Heat treatment is a critical process in metallurgy and materials science, used to alter the physical and mechanical properties of metals and alloys. The primary categories of heat treatment include annealing, quenching, tempering, normalizing, case hardening, and martensitic transformation. Each method serves a specific purpose, such as improving ductility, increasing hardness, or relieving internal stresses. These processes are often performed in controlled environments to prevent oxidation and other surface defects, ensuring the desired material properties are achieved.
Key Points Explained:
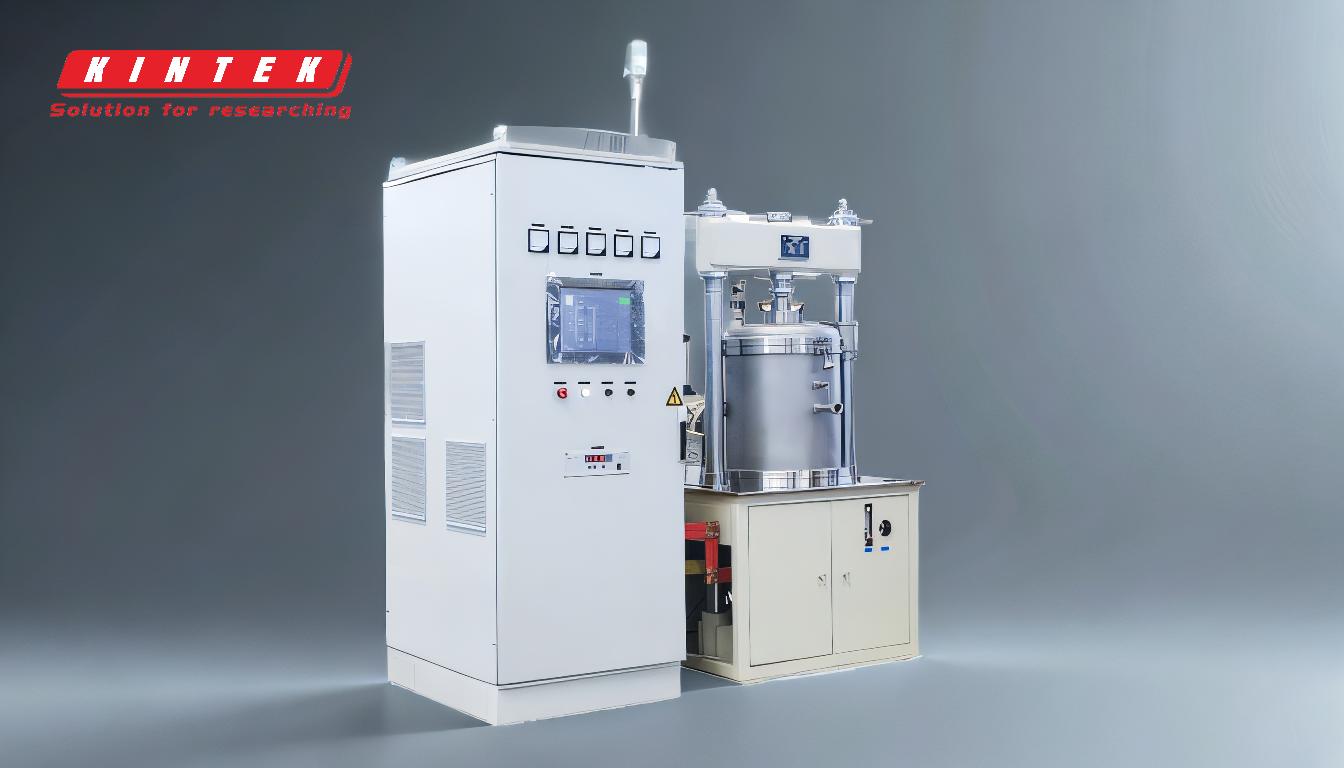
-
Annealing
- Purpose: Annealing is used to soften metals, improve ductility, and relieve internal stresses. It involves heating the material to a specific temperature and then cooling it slowly.
- Process: The metal is heated above its recrystallization temperature, held at that temperature for a period, and then cooled in a furnace or air.
- Applications: Commonly used for steel, copper, and aluminum to enhance machinability and reduce brittleness.
-
Quenching
- Purpose: Quenching rapidly cools metals to increase hardness and strength. It is often used in conjunction with hardening processes.
