The hot pressing process is a specialized manufacturing technique that combines heat and pressure to produce high-density materials, often used in the production of ceramics, metals, and composites. The process involves several sequential steps, starting with the preparation of the powder material, followed by loading it into a press, applying heat and pressure simultaneously to achieve densification, and finally cooling the material to solidify its structure. This method is advantageous because it reduces the time required for phase changes and alloy formation compared to traditional sintering methods. The steps are designed to ensure the removal of impurities, proper bonding of particles, and the creation of a dense, uniform final product.
Key Points Explained:
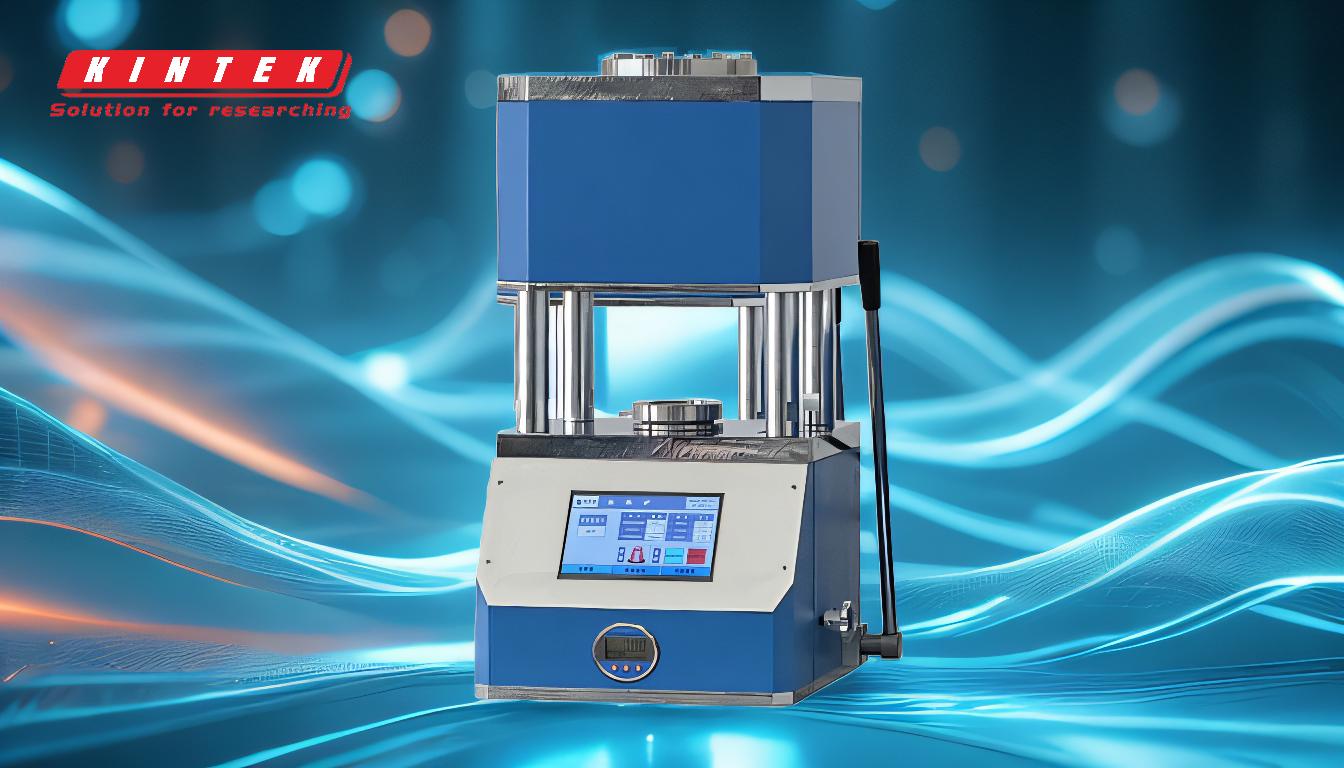
-
Powder Preparation:
- Atomization or Milling: The process begins with the production of fine powder particles through methods like atomization (breaking down molten metal into fine droplets) or milling (grinding solid materials into powder). This step ensures that the powder has the desired particle size and distribution.
- Blending and Mixing: The powders are then blended and mixed to achieve a homogeneous mixture. This is crucial for ensuring uniform properties in the final product. Additives or binders may also be included at this stage to improve the flowability or compressibility of the powder.
-
Charging:
- Loading the Powder: The prepared powder is loaded into a graphite mold or die, which is then placed inside the hot press furnace. The mold is designed to withstand high temperatures and pressures while maintaining the desired shape of the final product.
-
Vacuuming:
- Removing Gases and Impurities: The furnace is evacuated to create a vacuum, which helps remove any trapped gases, moisture, or impurities from the powder. This step is critical for preventing defects such as porosity or oxidation during the heating and pressing stages.
-
Heating:
- Raising the Temperature: The furnace is heated to a specific temperature, typically close to or above the melting point of the powder material. The heat softens the powder particles, allowing them to bond more effectively under pressure. The temperature must be carefully controlled to avoid overheating or underheating, which could compromise the material's integrity.
-
Pressurization:
- Applying Pressure: Simultaneously with heating, pressure is applied to the powder using hydraulic or mechanical means. This pressure aids in the densification of the material by forcing the particles closer together, reducing voids, and promoting particle bonding. The combination of heat and pressure accelerates the sintering process, leading to faster densification and a more uniform structure.
-
Cooling:
- Gradual Cooling: After the desired density and bonding are achieved, the material is gradually cooled to room temperature. Controlled cooling is essential to prevent thermal stresses or cracking in the final product. The cooling rate may vary depending on the material and its intended application.
-
Optional Secondary Processes:
- Infiltration or Finishing: In some cases, additional processes such as infiltration (filling pores with a secondary material) or surface finishing (polishing, coating) may be performed to enhance the properties or appearance of the final product. These steps are optional and depend on the specific requirements of the application.
By following these steps, the hot pressing process produces materials with high density, excellent mechanical properties, and uniform microstructure, making it a preferred method for manufacturing advanced materials in industries such as aerospace, automotive, and electronics.
Summary Table:
Step | Description |
---|---|
Powder Preparation | Atomization or milling to create fine powder; blending for uniformity. |
Charging | Loading powder into a graphite mold designed for high heat and pressure. |
Vacuuming | Evacuating the furnace to remove gases and impurities, preventing defects. |
Heating | Raising temperature to soften particles for effective bonding. |
Pressurization | Applying pressure to densify the material and reduce voids. |
Cooling | Gradual cooling to solidify the structure and prevent thermal stress. |
Secondary Processes | Optional steps like infiltration or finishing to enhance material properties. |
Discover how the hot pressing process can elevate your material production—contact us today for expert guidance!