Brazing is a metal-joining process that involves melting a filler metal into a joint to bond two pieces of metal together. The process typically includes several key steps: preparation of the materials, assembly and alignment of the parts, application of flux (if necessary), heating to the brazing temperature, application of the filler metal, cooling, and finally, inspection of the joint. Each step is crucial to ensure a strong, durable bond between the metal pieces. The process can vary slightly depending on the materials being joined and the specific brazing method used, such as torch brazing, furnace brazing, or vacuum brazing.
Key Points Explained:
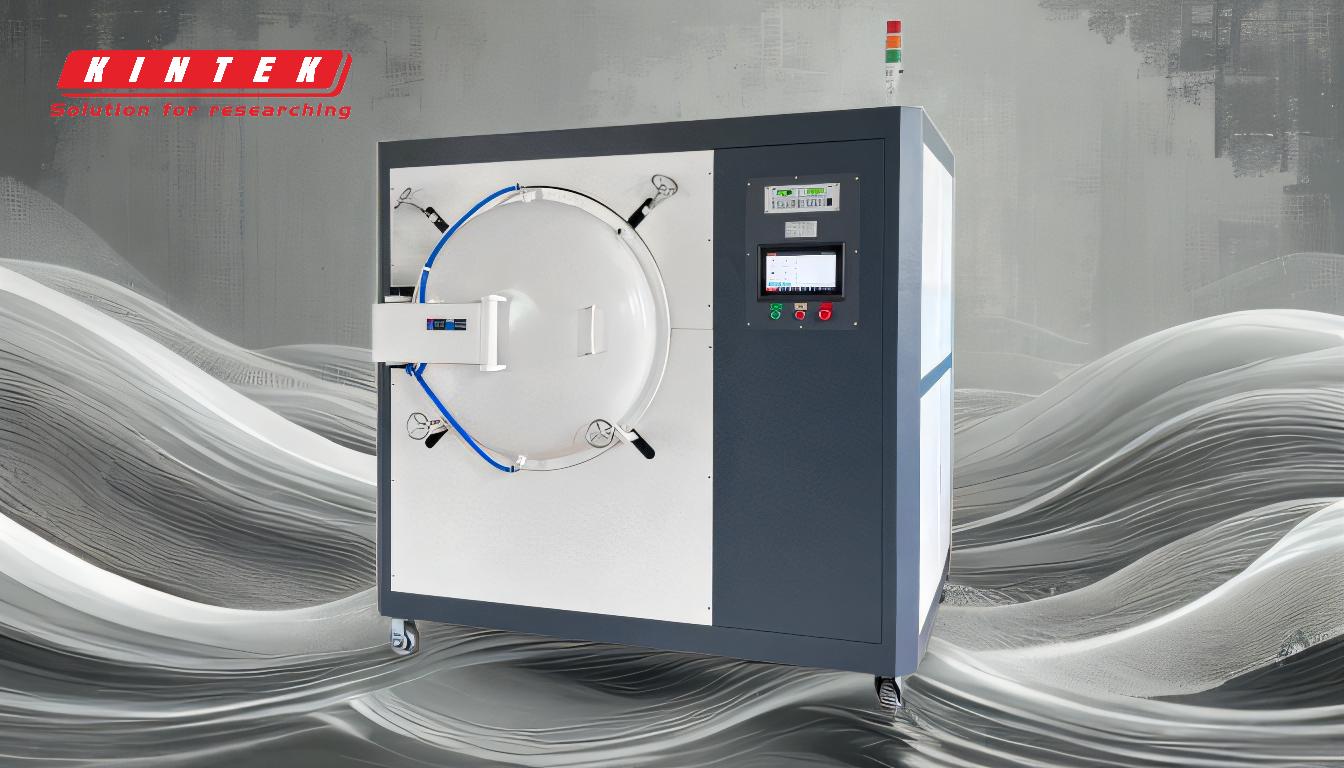
-
Preparation Before Brazing:
- Cleaning: The metal surfaces to be brazed must be thoroughly cleaned to remove any oxides, oils, or contaminants. This ensures proper wetting and flow of the filler metal.
- Surface Roughening: In some cases, the surfaces may be roughened to improve adhesion of the filler metal.
- Flux Application: Depending on the brazing method and materials, a flux may be applied to prevent oxidation and promote the flow of the filler metal. For example, in air brazing, special fluxes are used to prevent oxidation.
-
Assembly and Filling with Filler Metal:
- Alignment: The parts to be joined are carefully aligned and held in place using fixtures or clamps. Proper alignment is critical to ensure a strong joint.
- Filler Metal Placement: The filler metal, which has a lower melting point than the base metals, is placed near or in the joint. The filler metal can be in the form of wire, foil, or pre-placed rings.
- Heating: The assembly is heated to the brazing temperature, which is above the melting point of the filler metal but below the melting point of the base metals. The heat source can be a torch, furnace, or induction coil. In some cases, such as vacuum brazing, the process is performed in a controlled atmosphere to prevent oxidation.
-
Inspection of the Brazed Joint:
- Visual Inspection: After cooling, the joint is visually inspected for defects such as cracks, voids, or incomplete filling.
- Non-Destructive Testing: Techniques like X-ray, ultrasonic testing, or dye penetrant inspection may be used to detect internal defects or discontinuities.
- Mechanical Testing: In some cases, the joint may be tested for strength, ductility, or other mechanical properties to ensure it meets the required specifications.
-
Cooling:
- Controlled Cooling: After the brazing process, the assembly is allowed to cool. Controlled cooling is important to prevent thermal stresses that could lead to cracking or distortion.
- Post-Brazing Treatments: In some cases, additional treatments such as tempering may be required to achieve the desired material properties. For example, tempering can reduce brittleness in hardened steel and remove internal strains caused by sudden cooling during quenching.
-
Special Considerations:
- Atmosphere Control: In processes like vacuum brazing or brazing in a reducing atmosphere (e.g., pure hydrogen or dissociated ammonia), the environment is carefully controlled to prevent oxidation and ensure a clean joint.
- Material Compatibility: The choice of filler metal and flux must be compatible with the base metals to ensure a strong bond and avoid issues like galvanic corrosion.
By following these steps meticulously, a high-quality brazed joint can be achieved, ensuring the integrity and longevity of the metal assembly.
Summary Table:
Step | Key Actions |
---|---|
Preparation | Clean surfaces, roughen if needed, apply flux (if required). |
Assembly & Filling | Align parts, place filler metal, heat to brazing temperature. |
Inspection | Visually inspect, use non-destructive testing, and perform mechanical testing. |
Cooling | Allow controlled cooling; apply post-brazing treatments if necessary. |
Special Considerations | Control atmosphere, ensure material compatibility. |
Need expert advice on brazing? Contact us today for tailored solutions!