An integral quench furnace is a specialized type of controlled atmosphere furnace used primarily in heat treatment processes, particularly for hardening metals. It integrates the heating and quenching processes into a single system, allowing for efficient and precise heat treatment. The furnace heats the material in a controlled atmosphere to avoid oxidation and other undesirable effects, then rapidly cools (quenches) it in a liquid medium like oil or water to achieve the desired hardness and mechanical properties. This type of furnace is widely used in industries requiring high-strength components, such as automotive, aerospace, and tool manufacturing.
Key Points Explained:
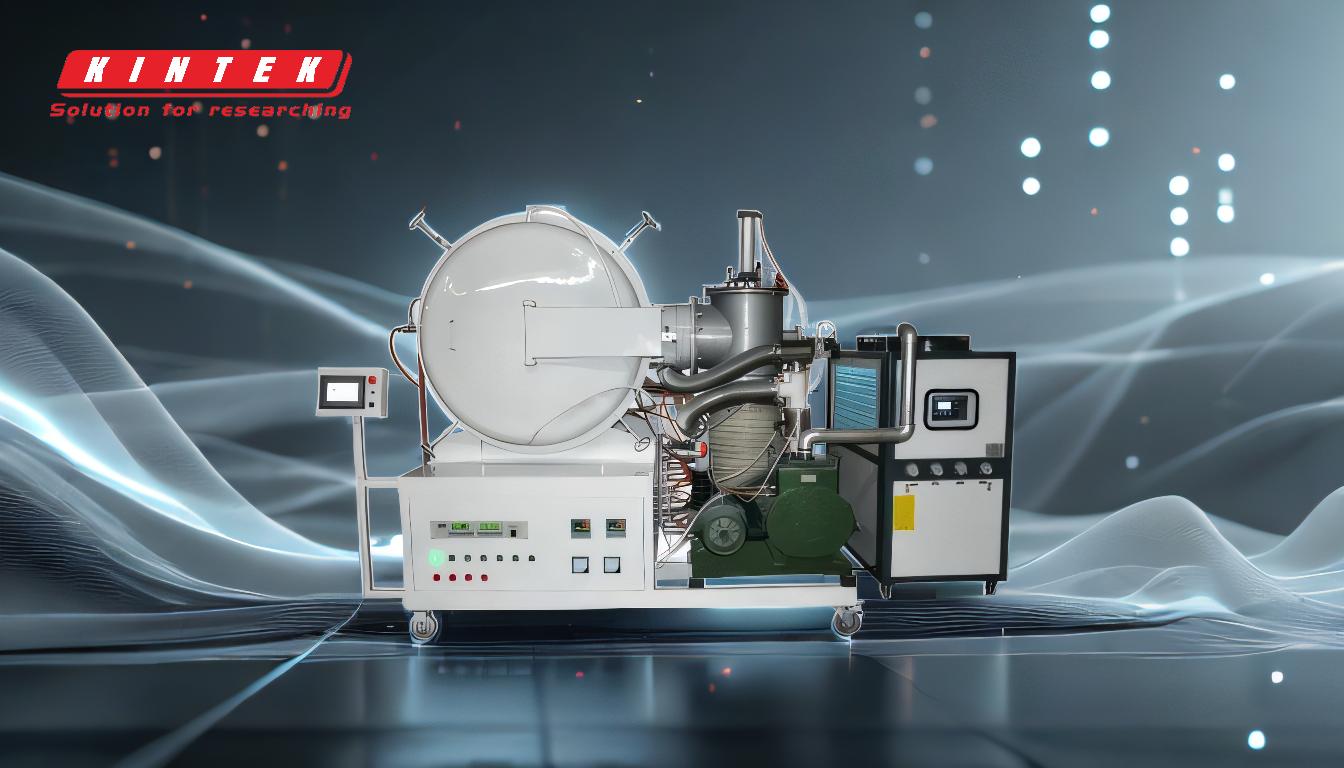
-
Definition and Purpose:
- An integral quench furnace is a type of furnace that combines heating and quenching processes in one system.
- Its primary purpose is to harden metals by heating them to a specific temperature in a controlled atmosphere and then rapidly cooling them to achieve the desired mechanical properties.
-
Controlled Atmosphere:
- The furnace operates in a controlled atmosphere, which means it introduces specific gases to protect the material from oxidation and other atmospheric effects during heating.
- This ensures the material retains its desired properties and surface quality.
-
Heating Process:
- The material is heated to a temperature above its critical point, where its microstructure changes to allow for hardening.
- The controlled atmosphere ensures uniform heating and prevents surface degradation.
-
Quenching Process:
- After heating, the material is rapidly cooled (quenched) in a liquid medium such as oil, water, or polymer.
- This rapid cooling locks in the desired microstructure, resulting in increased hardness and strength.
-
Applications:
- Integral quench furnaces are widely used in industries that require high-strength components, such as automotive (gears, shafts), aerospace (landing gear, engine components), and tool manufacturing (drills, dies).
-
Advantages:
- Efficiency: Combining heating and quenching in one system reduces processing time and energy consumption.
- Precision: The controlled atmosphere ensures consistent and high-quality results.
- Versatility: Can be used for a wide range of materials and applications.
-
Customization:
- Manufacturers like KinTek can design and build custom integral quench furnaces to meet specific application requirements, ensuring optimal performance and results.
By integrating heating and quenching processes in a controlled environment, integral quench furnaces provide a reliable and efficient solution for achieving the desired mechanical properties in metal components. Their use is critical in industries where strength, durability, and precision are paramount.
Summary Table:
Aspect | Details |
---|---|
Definition | Combines heating and quenching in one system for efficient heat treatment. |
Purpose | Hardens metals by heating in a controlled atmosphere and rapid cooling. |
Controlled Atmosphere | Protects materials from oxidation, ensuring surface quality. |
Heating Process | Heats material above critical point for uniform microstructure changes. |
Quenching Process | Rapid cooling in oil, water, or polymer to lock in hardness and strength. |
Applications | Automotive, aerospace, tool manufacturing (gears, shafts, drills, etc.). |
Advantages | Efficiency, precision, versatility, and customizable solutions. |
Ready to enhance your heat treatment process? Contact us today to explore custom integral quench furnace solutions!