Chemical vapor deposition (CVD) is a versatile and widely used technique for growing thin films and coatings on substrates. The process involves the decomposition of volatile compounds into reactive species, which then react on the substrate surface to form a solid film. The quality and characteristics of the deposited material depend on several key parameters, including temperature, pressure, gas flow rate, gas concentration, and the choice of catalyst. Understanding these parameters is crucial for optimizing the CVD process to achieve desired film properties, such as purity, crystallinity, and thickness.
Key Points Explained:
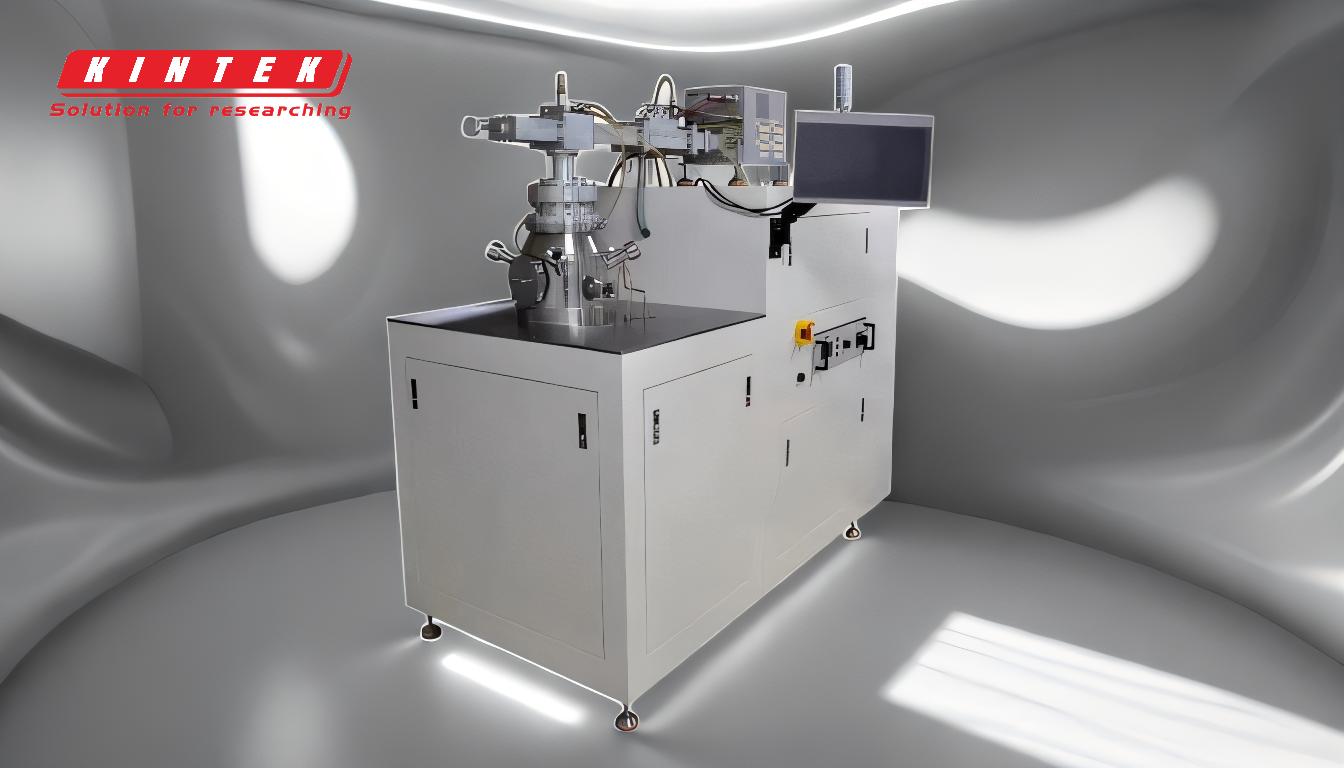
-
Temperature:
- Temperature is one of the most critical parameters in CVD. It affects the rate of chemical reactions, the decomposition of precursor gases, and the mobility of atoms on the substrate surface.
- Higher temperatures generally increase the reaction rate and improve the crystallinity of the deposited film. However, excessively high temperatures can lead to unwanted side reactions or degradation of the substrate.
- The optimal temperature range depends on the specific material being deposited and the precursor gases used. For example, graphene growth on copper catalysts typically occurs at temperatures around 1000°C.
