Floating Catalyst Chemical Vapor Deposition (FCCVD) is a specialized variant of the Chemical Vapor Deposition (CVD) process, where a catalyst is introduced in a gaseous or vapor phase to facilitate the deposition of materials onto a substrate. Unlike traditional CVD methods that use solid catalysts, FCCVD employs a floating catalyst that remains suspended in the gas phase, allowing for more uniform and controlled deposition. This method is particularly useful for synthesizing advanced materials like carbon nanotubes, graphene, and other nanostructures. The process involves the decomposition of precursor gases in the presence of the floating catalyst, leading to the formation of a thin film or nanostructured material on the substrate. FCCVD offers advantages such as high purity, good control over material properties, and the ability to deposit materials at relatively low temperatures.
Key Points Explained:
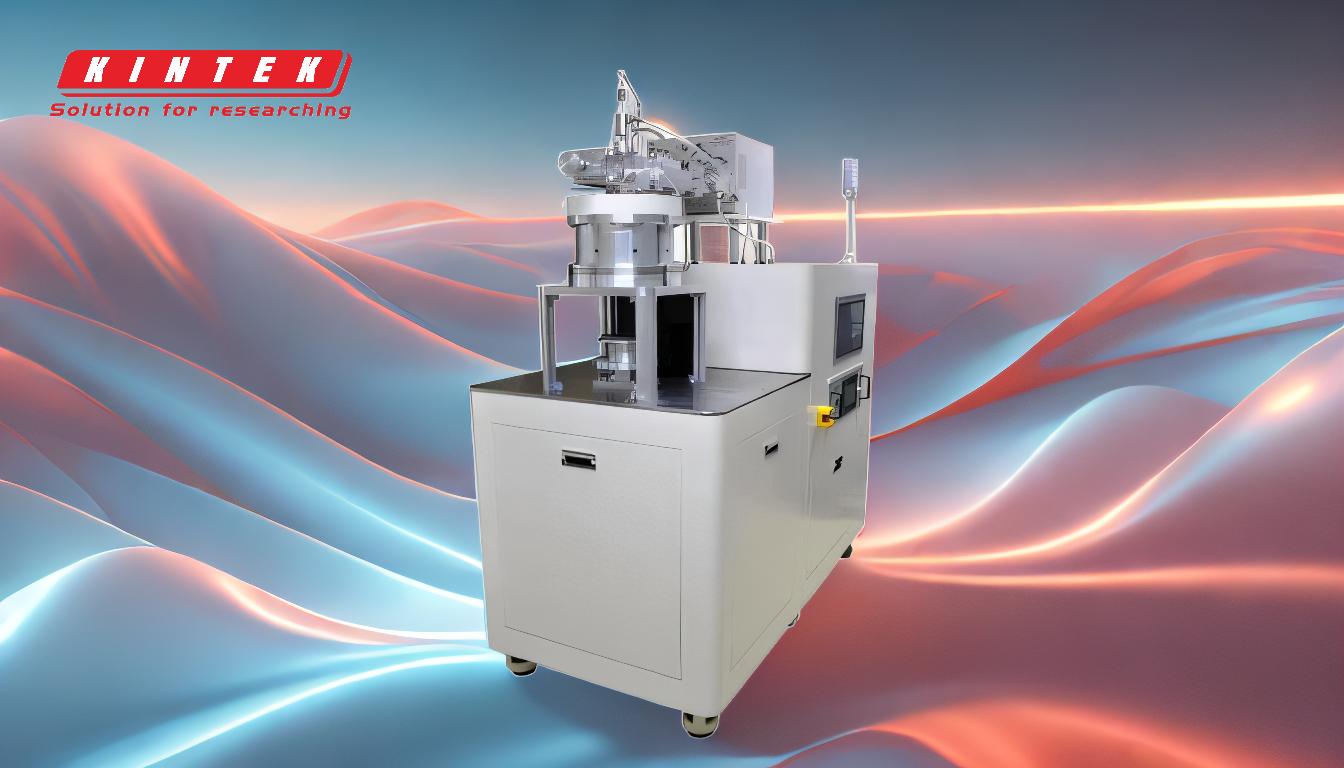
-
Definition of FCCVD:
- Floating Catalyst Chemical Vapor Deposition (FCCVD) is a process where a catalyst is introduced in a gaseous or vapor phase to facilitate the deposition of materials onto a substrate. This method is distinct from traditional CVD, which typically uses solid catalysts.
-
Mechanism of FCCVD:
- In FCCVD, precursor gases are introduced into a reaction chamber along with a floating catalyst. The catalyst remains suspended in the gas phase, allowing for more uniform and controlled deposition. The precursor gases decompose in the presence of the catalyst, leading to the formation of a thin film or nanostructured material on the substrate.
-
Advantages of FCCVD:
- High Purity: The use of a floating catalyst in the gas phase helps in achieving high-purity deposits.
- Controlled Deposition: The floating nature of the catalyst allows for better control over the deposition process, leading to uniform and high-quality films.
- Low Temperature Deposition: FCCVD can deposit materials at relatively low temperatures compared to other CVD methods, which is beneficial for temperature-sensitive substrates.
-
Applications of FCCVD:
- Carbon Nanotubes: FCCVD is widely used for the synthesis of carbon nanotubes due to its ability to provide a controlled environment for their growth.
- Graphene: The method is also employed in the production of graphene, where the floating catalyst helps in achieving high-quality, large-area graphene films.
- Other Nanostructures: FCCVD is used for the deposition of various other nanostructures, including nanowires and nanorods, which are essential for advanced electronic and optoelectronic applications.
-
Comparison with Other Deposition Methods:
- Traditional CVD: Unlike traditional CVD, which uses solid catalysts, FCCVD employs a floating catalyst, offering better control and uniformity.
- Sputtering: While sputtering involves the ejection of atoms from a solid target, FCCVD relies on the decomposition of precursor gases, making it more suitable for complex and nanostructured materials.
- Aerosol Deposition: Aerosol deposition involves the collision of fine ceramic particles with a substrate, whereas FCCVD uses a gaseous phase for deposition, allowing for finer control over the material properties.
-
Challenges and Considerations:
- Catalyst Selection: The choice of catalyst is crucial in FCCVD, as it directly affects the quality and properties of the deposited material.
- Process Parameters: Precise control over process parameters such as temperature, pressure, and gas flow rates is essential to achieve the desired material properties.
- Scalability: While FCCVD offers many advantages, scaling up the process for industrial applications can be challenging and requires further research and development.
In summary, Floating Catalyst Chemical Vapor Deposition (FCCVD) is a versatile and powerful method for depositing high-quality materials, particularly nanostructures, with precise control over their properties. Its unique use of a floating catalyst in the gas phase sets it apart from other deposition methods, offering significant advantages in terms of purity, uniformity, and low-temperature processing.
Summary Table:
Aspect | Details |
---|---|
Definition | A CVD method using a gaseous catalyst for uniform material deposition. |
Mechanism | Precursor gases decompose in the presence of a floating catalyst. |
Advantages | High purity, controlled deposition, low-temperature processing. |
Applications | Carbon nanotubes, graphene, nanowires, and other nanostructures. |
Comparison with CVD | Uses floating catalyst for better control and uniformity. |
Challenges | Catalyst selection, process parameter control, and scalability. |
Interested in leveraging FCCVD for your material synthesis needs? Contact our experts today to learn more!