The flame synthesis method for carbon nanotubes (CNTs) is an innovative and efficient technique that leverages the combustion of hydrocarbon fuels to produce CNTs. Unlike traditional methods such as laser ablation, arc discharge, or chemical vapor deposition (CVD), flame synthesis offers a scalable and cost-effective approach, often utilizing simple equipment and readily available hydrocarbon sources. This method involves the controlled combustion of a fuel in the presence of a catalyst, resulting in the formation of CNTs within the flame environment. Flame synthesis is particularly attractive due to its potential for continuous production, lower energy requirements, and the ability to use waste or green feedstocks, aligning with sustainable manufacturing practices.
Key Points Explained:
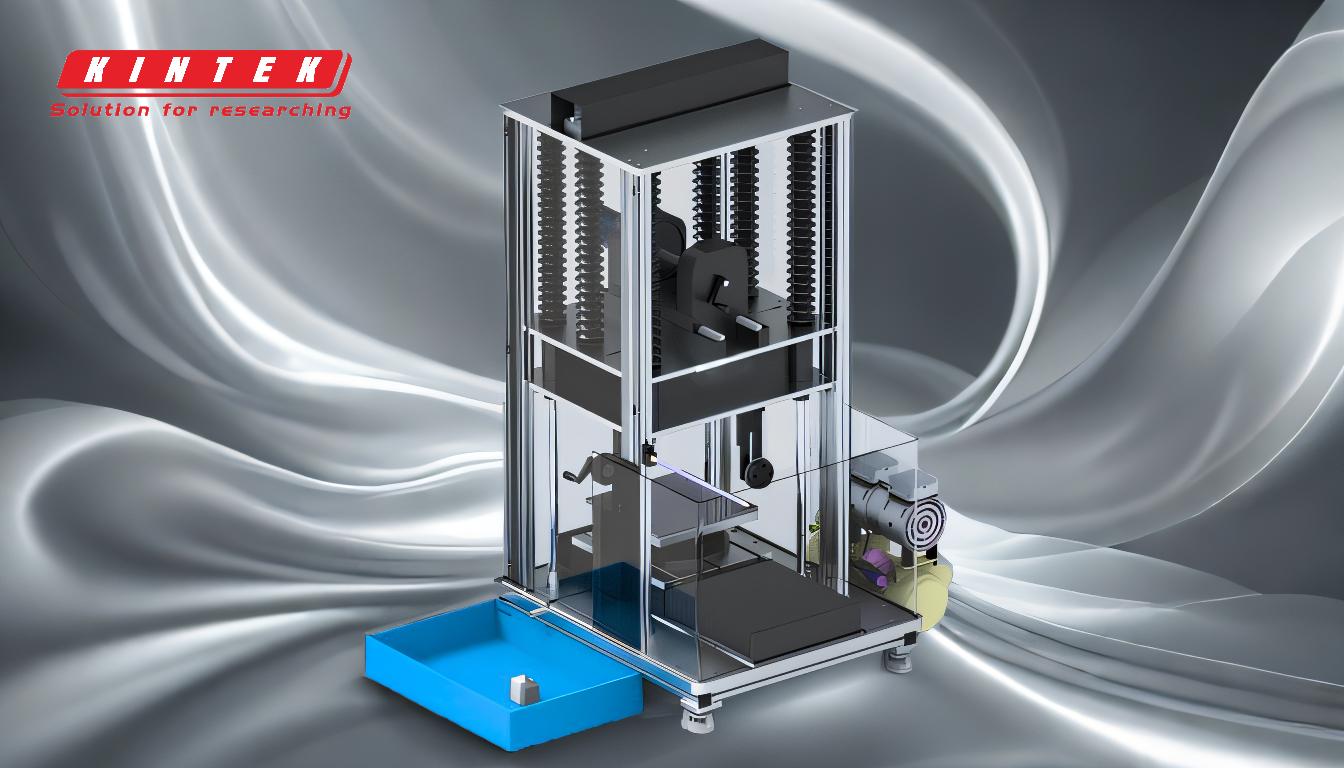
-
Principle of Flame Synthesis:
- Flame synthesis involves the combustion of hydrocarbon fuels (e.g., methane, ethylene, or acetylene) in a controlled environment. The combustion process generates high temperatures and reactive species, which facilitate the decomposition of hydrocarbons and the subsequent formation of carbon nanotubes.
- A catalyst, typically metal nanoparticles (e.g., iron, nickel, or cobalt), is introduced into the flame to promote the growth of CNTs. The catalyst acts as a nucleation site, enabling the carbon atoms to assemble into tubular structures.
-
Key Components of the Flame Synthesis Process:
- Fuel Source: Hydrocarbon fuels serve as the carbon source for CNT growth. The choice of fuel influences the quality and yield of the nanotubes.
- Oxidizer: Oxygen or air is used to sustain the combustion process. The oxidizer-to-fuel ratio is carefully controlled to maintain optimal flame conditions.
- Catalyst: Metal nanoparticles are essential for initiating and guiding the growth of CNTs. The catalyst is often introduced as a precursor or pre-deposited on a substrate.
- Flame Configuration: The flame can be configured in various ways, such as co-flow, counter-flow, or diffusion flames, depending on the desired CNT properties and production scale.
-
Advantages of Flame Synthesis:
- Scalability: Flame synthesis can be easily scaled up for continuous production, making it suitable for industrial applications.
- Cost-Effectiveness: The method utilizes relatively simple equipment and inexpensive hydrocarbon fuels, reducing production costs compared to traditional methods like CVD.
- Sustainability: Flame synthesis can incorporate waste or green feedstocks, such as carbon dioxide or methane, aligning with environmentally friendly manufacturing practices.
- High Yield: The high temperatures and reactive species in the flame environment enable efficient CNT growth, often resulting in high yields.
-
Challenges and Limitations:
- Control of Flame Parameters: Precise control of flame temperature, fuel-to-oxidizer ratio, and catalyst distribution is crucial for producing high-quality CNTs. Variations in these parameters can lead to defects or inconsistent nanotube properties.
- Catalyst Deactivation: Over time, the catalyst may become deactivated due to carbon deposition or sintering, reducing the efficiency of the synthesis process.
- Purification: The as-produced CNTs often require post-synthesis purification to remove catalyst particles and amorphous carbon impurities.
-
Applications and Future Prospects:
- Flame-synthesized CNTs have potential applications in electronics, energy storage, composites, and environmental technologies due to their unique mechanical, electrical, and thermal properties.
- Ongoing research focuses on optimizing flame synthesis parameters, exploring alternative catalysts, and integrating renewable feedstocks to enhance the sustainability and commercial viability of the method.
In summary, flame synthesis is a promising method for producing carbon nanotubes, offering a balance of scalability, cost-effectiveness, and environmental sustainability. While challenges remain in controlling flame parameters and ensuring consistent quality, advancements in catalyst design and process optimization are expected to further improve the method's efficiency and applicability.
Summary Table:
Aspect | Details |
---|---|
Principle | Combustion of hydrocarbon fuels in a controlled environment with a catalyst. |
Key Components | Fuel source, oxidizer, catalyst, flame configuration. |
Advantages | Scalability, cost-effectiveness, sustainability, high yield. |
Challenges | Control of flame parameters, catalyst deactivation, purification. |
Applications | Electronics, energy storage, composites, environmental tech. |
Interested in flame synthesis for carbon nanotubes? Contact us today to learn more!