A ceramic furnace, also known as a ceramic kiln or muffle furnace, is a specialized heating device designed for high-temperature processes such as firing, sintering, melting, and testing ceramic materials. These furnaces are essential in industries like ceramics, metallurgy, and materials science, as they provide precise temperature control and uniform heating to ensure the quality and durability of ceramic products. Modern ceramic furnaces are equipped with advanced features such as PID temperature control, vacuum systems, insulation materials, and safety mechanisms to optimize performance and efficiency. They are constructed using refractory materials to withstand extreme temperatures and are often used for continuous, long-term operations in laboratories and industrial settings.
Key Points Explained:
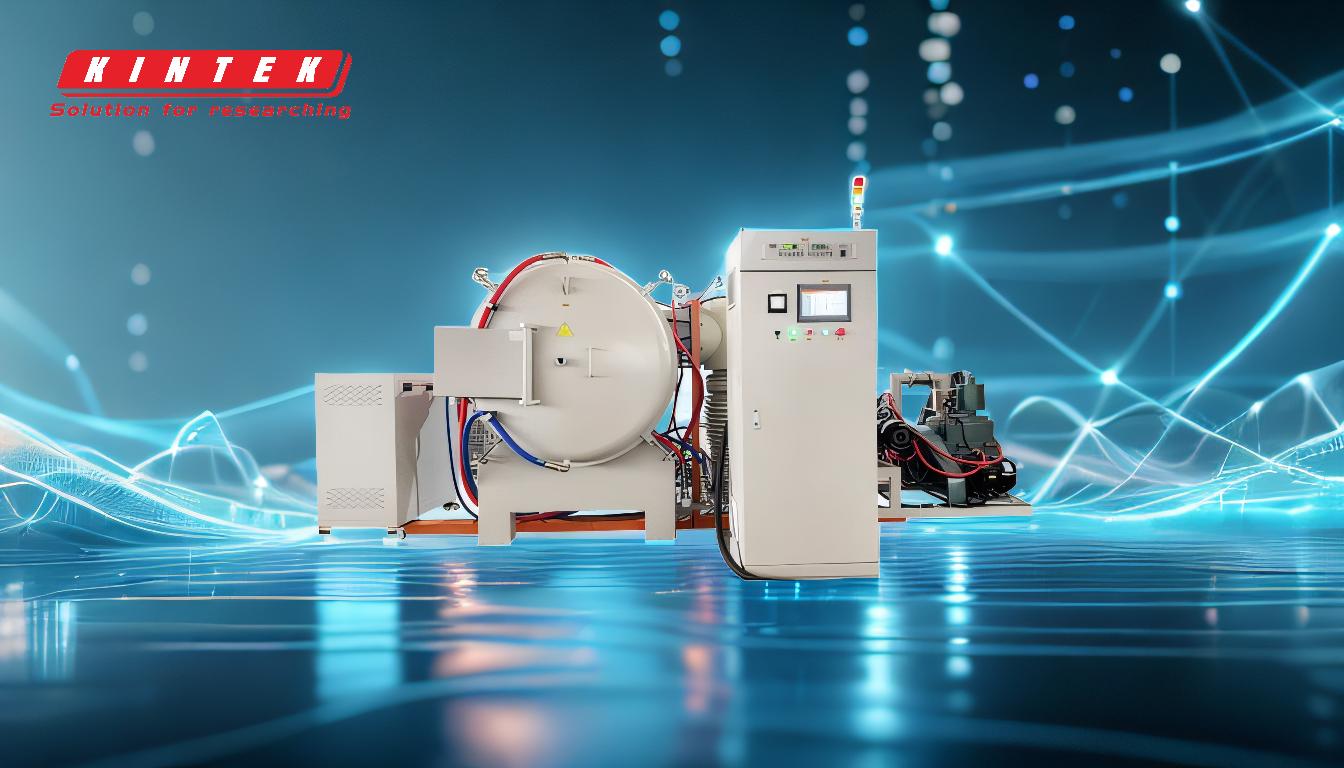
-
Definition and Purpose of a Ceramic Furnace:
- A ceramic furnace is a high-temperature heating device used for processes like firing, sintering, and melting ceramic materials.
- It ensures durability, hardness, and impermeability in ceramic products by providing controlled and uniform heating.
-
Core Components of a Ceramic Furnace:
- Heating Elements: Made of resistance wire or ceramic, these elements generate heat and ensure uniform temperature distribution.
- Furnace Chamber (Muffle): An insulated chamber where ceramic samples are placed for heating.
- Temperature Control Systems: Includes PID controllers, thermocouples, and sensors for precise temperature regulation (±1℃ accuracy).
- Insulation Materials: High-purity alumina fiber or polycrystalline mullite fiber insulation to maintain high temperatures and improve energy efficiency.
- Vacuum Systems: Built-in vacuum pumps to prevent opacity and ensure high-quality results in materials like porcelain.
-
Advanced Features:
- Programmable Controls: Multi-stage programmable temperature control for automated and precise heating cycles.
- Safety Mechanisms: Over-temperature protection, thermocouple failure alerts, and door-opening electrical outage systems.
- Ventilation and Cooling: Double-shell insulation and exhaust systems for quick cooling and efficient ventilation.
- Computer Interfaces: Integrated software for monitoring and controlling furnace operations.
-
Applications of Ceramic Furnaces:
- Ceramic Firing: Used to harden clay objects, making them durable and water-resistant.
- Sintering: Densifying ceramic powders to form solid materials.
- Melting and Testing: High-temperature processes for material analysis and quality testing.
- Industrial and Laboratory Use: Suitable for continuous operation in both industrial and research settings.
-
Types of Ceramic Furnaces:
- Muffle Furnaces: Designed with an insulated chamber for sample heating and precise temperature control.
- Porcelain Furnaces: Specialized for dental and industrial porcelain applications, featuring vacuum systems for clarity.
- Sintering Furnaces: Equipped with high-purity insulation and programmable controls for precise heating rates.
-
Material and Design Considerations:
- Refractory Materials: Used in construction to withstand extreme temperatures without breaking down.
- Stainless Steel and Ceramic Liners: Ensure color stability and long-term performance.
- Split Design: Detachable circuits for easy maintenance and repair.
-
Benefits of Modern Ceramic Furnaces:
- Precision: Advanced controllers and sensors ensure accurate temperature regulation.
- Efficiency: High-quality insulation and heating elements reduce energy consumption.
- Safety: Multiple protection measures prevent accidents and equipment damage.
- Versatility: Suitable for a wide range of ceramic materials and processes.
By understanding these key points, purchasers of ceramic furnaces can make informed decisions based on their specific needs, whether for industrial production, laboratory research, or specialized applications like dental porcelain fabrication.
Summary Table:
Aspect | Details |
---|---|
Definition | High-temperature device for firing, sintering, melting, and testing ceramics. |
Core Components | Heating elements, furnace chamber, temperature control, insulation, vacuum. |
Advanced Features | Programmable controls, safety mechanisms, ventilation, computer interfaces. |
Applications | Ceramic firing, sintering, melting, industrial and laboratory use. |
Types | Muffle, porcelain, and sintering furnaces. |
Benefits | Precision, efficiency, safety, and versatility. |
Ready to enhance your ceramic processes? Contact us today to find the perfect ceramic furnace for your needs!