Thermal evaporation is a widely used technique in various industries due to its simplicity, cost-effectiveness, and versatility. It is particularly advantageous for creating thin films of metals and other materials, which are essential in applications ranging from electronic devices to protective coatings. The process involves heating a material in a vacuum until it evaporates and then condenses on a substrate to form a thin film. This method is favored for its ability to produce high-purity films, precise control over film thickness, and compatibility with a wide range of materials. Additionally, thermal evaporation can be adapted to different deposition rates and source configurations, such as using baskets or crucibles, depending on the specific requirements of the application.
Key Points Explained:
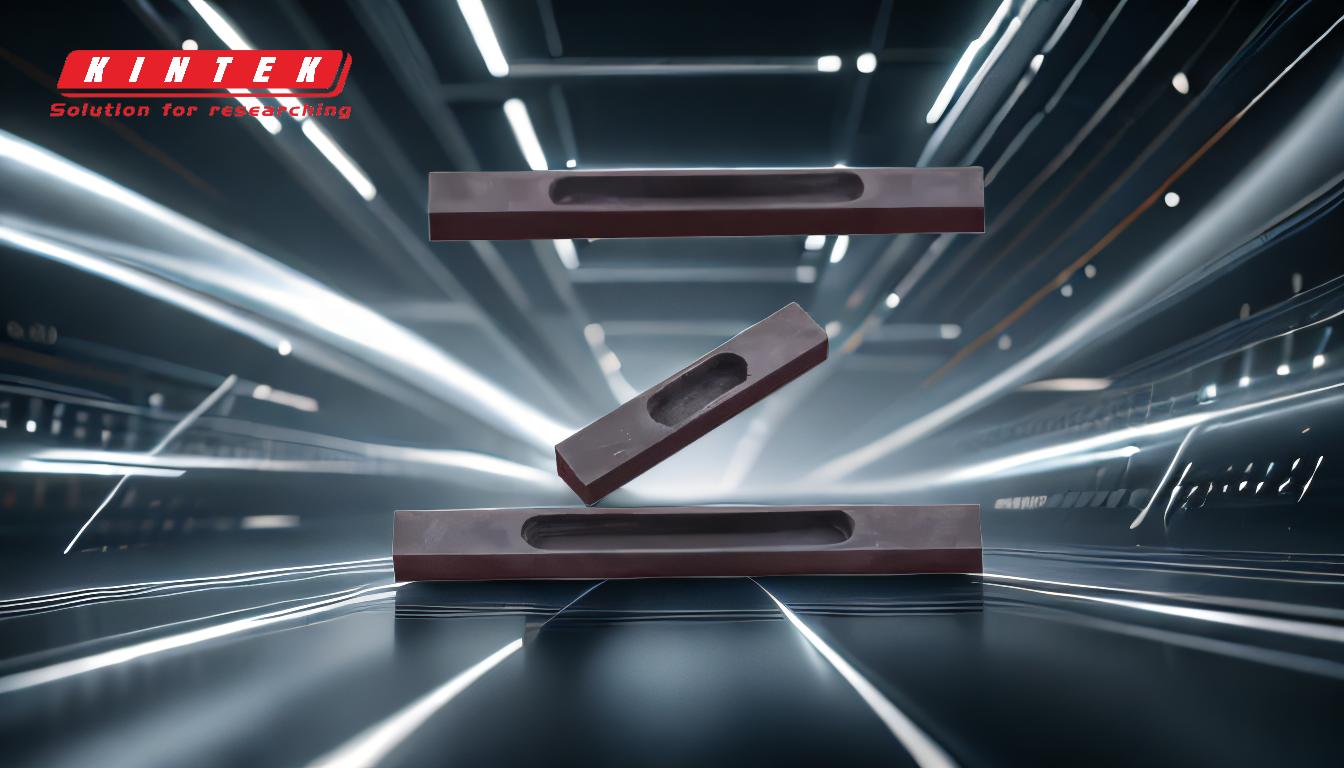
-
Versatility in Applications:
- Thermal evaporation is used in a variety of industries, including electronics, packaging, and aerospace. For example, it is employed to create metal bonding layers in OLEDs, solar cells, and thin film transistors. It is also used to deposit thin films of metals like aluminum on polymers for food packaging, heat and sound insulation, and decorative purposes. Furthermore, it finds applications in specialized fields such as NASA spacesuits, firefighter uniforms, emergency blankets, and anti-static or soundproof enclosures in aircraft.
-
High Purity Films:
- One of the significant advantages of thermal evaporation is its ability to produce high-purity films. Since the process occurs in a vacuum, there is minimal contamination from gases or impurities, resulting in films with excellent material properties. This is crucial for applications in electronics and optics where material purity directly impacts performance.
-
Precise Control Over Film Thickness:
- Thermal evaporation allows for precise control over the thickness of the deposited films. By adjusting parameters such as the evaporation rate and deposition time, manufacturers can achieve the desired film thickness with high accuracy. This is particularly important in applications like semiconductor manufacturing, where even slight variations in film thickness can affect device performance.
-
Compatibility with a Wide Range of Materials:
- The thermal evaporation process is compatible with a wide range of materials, including metals, alloys, and some organic compounds. This versatility makes it suitable for various applications, from depositing conductive layers in electronic devices to creating reflective coatings for mirrors and optical components.
-
Adaptability to Different Deposition Rates:
- Thermal evaporation can be adapted to achieve different deposition rates, depending on the specific requirements of the application. For instance, using baskets instead of boats can result in higher deposition rates due to higher source voltages. This flexibility allows manufacturers to optimize the process for different materials and applications.
-
Use of Baskets and Crucibles:
- Baskets are particularly useful for users who are less concerned with material losses. They allow for higher deposition rates with the same current due to generally high source voltages. Material is emitted in all directions from a basket, and box shielding can be used to contain stray deposition. Baskets can also be fitted with crucibles, which are often used for precious metals or when a large volume of evaporant needs to be supported. This adaptability in source configuration enhances the versatility of thermal evaporation.
-
Cost-Effectiveness:
- Compared to other thin-film deposition techniques, thermal evaporation is relatively cost-effective. The equipment required is less complex, and the process consumes less energy, making it an economical choice for many applications. This cost advantage is particularly beneficial for large-scale production or applications where budget constraints are a concern.
-
Simplicity and Ease of Use:
- The thermal evaporation process is straightforward and easy to set up and operate. This simplicity reduces the learning curve for operators and minimizes the risk of errors during the deposition process. Additionally, the ease of maintenance and lower operational complexity contribute to its widespread adoption in various industries.
In summary, thermal evaporation offers numerous advantages, including versatility, high purity, precise control, material compatibility, adaptability, and cost-effectiveness. These benefits make it a preferred choice for a wide range of applications, from electronics to aerospace. For more detailed information on thermal evaporation, you can explore further resources.
Summary Table:
Advantage | Description |
---|---|
Versatility | Used in electronics, packaging, aerospace, and more for thin film applications. |
High Purity Films | Produces contamination-free films, ideal for electronics and optics. |
Precise Thickness Control | Allows accurate adjustments for consistent film thickness. |
Material Compatibility | Works with metals, alloys, and organic compounds for diverse applications. |
Adaptable Deposition Rates | Adjustable rates using baskets or crucibles for optimized results. |
Cost-Effectiveness | Economical due to simple equipment and low energy consumption. |
Ease of Use | Simple setup, operation, and maintenance for efficient workflows. |
Ready to leverage thermal evaporation for your applications? Contact us today to learn more!