- Process: The metal is heated to a high temperature and then rapidly cooled in water, oil, or air.
- Applications: Used for hardening steel and other alloys, but can make materials brittle if not tempered afterward.
-
Tempering
- Purpose: Tempering reduces brittleness caused by quenching and improves toughness and ductility.
- Process: The metal is reheated to a temperature below its critical point and then cooled at a controlled rate.
- Applications: Commonly applied to hardened steel to balance hardness and toughness.
-
Normalizing
- Purpose: Normalizing refines the grain structure, improves mechanical properties, and relieves internal stresses.
- Process: The metal is heated to a temperature above its critical range and then cooled in air.
- Applications: Used for steel to produce a uniform microstructure and improve machinability.
-
Case Hardening
- Purpose: Case hardening increases the surface hardness of a metal while maintaining a softer, tougher core.
- Process: Techniques like carburizing, nitriding, or carbonitriding are used to introduce carbon or nitrogen into the surface layer.
- Applications: Ideal for components like gears and bearings that require a hard surface and a tough interior.
-
Martensitic Transformation
- Purpose: This process creates a hard, brittle structure in steel by rapidly cooling it to form martensite.
- Process: The steel is heated to a high temperature and then quenched to lock in the martensitic structure.
- Applications: Used in high-strength applications like knives, tools, and automotive parts.
-
Vacuum Heat Treatment
- Purpose: Vacuum heat treatment prevents oxidation and contamination during high-temperature processes.
- Process: Includes vacuum annealing, quenching, tempering, and sintering, all performed in a vacuum or controlled atmosphere.
- Applications: Used for high-precision components in aerospace, medical, and tooling industries.
-
Carburizing
- Purpose: Increases surface hardness by adding carbon to the surface layer of low-carbon steel.
- Process: The metal is heated in a carbon-rich environment, allowing carbon to diffuse into the surface.
- Applications: Used for gears, shafts, and other components requiring wear resistance.
-
Brazing
- Purpose: Joins metals by melting a filler metal without melting the base metals.
- Process: Performed at high temperatures in a controlled atmosphere to prevent oxidation.
- Applications: Common in joining copper, silver, and other non-ferrous metals in plumbing and electronics.
-
Sintering
- Purpose: Bonds powdered metals into a solid mass by heating below the melting point.
- Process: The metal powder is compacted and heated in a protective atmosphere.
- Applications: Used in powder metallurgy for producing complex shapes and porous components.
-
Bright Annealing
- Purpose: Minimizes oxidation and maintains a bright surface finish during annealing.
- Process: Performed in a pure hydrogen, nitrogen, or argon atmosphere.
- Applications: Used for stainless steel and other alloys requiring a clean, oxidation-free surface.
-
Stress Relieving
- Purpose: Reduces residual stresses in metals caused by machining, welding, or cold working.
- Process: The metal is heated to a temperature below its critical range and then cooled slowly.
- Applications: Used for welded structures, castings, and machined parts to prevent distortion.
By understanding these categories and their specific applications, equipment and consumable purchasers can make informed decisions about the most suitable heat treatment processes for their needs. Each method offers unique benefits, and the choice depends on the desired material properties and the application requirements.
Summary Table:
Heat Treatment Method | Purpose | Applications |
---|---|---|
Annealing | Soften metals, improve ductility, relieve stress | Steel, copper, aluminum |
Quenching | Increase hardness and strength | Hardening steel and alloys |
Tempering | Reduce brittleness, improve toughness | Hardened steel |
Normalizing | Refine grain structure, improve properties | Steel for uniform microstructure |
Case Hardening | Increase surface hardness, maintain tough core | Gears, bearings |
Martensitic Transformation | Create hard, brittle structure | Knives, tools, automotive parts |
Vacuum Heat Treatment | Prevent oxidation, high precision | Aerospace, medical, tooling industries |
Carburizing | Add carbon to surface, increase hardness | Gears, shafts |
Brazing | Join metals without melting base metals | Plumbing, electronics |
Sintering | Bond powdered metals into solid mass | Powder metallurgy for complex shapes |
Bright Annealing | Minimize oxidation, maintain bright surface | Stainless steel, oxidation-free alloys |
Stress Relieving | Reduce residual stresses | Welded structures, castings, machined parts |
Discover the best heat treatment solution for your needs—contact our experts today!