of withstanding extreme heat without degrading. Common materials include:
-
Heating Elements:
- Heating elements are critical components that generate the high temperatures required for furnace operation. Common materials for heating elements include:
- Tungsten and Molybdenum: These metals are used in vacuum furnaces and can withstand temperatures above 1200°C.
- Graphite: Often used in high temperature vacuum furnaces for its excellent thermal properties.
- Pure Metals: Aluminum and tantalum are also used in specific applications due to their high melting points and resistance to oxidation.
- Heating elements are critical components that generate the high temperatures required for furnace operation. Common materials for heating elements include:
-
Insulation and Heat Retention:
- High temperature furnaces are insulated to minimize heat loss and improve energy efficiency. Insulation materials include:
- Ceramic fiber: Used in muffle furnaces to maintain high internal temperatures.
- Refractory bricks: Commonly used in box furnaces to retain heat and protect the outer structure.
- High temperature furnaces are insulated to minimize heat loss and improve energy efficiency. Insulation materials include:
-
Temperature Control Systems:
- Precise temperature control is essential for high temperature furnaces. Key components include:
- Thermocouples: Used for accurate temperature measurement.
- PID Controllers: Provide programmable and precise temperature regulation.
- Touch Screen and PLC Systems: Enable fully automated control for complex heating processes.
- Precise temperature control is essential for high temperature furnaces. Key components include:
-
Types of High Temperature Furnaces:
- Different furnace types are designed for specific applications and temperature ranges:
- Tube Furnaces: Feature heating elements on both sides of the chamber for uniform heating, ideal for materials research and thermal processing.
- Box Furnaces: Used for batch processing of materials, often constructed with refractory bricks for heat retention.
- Muffle Furnaces: Designed with a ceramic inner chamber for high-temperature applications like ash testing and heat treatment.
- Different furnace types are designed for specific applications and temperature ranges:
-
Applications and Customization:
- High temperature furnaces are used in various industries, including metallurgy, materials science, and chemical processing. The choice of materials and design depends on the specific application, such as:
- Vacuum environments: Require materials like graphite and tungsten to prevent oxidation.
- Laboratory use: Often prioritize durability and safety, using steel and ceramic components.
- High temperature furnaces are used in various industries, including metallurgy, materials science, and chemical processing. The choice of materials and design depends on the specific application, such as:
By understanding the materials and components used in high temperature furnaces, purchasers can make informed decisions based on their specific needs, whether for industrial, laboratory, or research applications.
Summary Table:
Component | Materials Used | Key Features |
---|---|---|
Refractory Materials | Graphite, Ceramic, Steel | Withstand extreme heat, high thermal conductivity, durability |
Heating Elements | Tungsten, Molybdenum, Graphite, Aluminum, Tantalum | High melting points, resistance to oxidation, excellent thermal properties |
Insulation | Ceramic fiber, Refractory bricks | Minimize heat loss, improve energy efficiency |
Temperature Control | Thermocouples, PID Controllers, Touch Screen & PLC Systems | Precise temperature regulation, programmable, fully automated control |
Furnace Types | Tube Furnaces, Box Furnaces, Muffle Furnaces | Optimized for specific temperature ranges and applications |
Need a high temperature furnace tailored to your needs? Contact our experts today for personalized solutions!