A vacuum furnace is a highly specialized piece of equipment used in various industrial processes, particularly in heat treatment, sintering, and brazing. It operates in a vacuum environment to prevent oxidation and contamination of the materials being processed. The furnace is composed of several critical parts, each serving a specific function to ensure efficient and precise operation. These parts include the furnace body, vacuum system, heating elements, temperature control system, cooling system, and more. Understanding these components is essential for anyone involved in the purchase, operation, or maintenance of a vacuum furnace.
Key Points Explained:
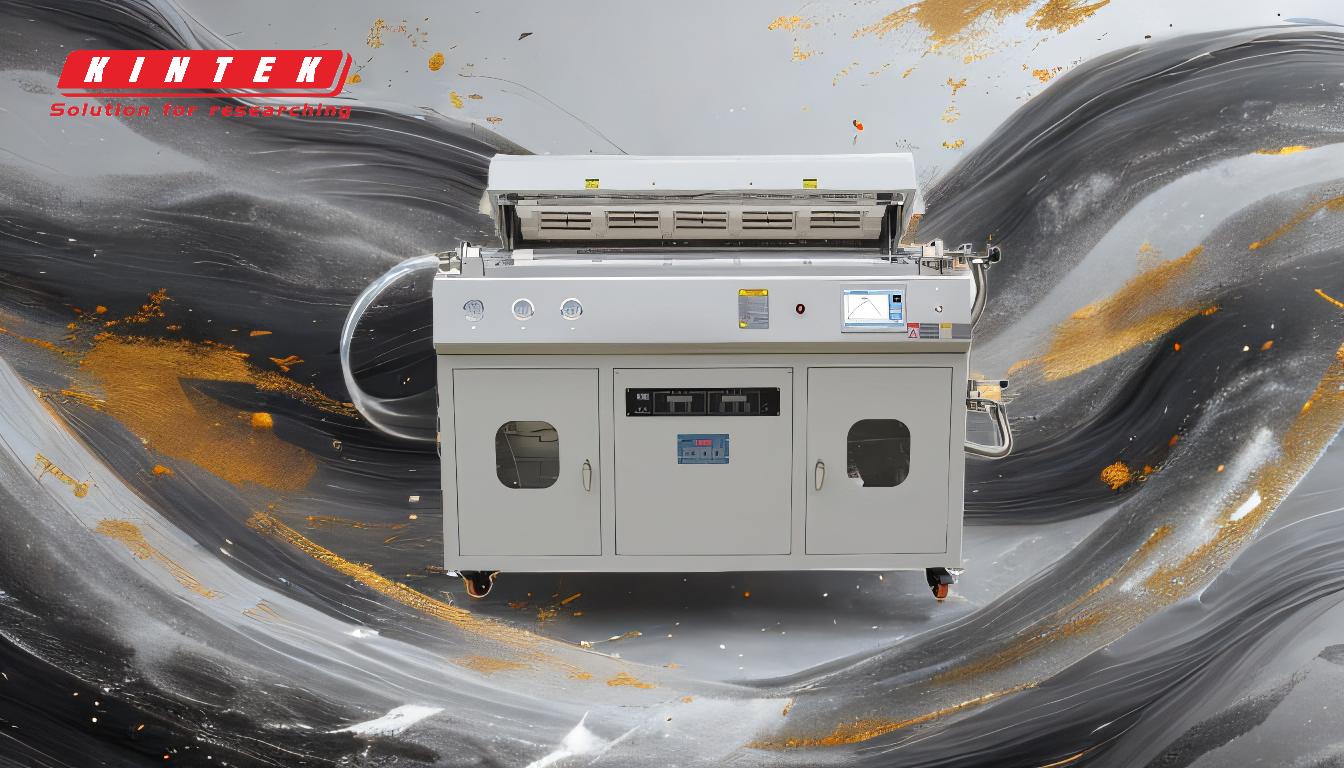
-
Furnace Body and Shell:
- The furnace body is typically constructed from high-strength steel plates, often with a double-layer water jacket structure to enhance durability and thermal management. The shell is usually welded using carbon steel or stainless steel, with removable parts sealed using vacuum sealing materials. This design ensures an airtight environment, which is crucial for maintaining the vacuum. The shell is also cooled by water or air to prevent deformation and degradation of sealing materials due to high temperatures.
