Cold isostatic pressing (CIP) is a versatile powder-forming process used across various industries to produce high-performance parts with minimal distortion or cracking. It involves applying uniform pressure from all directions using a liquid medium, making it ideal for materials that require high integrity and complex shapes. Common applications include the consolidation of ceramic powders, compression of graphite, refractories, and electrical insulators. It is also widely used in dental and medical applications for fine ceramics, as well as in the production of wear and metal-forming tools, large parts, and materials like cemented carbides, tool steel, and artificial bones. Additionally, CIP is employed in food processing and resin powder forming.
Key Points Explained:
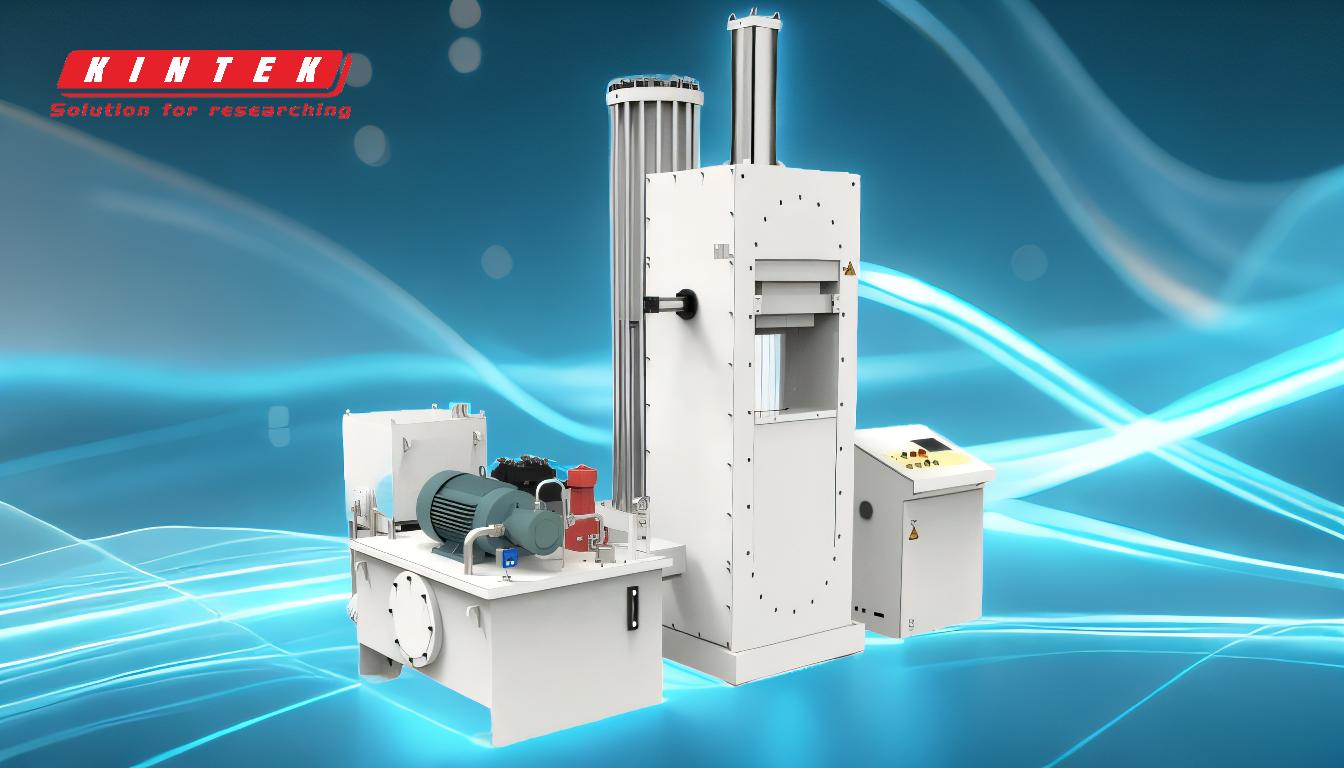
-
Consolidation of Ceramic Powders:
- CIP is extensively used to consolidate ceramic powders into dense, uniform shapes. This is particularly important in industries requiring high-performance ceramics, such as aerospace and electronics.
