Cold working, a process that involves shaping metal at temperatures below its recrystallization point, has a wide range of industrial applications due to its ability to enhance the mechanical properties of metals. This process is particularly valued for increasing strength, hardness, and dimensional accuracy while maintaining or improving surface finish. Industries such as automotive, aerospace, electronics, and construction extensively utilize cold working techniques to produce high-performance components. The process is also cost-effective, as it reduces the need for heat treatment and minimizes material waste. Cold working is integral to manufacturing processes like rolling, drawing, forging, and extrusion, making it a cornerstone of modern industrial production.
Key Points Explained:
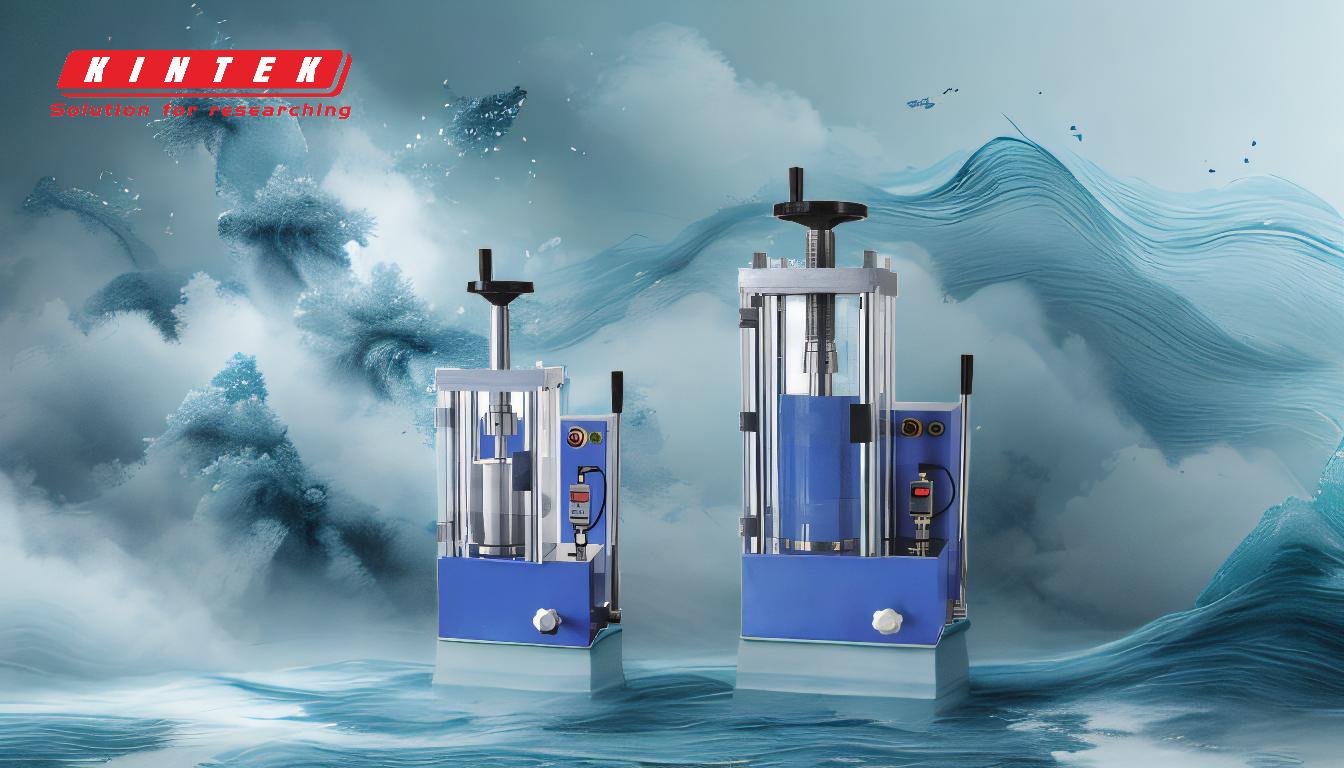
-
Enhanced Mechanical Properties:
- Cold working improves the strength and hardness of metals by introducing dislocations in the crystal structure, which impede the movement of atoms. This process, known as strain hardening, is crucial for applications requiring high durability and resistance to deformation.
- The process also enhances the surface finish of the metal, making it suitable for applications where aesthetics and precision are important.
-
Dimensional Accuracy:
- Cold working allows for precise control over the dimensions of the final product. This is particularly important in industries like aerospace and electronics, where components must meet strict tolerances.
- The absence of heat reduces the risk of warping or distortion, ensuring that the final product maintains its intended shape and size.
-
Cost-Effectiveness:
- By eliminating the need for heat treatment, cold working reduces energy consumption and associated costs. This makes it an economical choice for large-scale production.
- The process also minimizes material waste, as it often involves near-net-shape manufacturing, where the final product is very close to the desired dimensions, reducing the need for extensive machining.
-
Versatility in Applications:
- Automotive Industry: Cold working is used to produce high-strength components such as gears, shafts, and suspension parts. The process ensures that these parts can withstand the stresses and strains encountered during vehicle operation.
- Aerospace Industry: Components like turbine blades, fasteners, and structural elements benefit from the enhanced mechanical properties provided by cold working. The precision and reliability of these parts are critical for the safety and performance of aircraft.
- Electronics Industry: Cold working is employed in the production of connectors, springs, and other small components that require high precision and durability. The process ensures that these parts can function reliably in electronic devices.
- Construction Industry: Cold working is used to manufacture structural steel, reinforcing bars, and other construction materials. The enhanced strength and durability of these materials are essential for the safety and longevity of buildings and infrastructure.
-
Common Cold Working Techniques:
- Rolling: This process involves passing metal through rollers to reduce its thickness and improve its mechanical properties. It is commonly used to produce sheets, plates, and foils.
- Drawing: Metal is pulled through a die to reduce its diameter and increase its length. This technique is used to produce wires, rods, and tubes.
- Forging: Metal is shaped by applying compressive forces, often using dies. This process is used to produce complex shapes with high strength and durability.
- Extrusion: Metal is forced through a die to create long, continuous shapes with a consistent cross-section. This technique is used to produce bars, tubes, and profiles.
-
Environmental and Safety Considerations:
- Cold working is generally considered more environmentally friendly than hot working, as it consumes less energy and produces fewer emissions.
- However, the process can generate significant amounts of metal dust and chips, which must be managed to ensure worker safety and environmental compliance.
In summary, cold working is a versatile and cost-effective process that plays a critical role in modern industrial manufacturing. Its ability to enhance the mechanical properties, dimensional accuracy, and surface finish of metals makes it indispensable across a wide range of industries. From automotive and aerospace to electronics and construction, cold working ensures the production of high-performance components that meet the demanding requirements of today's industrial applications.
Summary Table:
Industry | Applications | Benefits |
---|---|---|
Automotive | Gears, shafts, suspension parts | High strength, durability, and resistance to deformation |
Aerospace | Turbine blades, fasteners, structural elements | Precision, reliability, and safety for critical components |
Electronics | Connectors, springs, small components | High precision, durability, and reliable performance in electronic devices |
Construction | Structural steel, reinforcing bars, construction materials | Enhanced strength and durability for safe and long-lasting infrastructure |
Techniques | Rolling, drawing, forging, extrusion | Versatile processes for producing sheets, wires, complex shapes, and more |
Discover how cold working can optimize your industrial processes—contact our experts today for tailored solutions!