The Chemical Vapor Deposition (CVD) process is a complex and highly controlled method used to produce high-quality thin films and coatings. The process involves the introduction of gaseous precursors into a reaction chamber, where they undergo chemical reactions to form a solid material on a substrate. The quality and properties of the deposited material are influenced by several key parameters, including temperature, pressure, gas flow rate, and substrate characteristics. These parameters must be carefully monitored and controlled to ensure optimal results. Understanding the interplay between these factors is crucial for achieving the desired material properties and film quality.
Key Points Explained:
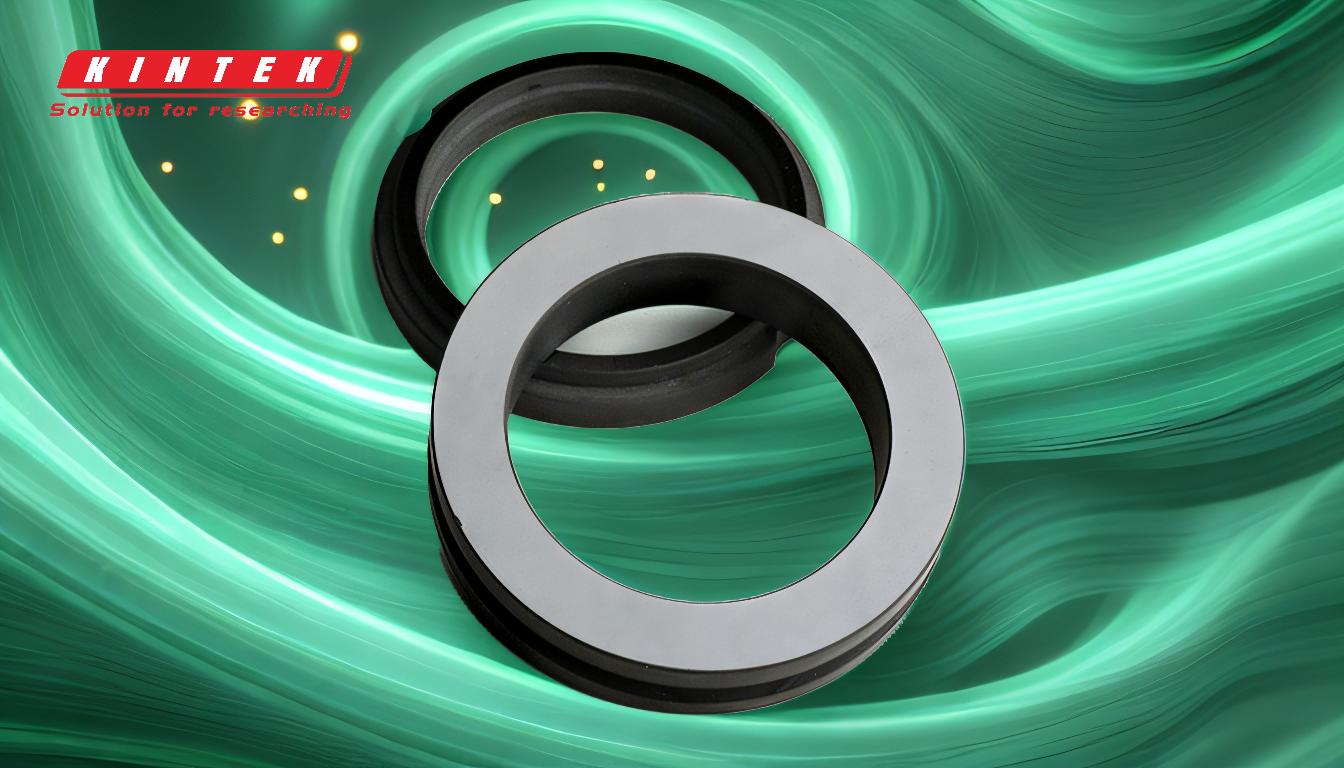
-
Temperature:
- The substrate temperature is one of the most critical parameters in the CVD process. It affects the rate of chemical reactions, the quality of the deposited film, and the adhesion of the film to the substrate.
