Hardening is a heat treatment process used to increase the hardness of metals, particularly steel, by altering their microstructure. This process involves heating the metal to a specific temperature, holding it at that temperature to allow for uniform heating, and then rapidly cooling it through quenching. The rapid cooling transforms the microstructure, typically from austenite to martensite, which is much harder and stronger. However, this also makes the metal more brittle. To reduce brittleness and improve toughness, a subsequent tempering process is often employed. Hardening is widely used in industries where high wear resistance and strength are required, such as in tools, gears, and structural components.
Key Points Explained:
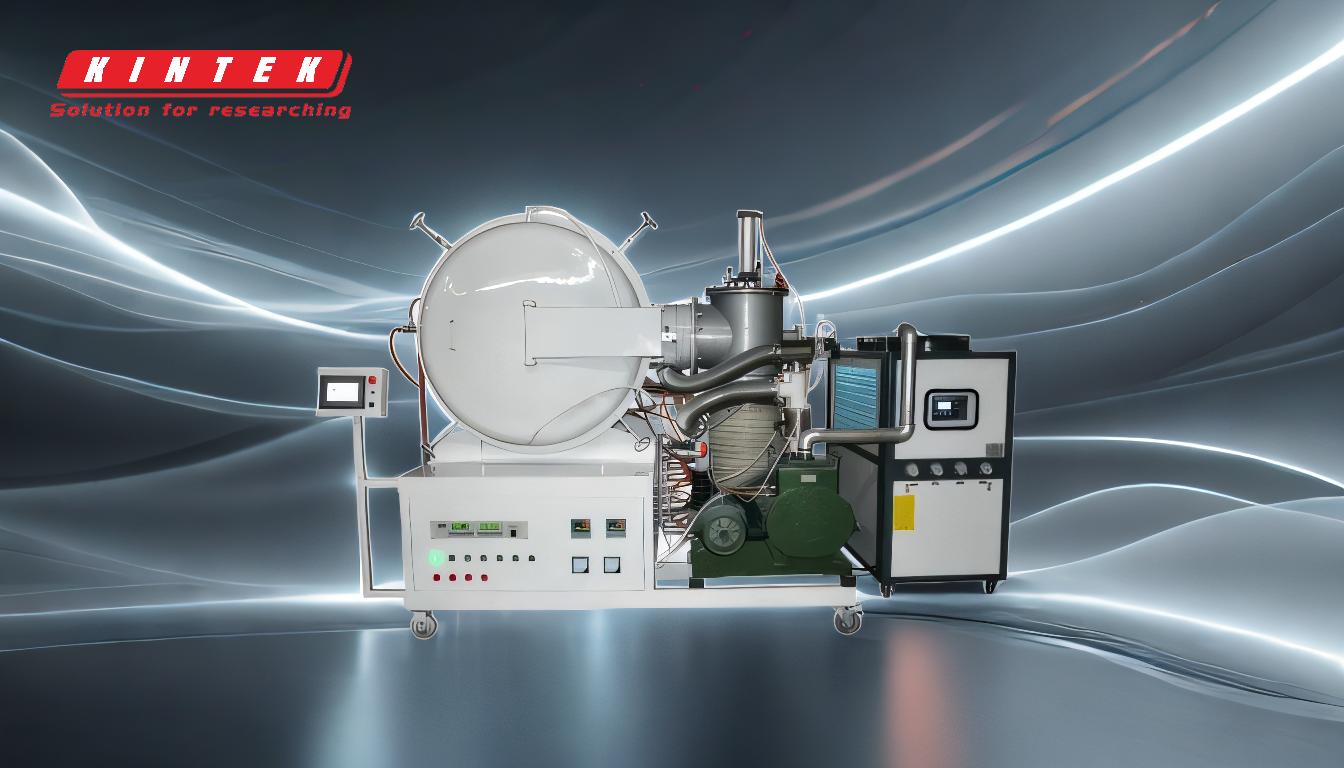
-
Purpose of Hardening:
- The primary goal of hardening is to increase the hardness and strength of metals, particularly steel. This is achieved by altering the metal's microstructure, which enhances its ability to resist deformation and wear.
-
Heating Phase:
- The metal is heated to a specific temperature, known as the austenitizing temperature, which is typically above the critical temperature for the material. This temperature varies depending on the type of steel or metal being treated. The heating phase ensures that the metal's microstructure transforms into austenite, a phase that is more receptive to hardening.
-
Holding at Temperature:
- After reaching the austenitizing temperature, the metal is held at that temperature for a period of time. This allows for uniform heating throughout the material, ensuring that the entire piece reaches the desired microstructure before quenching.
-
Quenching:
- Quenching is the rapid cooling of the metal, typically in water, oil, or air, depending on the material and desired properties. This rapid cooling transforms the austenite into martensite, a very hard and brittle microstructure. The rate of cooling is critical; too slow, and the desired hardness may not be achieved, too fast, and the metal may crack or warp.
-
Formation of Martensite:
- Martensite is a supersaturated solid solution of carbon in iron, characterized by its needle-like microstructure. It is much harder and stronger than the original microstructure but also more brittle. The formation of martensite is the key to achieving the increased hardness in the metal.
-
Brittleness and Tempering:
- While martensite provides high hardness, it also makes the metal more brittle. To reduce brittleness and improve toughness, the metal is often subjected to a tempering process after hardening. Tempering involves reheating the metal to a temperature below the austenitizing temperature and then cooling it slowly. This process reduces some of the hardness but significantly increases the metal's toughness and ductility.
-
Applications of Hardening:
- Hardening is widely used in the manufacturing of tools, gears, bearings, and structural components where high wear resistance and strength are required. It is also used in the automotive and aerospace industries to enhance the performance and longevity of critical components.
-
Types of Hardening Processes:
- There are several types of hardening processes, including through hardening, case hardening, and induction hardening. Through hardening involves hardening the entire piece of metal, while case hardening only hardens the surface layer, leaving the core relatively soft. Induction hardening uses electromagnetic induction to heat the metal, followed by rapid cooling, and is often used for localized hardening of specific areas.
-
Considerations and Challenges:
- The hardening process must be carefully controlled to avoid issues such as cracking, warping, or uneven hardness. The choice of quenching medium, heating rate, and cooling rate are all critical factors that influence the final properties of the metal. Additionally, the composition of the metal, including its carbon content, plays a significant role in determining the effectiveness of the hardening process.
By understanding these key points, one can appreciate the complexity and importance of the hardening process in metallurgy and its critical role in enhancing the properties of metals for various industrial applications.
Summary Table:
Key Aspect | Description |
---|---|
Purpose | Increases hardness and strength by altering metal microstructure. |
Heating Phase | Metal is heated to austenitizing temperature to transform microstructure. |
Holding at Temperature | Ensures uniform heating for consistent microstructure transformation. |
Quenching | Rapid cooling transforms austenite into hard, brittle martensite. |
Tempering | Reduces brittleness and improves toughness by reheating at lower temperatures. |
Applications | Used in tools, gears, bearings, and structural components for wear resistance. |
Types of Hardening | Includes through hardening, case hardening, and induction hardening. |
Challenges | Requires precise control to avoid cracking, warping, or uneven hardness. |
Discover how hardening can enhance your metal components—contact us today for expert advice!