A sealed quench furnace offers several advantages, particularly in heat treatment processes. It provides a controlled atmosphere that prevents oxidation and decarburization of the metal being treated, ensuring a higher quality finish. The sealed environment also allows for precise temperature control, leading to consistent and repeatable results. Additionally, the quench process within a sealed furnace can be more efficient and safer, as it minimizes exposure to external contaminants and reduces the risk of fire hazards. These features make sealed quench furnaces highly desirable for industries requiring precise and high-quality heat treatment.
Key Points Explained:
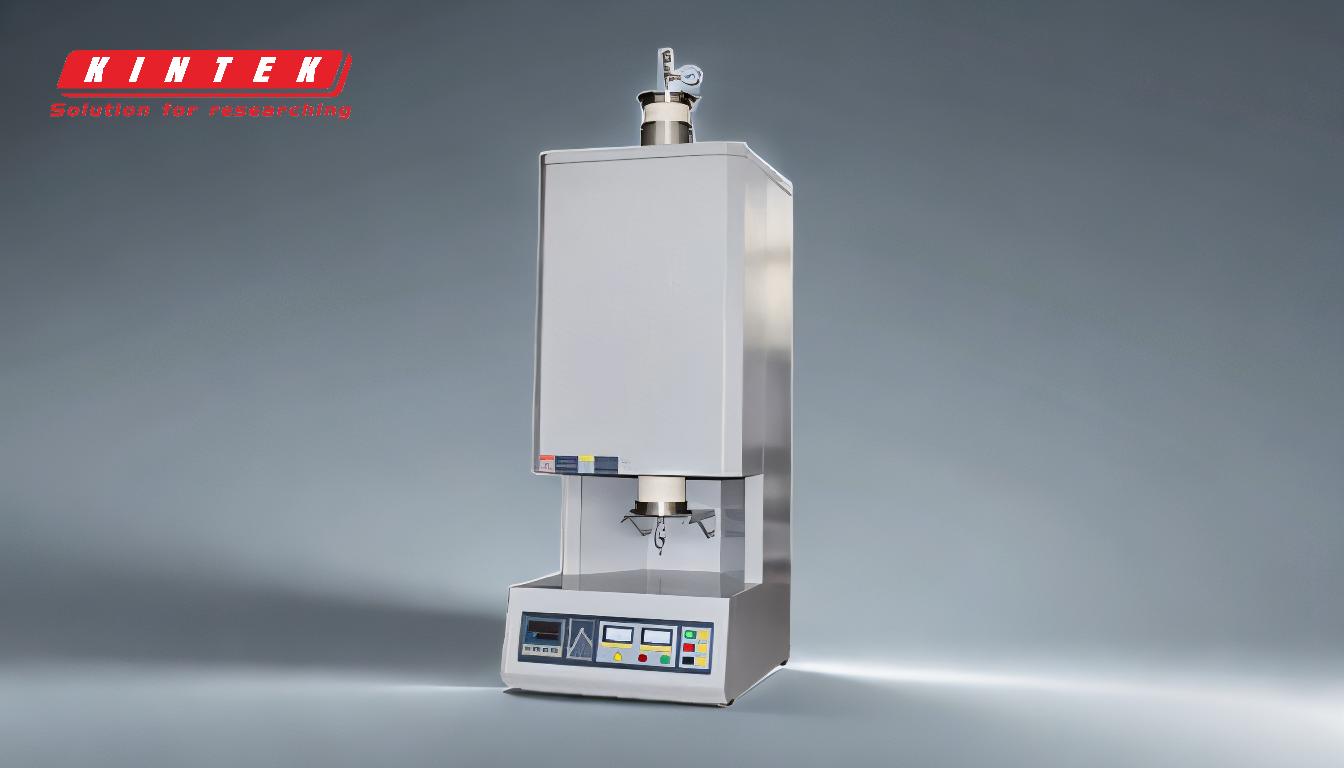
-
Controlled Atmosphere:
- A sealed quench furnace maintains a controlled atmosphere, which is crucial for preventing oxidation and decarburization of the metal. This ensures that the metal retains its desired properties and surface finish, which is essential for high-quality heat treatment.
-
Precise Temperature Control:
- The sealed environment allows for precise temperature regulation, which is vital for achieving consistent and repeatable results. This precision is particularly important in industries where uniformity in heat treatment is critical for product performance.
-
Efficient Quench Process:
- The quench process in a sealed quench furnace is more efficient due to the controlled environment. This efficiency translates to faster cooling rates and better control over the microstructure of the metal, leading to improved mechanical properties.
-
Safety and Reduced Contamination:
- The sealed design minimizes exposure to external contaminants, which can affect the quality of the heat treatment. Additionally, it reduces the risk of fire hazards associated with open quench systems, making it a safer option for operators.
-
Environmental Benefits:
- Similar to induction furnaces, sealed quench furnaces offer environmental benefits by reducing emissions and pollutants. This makes them a cleaner option for heat treatment processes, aligning with modern environmental regulations and sustainability goals.
By combining these advantages, sealed quench furnaces provide a superior solution for industries requiring precise, high-quality, and safe heat treatment processes.
Summary Table:
Advantage | Description |
---|---|
Controlled Atmosphere | Prevents oxidation and decarburization, ensuring high-quality metal finish. |
Precise Temperature Control | Achieves consistent and repeatable results for uniform heat treatment. |
Efficient Quench Process | Faster cooling rates and better control over metal microstructure. |
Safety and Reduced Contamination | Minimizes exposure to contaminants and reduces fire hazards. |
Environmental Benefits | Reduces emissions and pollutants, aligning with sustainability goals. |
Upgrade your heat treatment process with a sealed quench furnace—contact us today to learn more!