A joint in brazing refers to the connection formed between two or more materials using a filler metal that has a lower melting point than the base materials being joined. The process involves heating the base materials to a temperature above the melting point of the filler metal but below the melting point of the base materials, allowing the filler metal to flow into the joint by capillary action. Once cooled, the filler metal solidifies, creating a strong, durable, and often leak-proof bond. Brazing is widely used in industries such as automotive, aerospace, and HVAC due to its ability to join dissimilar materials and produce high-strength joints with minimal distortion.
Key Points Explained:
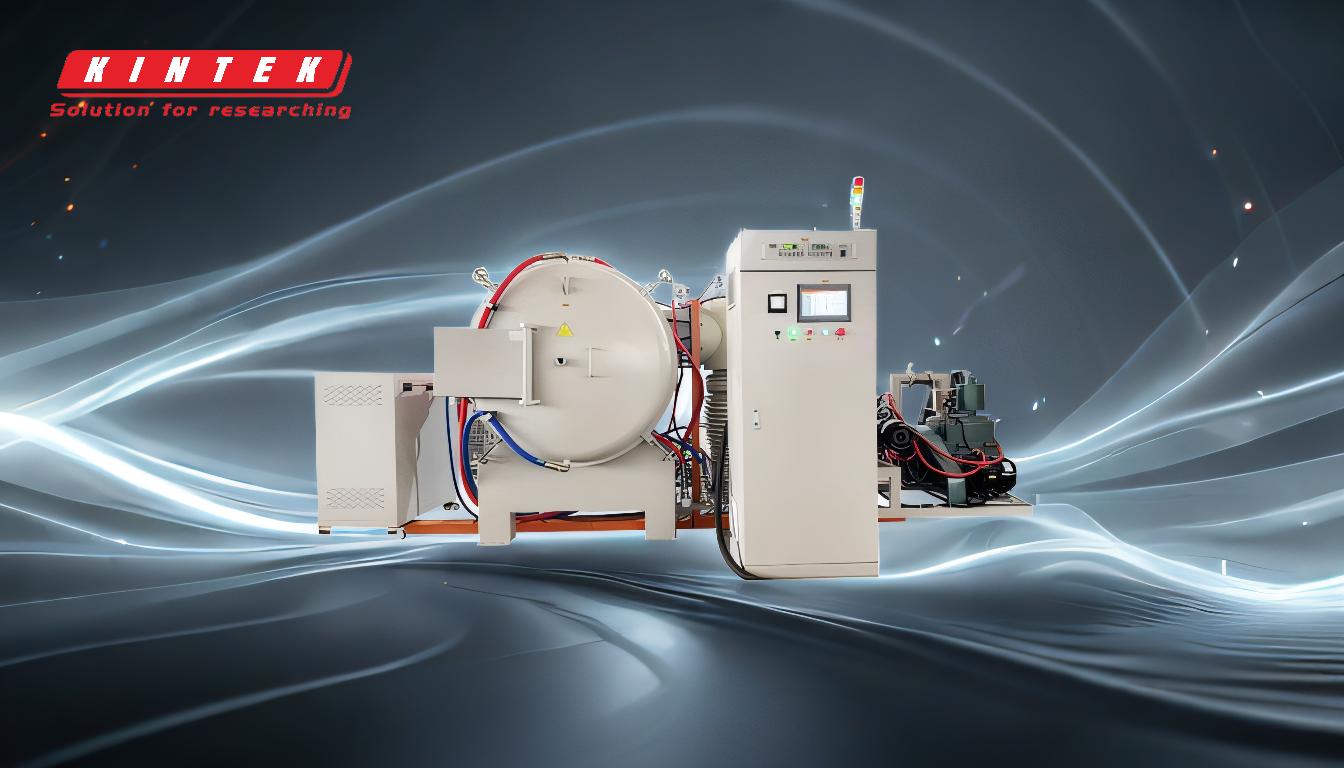
-
Definition of a Brazed Joint:
- A brazed joint is a metallurgical bond created between two or more materials using a filler metal. The filler metal melts at a temperature lower than the base materials but flows into the joint due to capillary action, forming a strong and durable connection upon cooling.
-
Components of a Brazed Joint:
- Base Materials: These are the primary materials being joined, which can be metals or ceramics. Common base materials include steel, copper, aluminum, and titanium.
- Filler Metal: The filler metal is chosen based on its compatibility with the base materials and its melting point. Common filler metals include silver alloys, copper-phosphorus alloys, and nickel-based alloys.
- Flux: Flux is often used to clean the surfaces of the base materials and prevent oxidation during the brazing process. It also helps the filler metal flow more easily into the joint.
-
How a Brazed Joint is Formed:
- The process begins by cleaning the surfaces of the base materials to remove any contaminants.
- The filler metal and flux are applied to the joint area.
- The assembly is heated to a temperature above the melting point of the filler metal but below the melting point of the base materials.
- The filler metal melts and flows into the joint by capillary action, filling the gaps between the base materials.
- The assembly is then cooled, allowing the filler metal to solidify and form a strong bond.
-
Types of Brazed Joints:
- Butt Joint: The simplest type of joint, where the ends of two materials are joined together in a straight line.
- Lap Joint: One material overlaps the other, providing a larger surface area for the filler metal to bond.
- T-Joint: One material is joined to the middle of another material at a right angle.
- Corner Joint: Two materials are joined at a corner, typically at a 90-degree angle.
-
Advantages of Brazed Joints:
- Strength: Brazed joints are strong and can often withstand high stress and strain.
- Versatility: Brazing can join dissimilar materials, such as metals to ceramics, which is difficult to achieve with other joining methods.
- Leak-Proof: Brazed joints are often used in applications where a leak-proof seal is required, such as in HVAC systems.
- Minimal Distortion: Since the base materials are not melted, there is minimal distortion or warping during the brazing process.
-
Applications of Brazed Joints:
- Automotive Industry: Brazed joints are used in the manufacturing of radiators, heat exchangers, and air conditioning systems.
- Aerospace Industry: The high strength and reliability of brazed joints make them ideal for use in aircraft engines and structural components.
- HVAC Systems: Brazed joints are commonly used in the construction of heat exchangers and refrigeration systems due to their leak-proof nature.
- Electronics: Brazing is used to join components in electronic devices, where precision and reliability are critical.
-
Considerations for Brazing:
- Joint Design: The design of the joint is critical to the success of the brazing process. Proper joint design ensures that the filler metal can flow into the joint and form a strong bond.
- Temperature Control: Precise temperature control is necessary to ensure that the filler metal melts and flows properly without overheating the base materials.
- Material Compatibility: The filler metal must be compatible with the base materials to ensure a strong bond and prevent issues such as galvanic corrosion.
In summary, a brazed joint is a critical component in many industrial applications, offering a strong, durable, and versatile method of joining materials. Understanding the components, formation process, and advantages of brazed joints is essential for anyone involved in the design or manufacturing of products that require reliable and high-strength connections.
Summary Table:
Aspect | Details |
---|---|
Definition | A metallurgical bond using a filler metal with a lower melting point. |
Components | Base materials, filler metal, and flux. |
Formation Process | Heating, capillary action, and cooling to create a strong bond. |
Types of Joints | Butt, Lap, T-Joint, and Corner Joints. |
Advantages | High strength, versatility, leak-proof, and minimal distortion. |
Applications | Automotive, aerospace, HVAC, and electronics industries. |
Key Considerations | Joint design, temperature control, and material compatibility. |
Need expert advice on brazing joints? Contact us today to learn more!