Heat treatment is a critical process in metallurgy and materials science, used to alter the physical and mechanical properties of metals and alloys. However, it is not without its challenges and failures. Common issues include the formation of an oxide film on the workpiece surface, a harsh treatment environment, and limited applicability of certain techniques. These failures can lead to suboptimal material properties, increased costs, and reduced efficiency in manufacturing processes. Understanding these failures is essential for improving heat treatment methods and ensuring the production of high-quality components.
Key Points Explained:
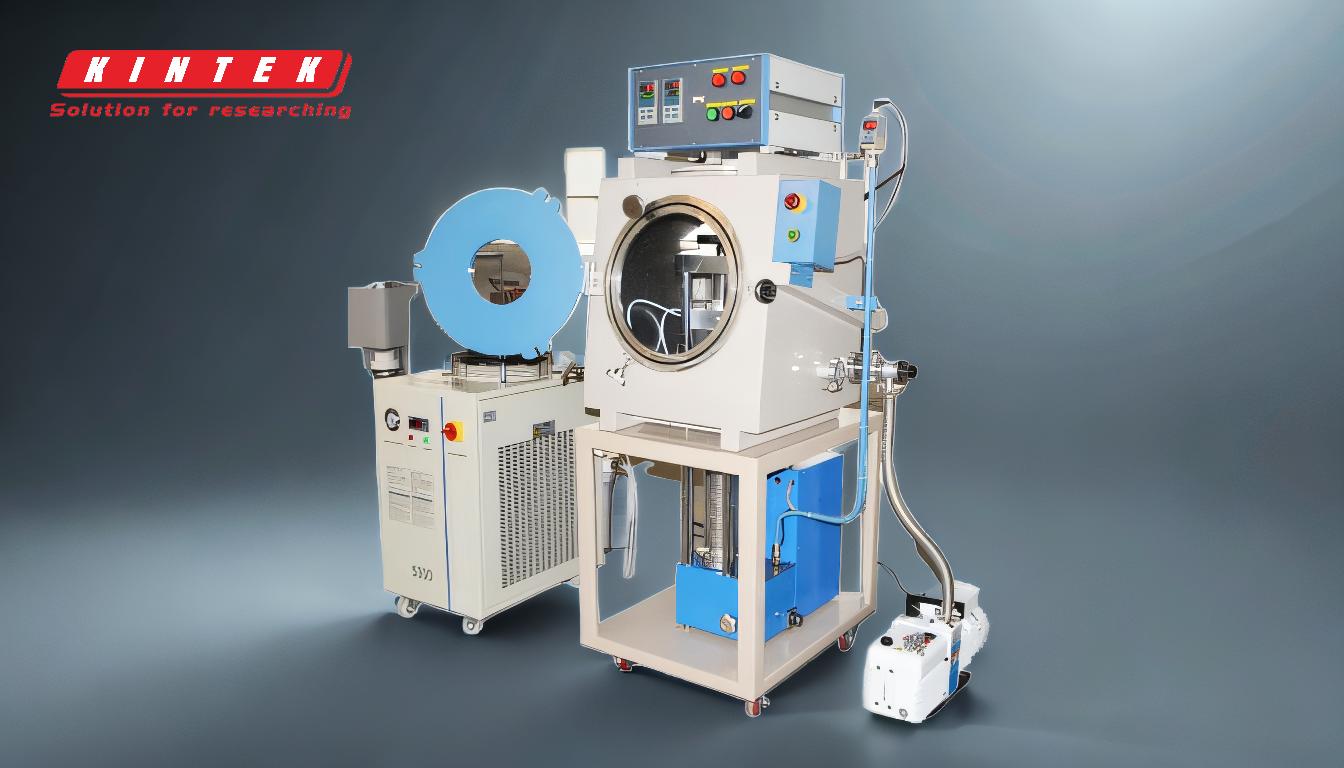
-
Formation of Oxide Film:
- Description: Ordinary atmosphere heat treatment often results in the formation of an oxide film on the workpiece surface. This oxide layer can negatively impact the material's properties and appearance.
- Impact: The oxide film can lead to surface defects, reduced corrosion resistance, and poor adhesion of subsequent coatings. It can also interfere with the heat treatment process itself, leading to inconsistent results.
- Mitigation: To mitigate this issue, controlled atmosphere heat treatment or vacuum heat treatment can be employed. These methods reduce or eliminate the presence of oxygen, thereby preventing oxide formation.
-
Harsh Treatment Environment:
- Description: The environment in which heat treatment is conducted can be harsh, with high temperatures and potentially corrosive atmospheres.
- Impact: The harsh environment can cause degradation of the equipment, leading to increased maintenance costs and downtime. It can also affect the quality of the treated materials, especially if the environment is not properly controlled.
- Mitigation: Using advanced materials for furnace construction and implementing better environmental controls can help mitigate these issues. Regular maintenance and monitoring of the heat treatment environment are also crucial.
-
Limited Applicability:
- Description: Certain heat treatment techniques have limited applicability due to the specific requirements of different materials and applications.
- Impact: This limitation can restrict the use of heat treatment in certain industries or for certain materials, leading to the need for alternative processing methods that may be less effective or more costly.
- Mitigation: Research and development into new heat treatment methods, such as advanced surface treatments or hybrid techniques, can expand the applicability of heat treatment. Customizing heat treatment processes to specific material requirements can also help overcome these limitations.
-
Common Heat Treatment Techniques and Their Challenges:
- Annealing: Used to soften materials and improve machinability. Challenges include controlling the cooling rate to achieve the desired microstructure.
- Quenching: Rapid cooling to harden materials. Challenges include the risk of cracking or distortion due to thermal stresses.
- Tempering: Reduces brittleness after quenching. Challenges include achieving the right balance between hardness and toughness.
- Case Hardening: Hardens the surface while keeping the core soft. Challenges include ensuring uniform hardness and depth of the hardened layer.
- Normalizing: Improves uniformity in microstructure. Challenges include controlling the cooling rate to avoid unwanted phase transformations.
-
Economic and Quality Issues:
- Cost: Heat treatment processes can be expensive due to the need for specialized equipment and energy consumption.
- Quality: Inconsistent results can lead to variability in product quality, affecting performance and reliability.
- Mitigation: Implementing process optimization, automation, and quality control measures can help reduce costs and improve consistency.
Understanding these failures and their underlying causes is crucial for improving heat treatment processes. By addressing these issues, manufacturers can enhance the quality and performance of treated materials, leading to better products and more efficient production processes.
Summary Table:
Failure | Description | Impact | Mitigation |
---|---|---|---|
Formation of Oxide Film | Oxide layer forms on workpiece surface during ordinary atmosphere heat treatment. | Surface defects, reduced corrosion resistance, poor coating adhesion. | Use controlled atmosphere or vacuum heat treatment. |
Harsh Treatment Environment | High temperatures and corrosive atmospheres degrade equipment and materials. | Increased maintenance costs, downtime, and inconsistent material quality. | Use advanced furnace materials and improve environmental controls. |
Limited Applicability | Certain techniques are unsuitable for specific materials or applications. | Restricted use, higher costs, and reliance on less effective alternatives. | Research new methods and customize processes for specific material needs. |
Economic and Quality Issues | High costs and inconsistent results due to specialized equipment and processes. | Increased expenses and variability in product quality. | Optimize processes, automate, and implement quality control measures. |
Struggling with heat treatment failures? Contact our experts to optimize your process and improve material quality!