Rotary kilns are complex industrial equipment primarily used for high-temperature processing of materials. They are made up of several critical components, each designed to withstand extreme conditions and ensure efficient operation. The key materials and components include the kiln shell, refractory lining, support tyres (riding rings), rollers, drive gear, and internal heat exchangers. The shell is typically made of steel, while the refractory lining is composed of heat-resistant materials to protect the shell from high temperatures. Support tyres and rollers are also made of durable materials to handle the kiln's weight and rotation. The drive gear and internal heat exchangers are customized based on the specific application and material being processed.
Key Points Explained:
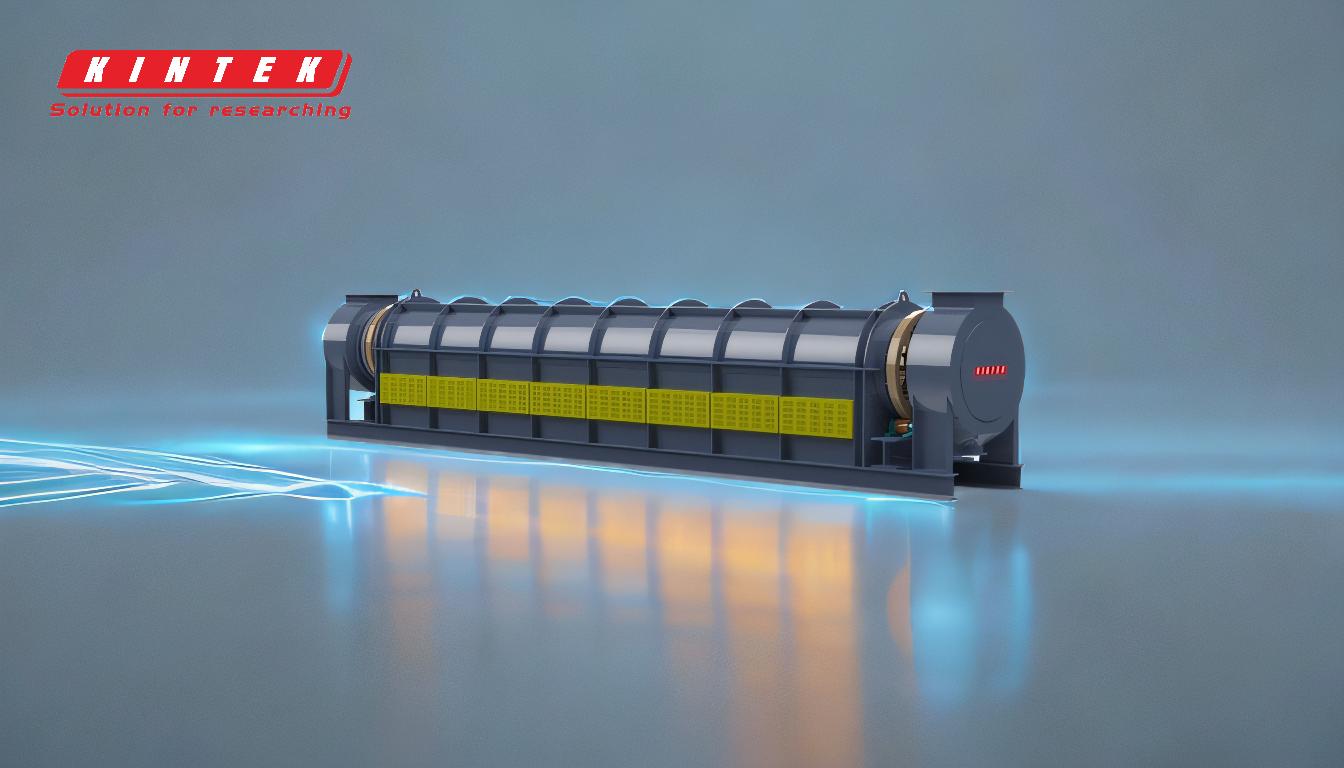
-
Kiln Shell:
- Material: The shell is usually constructed from high-quality steel, which provides the necessary strength and durability to withstand the mechanical stresses of rotation and the high temperatures inside the kiln.
- Function: The shell acts as the main structural component, housing the refractory lining and supporting the internal components. It is conically tapered at the ends to facilitate material movement and reduce stress concentrations.
-
Refractory Lining:
- Material: The lining is made from heat-resistant materials such as alumina, silica, or magnesia, depending on the operating temperature and the type of material being processed.
- Function: The refractory lining protects the steel shell from the extreme heat inside the kiln, preventing thermal damage and extending the lifespan of the kiln.
-
Support Tyres (Riding Rings) and Rollers:
- Material: These components are typically made from high-strength steel or cast iron to handle the kiln's weight and the rotational forces.
- Function: Support tyres and rollers provide the necessary support for the kiln shell, allowing it to rotate smoothly. They also help distribute the kiln's weight evenly across the support structure.
-
Drive Gear:
- Material: The drive gear is usually made from hardened steel to ensure durability and efficient power transmission.
- Function: The drive gear, along with the motor, induces the turning motion of the kiln. It can be a chain and sprocket drive, gear drive, friction drive, or direct drive assembly, depending on the specific requirements of the application.
-
Internal Heat Exchangers:
- Material: Heat exchangers are often made from materials that can withstand high temperatures and corrosive environments, such as stainless steel or specialized alloys.
- Function: Internal heat exchangers are used to optimize heat transfer within the kiln, ensuring that the material is heated uniformly and efficiently. They can be customized based on the specific thermal requirements of the process.
-
Additional Components:
- Tug Wheel Set: This set includes large and small gears and gear wheels, which are essential for the rotation mechanism.
- Thrust Rollers: These rollers help maintain the kiln's axial position and prevent it from moving out of alignment.
- Discharge Breeching: This component is located at the discharge end of the kiln and is designed to handle the discharge of processed material.
-
Customization:
- Material and Design: The materials and design of rotary kiln components can be customized based on the specific needs of the industry and the material being processed. Customization often involves selecting materials that can withstand higher temperatures or more corrosive environments, but this typically comes at a higher cost.
-
Lab Rotary Kiln:
- Kiln Body: The kiln body in lab-scale rotary kilns often uses an alumina fiber furnace for insulation and a 60W motor with a reduction gearbox for rotation.
- Tilt Control: The tilt of the furnace body is controlled by a hydraulic device operated with a hand wheel, allowing for precise control over the processing conditions.
In summary, rotary kilns are made from a combination of high-strength steel, refractory materials, and specialized components designed to withstand extreme conditions. Each component plays a crucial role in ensuring the efficient and reliable operation of the kiln, and materials can be customized to meet specific industrial requirements.
Summary Table:
Component | Material | Function |
---|---|---|
Kiln Shell | High-quality steel | Main structural component, supports internal parts and withstands rotation. |
Refractory Lining | Alumina, silica, or magnesia | Protects the shell from extreme heat, extending kiln lifespan. |
Support Tyres & Rollers | High-strength steel or cast iron | Supports kiln shell, ensures smooth rotation, and distributes weight. |
Drive Gear | Hardened steel | Induces kiln rotation, customized for specific applications. |
Internal Heat Exchangers | Stainless steel or specialized alloys | Optimizes heat transfer for uniform and efficient material processing. |
Need a rotary kiln tailored to your industrial needs? Contact us today to discuss customization options!