Sintering of ceramics is a critical process that transforms powdered ceramic materials into dense, solid bodies by applying heat, often below the material's melting point. During sintering, the powder particles undergo material migration and grain boundary movement, leading to densification and the formation of a strong, durable ceramic body. This process reduces porosity, causes shrinkage, and consolidates the powdery structure into a cohesive mass. Sintering is essential in manufacturing ceramic objects like pottery and is optimized to achieve desired physical properties such as strength, hardness, and durability.
Key Points Explained:
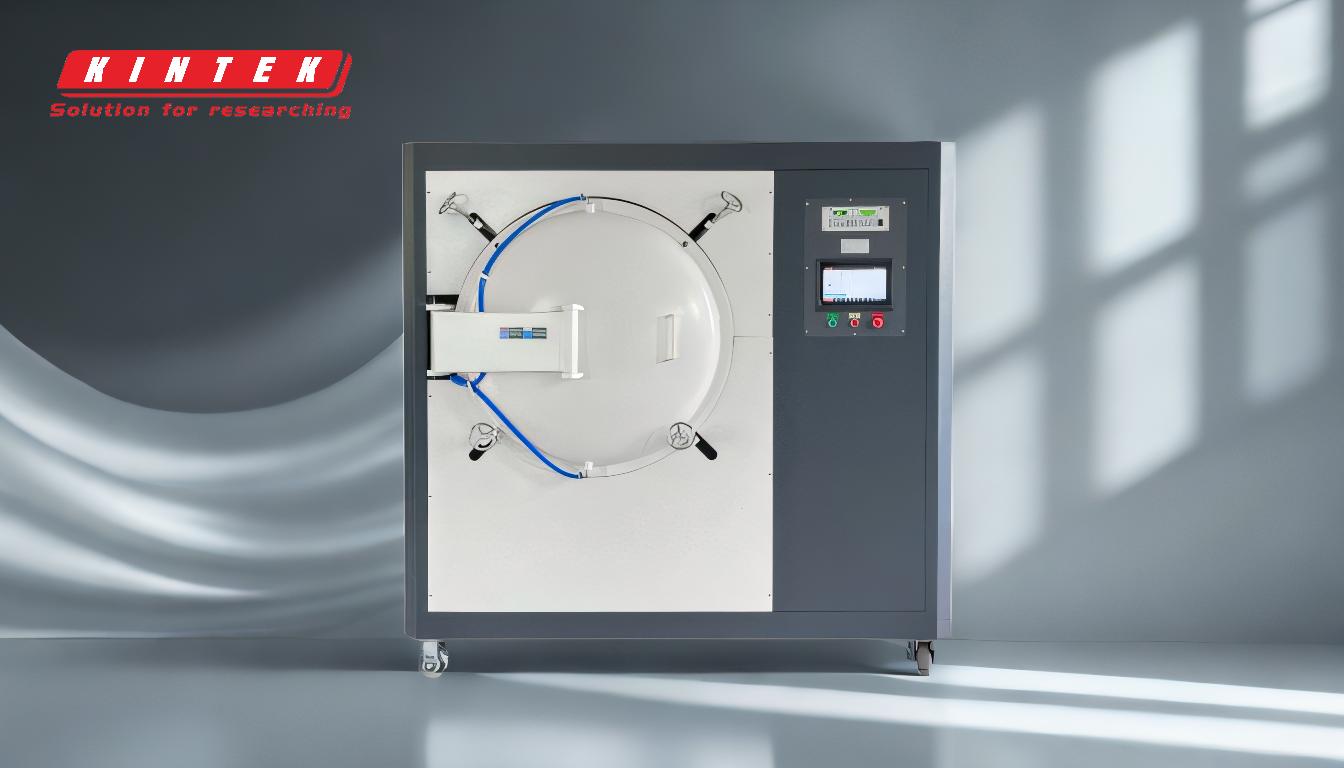
-
Definition and Purpose of Sintering:
- Sintering is a manufacturing process used to compact and densify ceramic powders by applying heat and sometimes pressure, without reaching the material's melting point.
- The primary goal is to transform loose powder particles into a solid, dense, and durable ceramic body with reduced porosity and improved mechanical properties.
-
Stages of the Sintering Process:
-
Initial Stage:
- Powder particles are pressed into a "green" compact, which has a porous structure and limited strength.
- The particles are in close contact but not yet bonded.
-
Intermediate Stage:
- Heat is applied, causing material migration and diffusion at the particle boundaries.
- Grain boundaries begin to form, and the material starts to densify.
-
Final Stage:
- Porosity is significantly reduced, and the material shrinks as the particles fuse together.
- The ceramic body gains strength and density, forming a cohesive structure.
-
Initial Stage:
-
Material Migration and Densification:
- During sintering, atoms from the powder particles diffuse across particle boundaries, driven by high temperatures.
- This diffusion causes the particles to bond together, reducing voids and porosity.
- Grain growth occurs as smaller grains merge into larger ones, further strengthening the material.
-
Role of Temperature and Atmosphere:
- Sintering occurs at temperatures below the material's melting point, typically in a controlled atmosphere (e.g., air, nitrogen, or vacuum).
- The temperature must be carefully optimized to ensure proper diffusion and bonding without causing defects like warping or cracking.
- The atmosphere prevents oxidation or contamination, ensuring the ceramic retains its desired properties.
-
Shrinkage and Porosity Reduction:
- As the particles bond and densify, the material undergoes shrinkage, which must be accounted for in the design of the final product.
- Porosity decreases as voids between particles are eliminated, resulting in a denser and stronger ceramic body.
-
Applications of Sintering in Ceramics:
- Sintering is widely used in the production of pottery, tiles, and advanced ceramics for industrial applications.
- It is also employed in powder metallurgy for metals and other high-melting-point materials like tungsten and molybdenum.
-
Optimization of the Sintering Process:
- The sintering process must be carefully controlled to achieve the desired physical properties, such as strength, hardness, and thermal stability.
- Factors like temperature, heating rate, pressure, and atmosphere are optimized to ensure consistent and high-quality results.
-
Benefits of Sintering:
- Produces strong, durable, and hard ceramic materials.
- Reduces porosity and improves mechanical properties.
- Enables the creation of complex shapes and structures that are difficult to achieve through other manufacturing methods.
By understanding these key points, a purchaser of ceramic equipment or consumables can appreciate the importance of sintering in achieving high-quality ceramic products and make informed decisions about materials and processes.
Summary Table:
Key Aspect | Details |
---|---|
Definition | A process to compact and densify ceramic powders using heat and pressure. |
Stages | Initial (green compact), Intermediate (material migration), Final (fusion). |
Key Factors | Temperature, atmosphere, heating rate, and pressure. |
Benefits | Strong, durable ceramics with reduced porosity and complex shapes. |
Applications | Pottery, tiles, advanced ceramics, and powder metallurgy. |
Discover how sintering can enhance your ceramic production—contact our experts today for tailored solutions!