-
Heating Elements:
- Heating elements are critical for achieving the desired temperatures within the furnace. Common materials used for heating elements include tungsten, platinum, and graphite, chosen for their high-temperature resistance, low vapor pressure, and good thermal conductivity. These elements must ensure rapid heating rates, minimal heat loss, and stable performance over time. The choice of material also depends on the chemical properties required for processing specific products to avoid affecting the quality of the workpiece.
-
Vacuum System:
- The vacuum system is essential for creating and maintaining the vacuum environment inside the furnace. It typically operates in the 10-2 Torr range and includes components such as vacuum pumps, vacuum valves, vacuum measuring instruments, and pipelines. The system often uses a two-stage rotary vane pump to remove oxygen and other gases from the chamber, ensuring an airtight seal. Additional components like vacuum gauge controllers, electro-pneumatic vacuum valves, and leak check valves are also part of this system.
-
Temperature Control System:
- Precision in temperature control is vital for the success of processes conducted in a vacuum furnace. The temperature control system includes sensors, controllers, and power supply systems that work together to achieve and maintain the desired temperature. This system ensures uniform heating and cooling rates, which are crucial for the quality of the processed materials.
-
Cooling System:
- The cooling system is designed to manage the thermal load within the furnace, preventing overheating and ensuring the longevity of the furnace components. It often includes water or air cooling mechanisms for the furnace shell and other critical parts. In some designs, inert gases like argon are cycled into the chamber to cool the components without causing chemical reactions, which is particularly important for sensitive materials.
-
Hydraulic System:
- In some vacuum furnace designs, particularly those used in vacuum hot press furnaces, a hydraulic system is employed to apply pressure during the processing of materials. This system works in conjunction with the vacuum and heating systems to achieve specific material properties, such as increased density or improved mechanical strength.
-
Control System:
- The control system integrates various components of the vacuum furnace, including the vacuum system, heating elements, temperature control, and cooling system. It allows for automated operation, precise control over process parameters, and monitoring of the furnace's performance. This system often includes a user interface for easy operation and data logging for process optimization and quality control.
-
Insulation and Heat Shields:
- Insulation materials and heat shields are used to minimize heat loss and protect the furnace structure from high temperatures. Materials like high-grade carbon felt and flexible graphite paper are commonly used for insulation due to their high-temperature resistance and low thermal conductivity. These materials ensure that the heat is concentrated within the heating chamber, improving energy efficiency and process consistency.
-
Furnace Frame and Structural Components:
- The furnace frame provides structural support for all the components of the vacuum furnace. It is designed to withstand the mechanical stresses and thermal loads encountered during operation. The frame also houses other structural components like the furnace cover, furnace bottom, and automatic charging and deflating systems, which facilitate the loading and unloading of materials.
-
Power Supply and Transformers:
- The power supply system is responsible for delivering the necessary electrical energy to the heating elements and other electrical components of the furnace. Transformers and connecting copper bars are used to manage the power distribution and ensure stable operation. This system must be designed to handle the high power demands of the furnace while maintaining safety and efficiency.
Understanding these key components of a vacuum furnace is essential for anyone involved in its purchase, operation, or maintenance. Each part plays a crucial role in ensuring the furnace's performance, reliability, and the quality of the processed materials. For more detailed information on vacuum furnaces, you can visit vacuum furnace.
Summary Table:
Component | Function |
---|---|
Furnace Body and Shell | Provides structural integrity and airtight environment for vacuum operation |
Heating Elements | Achieve and maintain high temperatures for material processing |
Vacuum System | Creates and maintains a vacuum to prevent oxidation and contamination |
Temperature Control System | Ensures precise and uniform heating and cooling rates |
Cooling System | Manages thermal load to prevent overheating and prolong furnace life |
Hydraulic System | Applies pressure for specific material properties in certain designs |
Control System | Integrates and automates furnace operations for precise process control |
Insulation and Heat Shields | Minimizes heat loss and protects furnace components from high temperatures |
Furnace Frame | Supports all components and withstands mechanical and thermal stresses |
Power Supply and Transformers | Delivers electrical energy for stable and efficient furnace operation |
Ready to optimize your heat treatment process? Contact our experts today to learn more about vacuum furnace solutions!