Sintering is a highly advantageous manufacturing process that offers numerous benefits, including higher purity, reduced weight, improved precision, and the ability to create complex shapes and high-melting-point metals. It is a reliable and repeatable method, particularly when conducted in controlled atmospheres, which enhances the quality of ceramic materials by allowing precise control over their composition and structure. This makes sintering particularly valuable for materials sensitive to atmospheric conditions.
Key Points Explained:
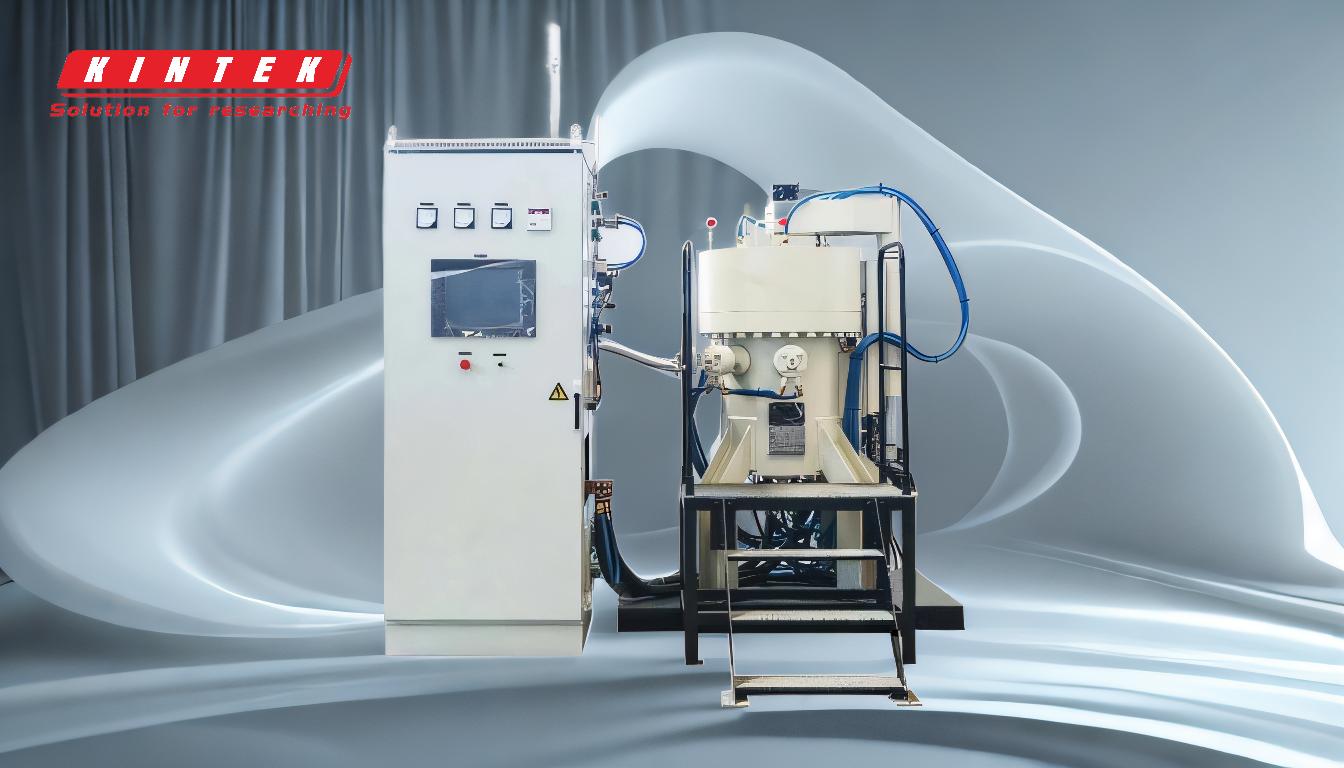
-
Higher Purity:
- Sintering involves heating materials below their melting point, which reduces the risk of contamination from melting agents or impurities. This results in a final product with higher purity compared to traditional melting and casting methods.
-
Lower Weight of the Final Product:
- The sintering process compacts powdered materials into a solid form, often resulting in a lighter final product. This is particularly beneficial in industries like aerospace and automotive, where weight reduction is critical for performance and efficiency.
-
Higher Manufacturing Precision:
- Sintering allows for precise control over the dimensions and shape of the final product. This is achieved by using molds or dies that can create highly detailed and accurate parts, making it ideal for applications requiring tight tolerances.
-
Ability to Form Complex Shapes:
- Unlike traditional manufacturing methods, sintering can produce intricate and complex shapes that would be difficult or impossible to achieve through machining or casting. This capability is especially useful in industries like electronics and medical devices.
-
Manufacturing High Melting Point Metals:
- Sintering is particularly advantageous for materials with high melting points, such as tungsten or molybdenum. Since sintering occurs below the melting point, it avoids the challenges associated with melting these metals, such as high energy consumption and equipment wear.
-
Reliability and Repeatability:
- The sintering process is highly consistent, ensuring that each batch of products meets the same quality standards. This repeatability is crucial for industries where uniformity and reliability are paramount.
-
Atmosphere Control for Ceramic Materials:
- Sintering in a controlled atmosphere allows for precise regulation of the material's composition and microstructure. This is particularly important for ceramic materials that are sensitive to atmospheric conditions, as it ensures optimal product quality and performance.
-
Unique Advantages of Atmosphere Sintering Furnaces:
- For materials that react with oxygen or other gases, atmosphere sintering furnaces provide an environment where the sintering process can occur without contamination or degradation. This is essential for producing high-quality ceramic components used in advanced applications.
Summary Table:
Advantage | Description |
---|---|
Higher Purity | Reduces contamination, resulting in a purer final product. |
Lower Weight | Produces lighter components, ideal for aerospace and automotive industries. |
Higher Precision | Enables tight tolerances and detailed shapes for high-accuracy applications. |
Complex Shapes | Creates intricate designs difficult to achieve with traditional methods. |
High Melting Point Metals | Sinters metals like tungsten without the challenges of melting. |
Reliability and Repeatability | Ensures consistent quality across batches for uniform production. |
Atmosphere Control | Enhances ceramic material quality by controlling composition and microstructure. |
Atmosphere Sintering Furnaces | Prevents contamination, ideal for sensitive materials in advanced applications. |
Unlock the potential of sintering for your manufacturing needs—contact our experts today!