- Example: Fine ceramics used in dental crowns and medical implants are often produced using CIP to ensure high density and structural integrity.
-
Compression of Graphite:
- Graphite, known for its high thermal conductivity and resistance to extreme temperatures, is compressed using CIP to create isotropic graphite. This material is used in applications like semiconductor manufacturing and nuclear reactors.
- Example: Isotropic graphite components for crucibles and electrodes are produced through CIP.
-
Refractories and Electrical Insulators:
- Refractory materials, which withstand high temperatures, and electrical insulators, which require uniform density, are commonly formed using CIP.
- Example: Refractory bricks for furnaces and insulators for high-voltage electrical systems are manufactured using this process.
-
High-Melting-Point Metals and Cemented Carbides:
- CIP is ideal for forming high-melting-point metals and cemented carbides, which are challenging to shape using traditional methods.
- Example: Tungsten and molybdenum parts, as well as carbide cutting tools, are produced using CIP.
-
Tool Steel and Wear-Resistant Tools:
- Tool steel and wear-resistant tools benefit from CIP due to the process's ability to produce parts with minimal internal stress and high density.
- Example: Metal-forming dies and wear plates are often manufactured using CIP.
-
Sintered Filters and Artificial Bones:
- CIP is used to create porous sintered filters and biocompatible artificial bones, which require precise control over porosity and density.
- Example: Filters for industrial applications and bone implants for medical use are produced using CIP.
-
Resin Powder and Food Processing:
- CIP is also applied in non-metallic industries, such as resin powder forming and food processing, where uniform pressure is essential for consistent product quality.
- Example: Resin-based components and food-grade filters are manufactured using CIP.
-
Large Parts and Complex Shapes:
- CIP is particularly advantageous for producing large parts or complex shapes that cannot be easily formed using uniaxial pressing.
- Example: Large billets for aerospace components or intricate preforms for industrial machinery are made using CIP.
-
Hydrostatic Pressing and Minimal Distortion:
- The hydrostatic nature of CIP ensures uniform pressure distribution, reducing the risk of distortion or cracking during the forming process.
- Example: High-integrity billets for critical applications, such as turbine blades, are produced using CIP.
-
Applications in Dental and Medical Fields:
- CIP is widely used in the dental and medical industries to produce fine ceramics and biocompatible materials with precise geometries.
- Example: Dental implants and prosthetic components are often manufactured using CIP to ensure high precision and durability.
By leveraging the unique advantages of cold isostatic pressing, industries can produce high-quality, complex parts with minimal defects, making it a preferred method for a wide range of applications.
Summary Table:
Application | Description | Example |
---|---|---|
Consolidation of Ceramic Powders | Forms dense, uniform shapes for high-performance ceramics. | Dental crowns, medical implants. |
Compression of Graphite | Creates isotropic graphite for high-temperature applications. | Crucibles, electrodes. |
Refractories and Electrical Insulators | Produces materials resistant to high temperatures and uniform density. | Refractory bricks, high-voltage insulators. |
High-Melting-Point Metals | Ideal for shaping metals like tungsten and molybdenum. | Tungsten parts, carbide cutting tools. |
Tool Steel and Wear-Resistant Tools | Produces parts with minimal internal stress and high density. | Metal-forming dies, wear plates. |
Sintered Filters and Artificial Bones | Creates porous filters and biocompatible materials. | Industrial filters, bone implants. |
Resin Powder and Food Processing | Ensures uniform pressure for consistent product quality. | Resin components, food-grade filters. |
Large Parts and Complex Shapes | Suitable for large or intricate shapes difficult to form with uniaxial pressing. | Aerospace billets, industrial preforms. |
Hydrostatic Pressing | Ensures uniform pressure distribution, minimizing distortion. | Turbine blades, high-integrity billets. |
Dental and Medical Applications | Produces fine ceramics and biocompatible materials with precise geometries. | Dental implants, prosthetic components. |
Interested in leveraging CIP for your industry? Contact us today to learn more!