-
Pressure:
- The pressure in the reaction chamber influences the mean free path of gas molecules, the rate of gas-phase reactions, and the uniformity of the deposited film.
- Low-pressure CVD (LPCVD) is often used to achieve high-quality films with excellent uniformity and step coverage. In contrast, atmospheric-pressure CVD (APCVD) is simpler and more cost-effective but may result in less uniform films.
- The choice of pressure depends on the desired film properties and the specific CVD variant being used.
-
Gas Flow Rate:
- The flow rate of precursor gases and carrier gases controls the supply of reactive species to the substrate surface. It affects the growth rate, film thickness, and uniformity.
- A higher flow rate can increase the deposition rate but may also lead to incomplete reactions or the formation of defects. Conversely, a lower flow rate may result in slower growth but better film quality.
- Precise control of gas flow rates is essential for achieving reproducible results and optimizing film properties.
-
Gas Concentration:
- The concentration of precursor gases in the reaction chamber determines the availability of reactive species for film growth. It influences the stoichiometry, composition, and properties of the deposited material.
- For example, in the CVD growth of graphene, the ratio of methane (CH₄) to hydrogen (H₂) is critical for controlling the number of graphene layers and the quality of the film.
- Adjusting gas concentrations allows for the synthesis of both pure and complex materials with tailored properties.
-
Catalyst:
- Catalysts play a vital role in many CVD processes, particularly in the growth of materials like graphene and carbon nanotubes. They lower the activation energy for chemical reactions and promote the formation of high-quality films.
- Transition metals, such as copper and nickel, are commonly used as catalysts due to their cost-effectiveness and ability to facilitate the decomposition of precursor gases.
- The choice of catalyst and its surface properties (e.g., crystal orientation, roughness) significantly impact the nucleation and growth of the film.
-
Reaction Atmosphere:
- The composition of the reaction atmosphere, including the presence of reactive or inert gases, affects the chemical reactions and the quality of the deposited film.
- For example, hydrogen is often used as a reducing agent to prevent oxidation and promote the formation of pure materials. In contrast, oxygen or water vapor can be introduced to facilitate oxidation reactions.
- The reaction atmosphere must be carefully controlled to achieve the desired film properties and avoid contamination.
-
Substrate Preparation:
- The substrate's surface condition, including cleanliness, roughness, and crystal orientation, influences the nucleation and growth of the film.
- Proper substrate preparation, such as cleaning and annealing, is essential for achieving high-quality films with good adhesion and uniformity.
- In some cases, the substrate itself acts as a catalyst or participates in the chemical reactions, further emphasizing the importance of substrate selection and preparation.
-
Deposition Time:
- The duration of the CVD process determines the thickness of the deposited film. Longer deposition times generally result in thicker films but may also increase the risk of defects or impurities.
- The optimal deposition time depends on the desired film thickness and the growth rate, which is influenced by other parameters such as temperature and gas flow rate.
-
By-product Removal:
- Efficient removal of gaseous by-products from the reaction chamber is crucial for maintaining a stable deposition environment and preventing contamination.
- This is typically achieved through a combination of gas flow and diffusion processes, ensuring that by-products are continuously removed from the substrate surface and the reaction chamber.
By carefully controlling these parameters, researchers and engineers can optimize the CVD process to produce high-quality thin films with tailored properties for a wide range of applications, from electronics and optics to energy storage and catalysis.
Summary Table:
Parameter | Key Influence | Example/Consideration |
---|---|---|
Temperature | Reaction rate, crystallinity, and substrate integrity | Graphene growth on copper: ~1000°C |
Pressure | Film uniformity and gas-phase reactions | LPCVD for high-quality films, APCVD for cost-effective solutions |
Gas Flow Rate | Growth rate, film thickness, and uniformity | Higher flow rates increase deposition but may cause defects |
Gas Concentration | Stoichiometry, composition, and material properties | CH₄:H₂ ratio critical for graphene layer control |
Catalyst | Activation energy reduction and film quality | Copper and nickel for graphene and carbon nanotube growth |
Reaction Atmosphere | Chemical reactions and film purity | Hydrogen for reduction, oxygen for oxidation |
Substrate Prep | Nucleation, adhesion, and film uniformity | Cleaning and annealing for optimal surface conditions |
Deposition Time | Film thickness and defect risk | Longer times increase thickness but may introduce impurities |
By-product Removal | Deposition stability and contamination prevention | Continuous removal via gas flow and diffusion processes |
Ready to optimize your CVD process? Contact our experts today for tailored solutions!