- Typically, the substrate is heated to a high temperature (around 1000-1100 ˚C) to prepare the surface chemistry and etch passivation. This high temperature is necessary to activate the chemical reactions that lead to the deposition of the desired material.
- Temperature control is also crucial during the cooling phase, which can take 20-30 minutes depending on the substrate material. Improper cooling can lead to defects in the deposited film.
-
Pressure:
- The pressure within the reaction chamber is another key parameter that influences the CVD process. It affects the rate of gas-phase reactions, the diffusion of reactants to the substrate surface, and the removal of byproducts.
- Deposition pressure is usually one of the limiting factors in the CVD process. High pressures can lead to increased reaction rates but may also result in poor film quality due to the formation of defects. Conversely, low pressures can improve film quality but may reduce the deposition rate.
-
Gas Flow Rate:
- The flow rate of the reactant gases into the reaction chamber is critical for controlling the concentration of reactants at the substrate surface. It influences the uniformity and thickness of the deposited film.
- Optimal gas flow rates ensure that the reactants are evenly distributed across the substrate, leading to uniform film growth. Too high or too low flow rates can result in non-uniform deposition or incomplete reactions.
-
Reactant Concentration:
- The chemical composition and concentration of the reactant gases play a significant role in determining the properties of the deposited material. Different precursors can lead to variations in film composition, structure, and properties.
- Controlling the reactant concentration is essential for achieving the desired film characteristics. For example, the introduction of dopants or additional gases can modify the electrical, optical, or mechanical properties of the deposited material.
-
Substrate Characteristics:
- The size, shape, and composition of the substrate can influence the CVD process. The substrate's surface chemistry and morphology affect the nucleation and growth of the deposited film.
- Pre-treatment of the substrate, such as thermal dehydration to remove oxygen impurities, is often necessary to ensure optimal film adhesion and quality.
-
Process Steps:
- The CVD process can be broken down into four main steps:
- Introduction of Reactants: Gaseous precursors are introduced into the reaction chamber containing the substrate.
- Activation of Reactants: Precursors are activated through methods such as thermal energy, plasma, or catalysts.
- Surface Reaction and Deposition: Activated precursors react at the substrate surface to form the desired material.
- Removal of Byproducts: Volatile or non-volatile byproducts are eliminated from the reaction chamber.
- The CVD process can be broken down into four main steps:
-
Kinetics and Mass Transfer:
- The CVD process involves three main steps: surface reaction (kinetics), diffusion (mass transfer), and desorption. The rate of each step can influence the overall deposition rate and film quality.
- Understanding the kinetics and mass transfer processes is essential for optimizing the CVD process and achieving the desired material properties.
-
Economic Considerations:
- The CVD process must also take into account economic factors, such as the cost of precursors, energy consumption, and equipment maintenance. Optimizing these factors can lead to more cost-effective production without compromising film quality.
In summary, the CVD process is governed by a complex interplay of parameters, including temperature, pressure, gas flow rate, reactant concentration, and substrate characteristics. Careful control and optimization of these parameters are essential for producing high-quality thin films and coatings with the desired properties.
Summary Table:
Parameter | Role in CVD Process | Optimal Conditions |
---|---|---|
Temperature | Affects reaction rate, film quality, and adhesion. | Typically 1000-1100 ˚C for activation; controlled cooling to prevent defects. |
Pressure | Influences gas-phase reactions, diffusion, and byproduct removal. | Balanced to optimize reaction rate and film quality. |
Gas Flow Rate | Controls reactant concentration and film uniformity. | Adjusted for even distribution and complete reactions. |
Reactant Concentration | Determines film composition, structure, and properties. | Precise control for desired characteristics, e.g., dopants for electrical properties. |
Substrate Characteristics | Affects nucleation, growth, and adhesion of the film. | Pre-treated to remove impurities and ensure optimal surface chemistry. |
Need help optimizing your CVD process? Contact our experts today for tailored solutions!