The sintering process is a method of forming solid objects from powdered materials by applying heat and pressure without melting the materials completely. It is widely used in industries such as ceramics, metals, and plastics to create products with high structural integrity and strength. The process typically involves three main stages: powder composition, powder compaction, and sintering (heating). Each stage is critical to ensuring the final product's quality and properties. Powder composition involves mixing and preparing the raw materials, compaction shapes the powder into the desired form, and sintering fuses the particles together through controlled heating and cooling. This process relies on atomic diffusion to bond particles, resulting in a dense and cohesive structure.
Key Points Explained:
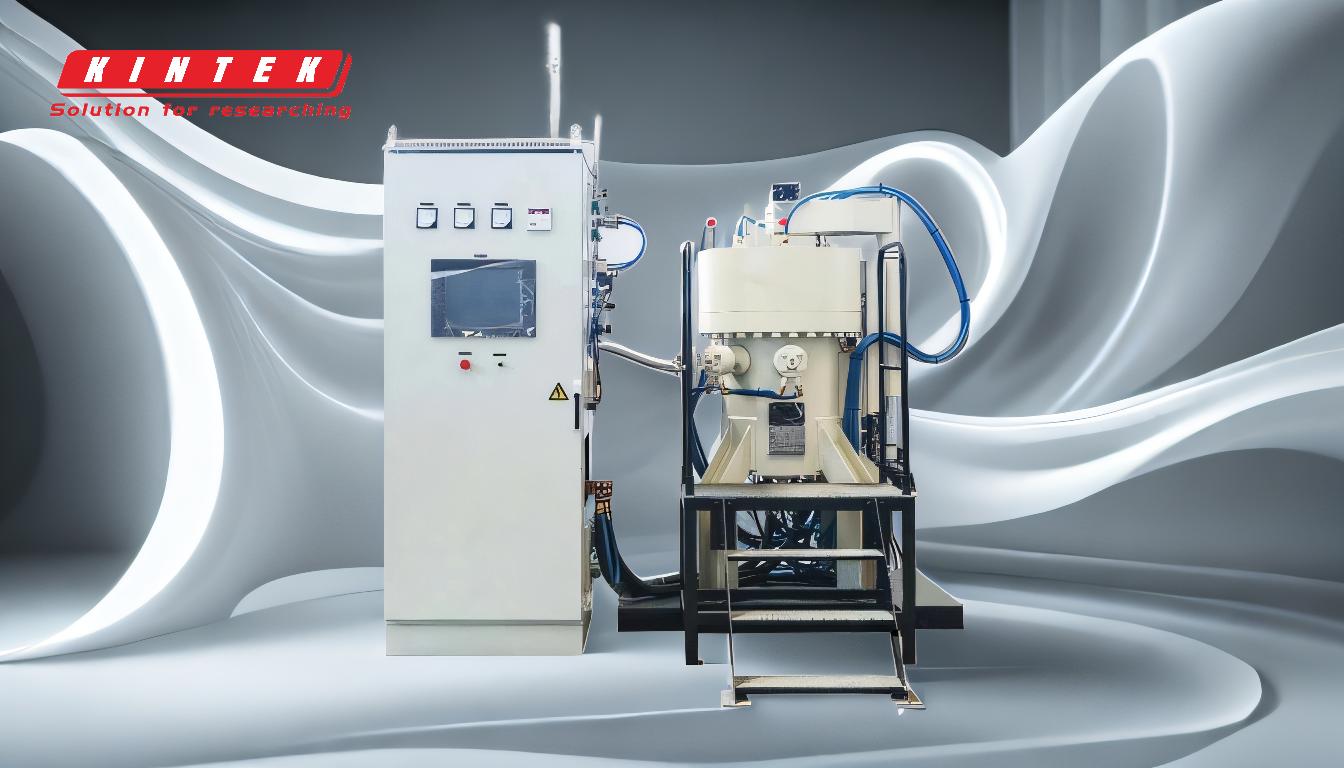
-
Powder Composition (Mixing and Preparation)
- This is the initial stage where the raw materials, such as metal, ceramic, or plastic powders, are carefully selected and mixed.
- Additives like binders, deflocculants, and coupling agents may be included to improve the powder's properties, such as flowability and bonding strength.
- The mixture is often processed into a slurry, which is then spray-dried to form a free-flowing powder ready for compaction.
- The composition determines the final material's properties, such as strength, porosity, and thermal resistance.
-
Powder Compaction (Shaping the Powder)
- The prepared powder is compacted into the desired shape using mechanical pressure. This can be done through cold or hot pressing, depending on the material and application.
- Compaction eliminates voids and ensures uniformity in the green part (the unfired, compacted shape).
- The green part is fragile at this stage and requires careful handling to avoid damage before sintering.
-
Sintering (Heating and Bonding)
- The green part is heated in a furnace at temperatures below the material's melting point. This prevents liquefaction while enabling atomic diffusion.
- During heating, particles bond through solid-state diffusion, forming necks between particles and reducing porosity.
- The sintering process is carefully controlled to achieve the desired density, strength, and microstructure.
- After sintering, the part is cooled gradually to solidify into a rigid and cohesive structure.
-
Cooling and Finalization
- Cooling is a critical step that allows the sintered part to solidify and stabilize.
- The cooling rate can influence the final properties of the material, such as hardness and thermal resistance.
- Once cooled, the sintered product is ready for post-processing, such as machining, coating, or polishing, depending on the application.
By following these steps, the sintering process transforms loose powder into a durable and functional product, leveraging heat and pressure to create strong, cohesive materials.
Summary Table:
Stage | Description |
---|---|
Powder Composition | Mixing raw materials and additives to prepare a free-flowing powder. |
Powder Compaction | Shaping the powder into the desired form using mechanical pressure. |
Sintering (Heating) | Heating the compacted powder to bond particles through atomic diffusion. |
Cooling | Gradual cooling to solidify and stabilize the sintered part. |
Discover how sintering can enhance your manufacturing process—contact our experts today!