Refractory materials are specialized, heat-resistant substances used in high-temperature applications such as furnaces, kilns, and reactors. They are composed of natural and synthetic materials, primarily nonmetallic, and often include combinations of compounds and minerals like alumina, fireclays, bauxite, chromite, dolomite, magnesite, silicon carbide, and zirconia. These materials are chosen for their ability to withstand extreme temperatures, thermal shock, and chemical corrosion. Refractory linings in equipment like furnaces often use multi-layer insulation designs, incorporating lightweight alumina ceramic fiber and high-quality insulation boards, which ensure low heat loss and energy efficiency. Advanced refractory materials, such as high-strength alumina or silicon carbide, are also used to provide accurate and uniform process conditions in industrial settings.
Key Points Explained:
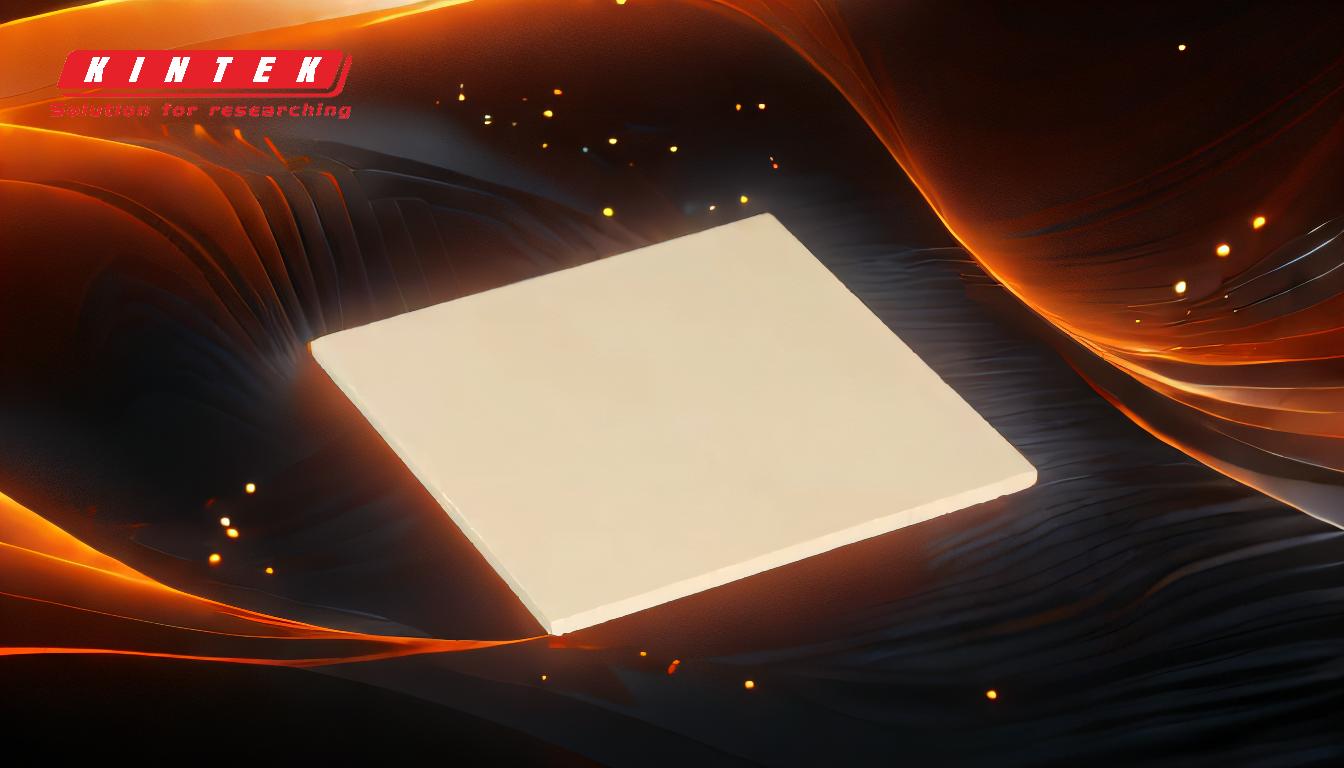
-
Composition of Refractory Materials:
- Refractory materials are made from a combination of natural and synthetic, nonmetallic compounds and minerals.
- Common materials include:
- Alumina (Al₂O₃): Provides high strength and thermal stability.
- Fireclays: Offer good thermal insulation and resistance to thermal shock.
- Bauxite: A source of alumina, used for its high melting point.
- Chromite (FeCr₂O₄): Adds corrosion resistance and high-temperature stability.
- Dolomite (CaMg(CO₃)₂): Used for its refractory properties in basic environments.
- Magnesite (MgCO₃): Provides resistance to basic slags and high temperatures.
- Silicon Carbide (SiC): Known for its exceptional thermal conductivity and resistance to wear.
- Zirconia (ZrO₂): Offers high thermal resistance and low thermal conductivity.
-
Types of Refractory Materials:
- Acidic Refractories: Made from materials like silica (SiO₂) and zirconia, suitable for acidic environments.
- Basic Refractories: Composed of magnesite, dolomite, and chromite, ideal for basic or alkaline conditions.
- Neutral Refractories: Include alumina and chromite, which are resistant to both acidic and basic slags.
-
Applications in Furnace Linings:
- Refractory materials are used in multi-layer insulation designs for furnace linings.
- Common designs incorporate:
- Lightweight Alumina Ceramic Fiber: Provides excellent thermal insulation and reduces heat loss.
- High-Quality Insulation Boards: Backing materials that enhance energy efficiency and structural integrity.
- These designs are asbestos-free, ensuring safety and compliance with modern environmental standards.
-
Advanced Refractory Materials:
- High-Strength Alumina (Al₂O₃): Used in muffle furnaces for its durability and ability to maintain uniform process conditions.
- Silicon Carbide (SiC): Employed in advanced furnace linings for its thermal conductivity and resistance to thermal shock.
- These materials ensure precise temperature control and longevity in high-temperature industrial processes.
-
Key Properties of Refractory Materials:
- High Melting Point: Essential for withstanding extreme temperatures.
- Thermal Shock Resistance: Ability to endure rapid temperature changes without cracking.
- Chemical Stability: Resistance to corrosion from slags, gases, and molten metals.
- Low Thermal Conductivity: Minimizes heat loss and improves energy efficiency.
- Mechanical Strength: Ensures structural integrity under high stress and load conditions.
-
Selection Criteria for Refractory Materials:
- Operating Temperature: Materials must withstand the maximum temperature of the application.
- Chemical Environment: Compatibility with the chemical composition of the process (acidic, basic, or neutral).
- Thermal Conductivity: Low conductivity is preferred for insulation, while high conductivity is needed for heat transfer applications.
- Mechanical Load: Materials must support the weight of the structure and any additional loads.
- Cost and Availability: Balancing performance with economic feasibility.
By understanding the composition, types, applications, and properties of refractory materials, equipment and consumable purchasers can make informed decisions to optimize performance, efficiency, and safety in high-temperature industrial processes.
Summary Table:
Aspect | Details |
---|---|
Composition | Alumina, fireclays, bauxite, chromite, dolomite, magnesite, SiC, zirconia |
Types | Acidic, basic, neutral refractories |
Applications | Furnace linings, multi-layer insulation, high-temperature industrial processes |
Key Properties | High melting point, thermal shock resistance, chemical stability, low thermal conductivity, mechanical strength |
Selection Criteria | Operating temperature, chemical environment, thermal conductivity, mechanical load, cost |
Optimize your high-temperature processes with the right refractory materials—contact our experts today!