Sintering and melting are two fundamental processes in additive manufacturing, each with distinct mechanisms and applications. Sintering involves compacting and bonding particles of a material using heat and/or pressure without reaching the material's melting point, whereas melting involves heating a material until it transitions from a solid to a liquid state. Sintering is particularly useful for materials with high melting points and is widely used in techniques like selective laser sintering (SLS) and electron beam sintering (EBS). Melting, on the other hand, is central to processes like Powder Bed Fusion (PBF), where metal particles are fully melted to create dense, functional parts. Both processes are critical in additive manufacturing, enabling the production of complex, high-performance components.
Key Points Explained:
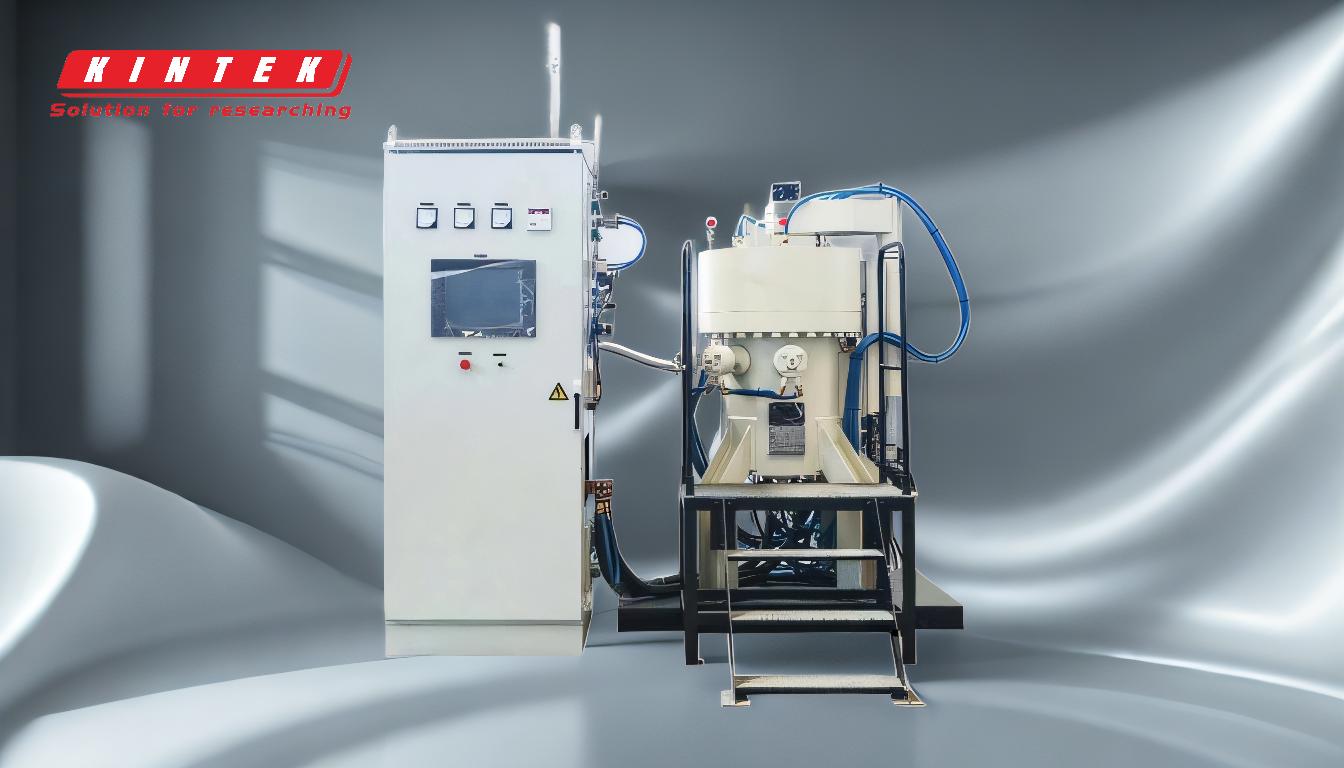
-
Definition of Sintering and Melting:
- Sintering: A process where particles are bonded together using heat and/or pressure without reaching the material's melting point. This allows for the creation of solid parts with enhanced properties like strength and hardness.
- Melting: Involves heating a material until it transitions from a solid to a liquid state. This requires sufficient thermal energy to change the material's energy state, enabling full liquefaction.
-
Key Differences:
- Liquefaction: Melting involves complete liquefaction of the material, while sintering occurs below the melting point, bonding particles without liquefaction.
- Temperature and Energy: Melting requires higher temperatures to achieve the energy threshold for liquefaction, whereas sintering operates at lower temperatures, often combined with pressure.
- Applications: Sintering is ideal for materials with high melting points and is used in composite materials like metal matrix composites (MMCs) and ceramic matrix composites (CMCs). Melting is central to processes like Powder Bed Fusion (PBF).
-
Role in Additive Manufacturing:
- Sintering: Used in techniques like selective laser sintering (SLS) and electron beam sintering (EBS), where powdered materials are selectively sintered layer by layer to create complex 3D objects. This process consolidates and bonds the material, resulting in fully dense and functional parts.
- Melting: Essential in Powder Bed Fusion (PBF), where metal particles and the substrate are fully melted to create dense, high-strength components.
-
Equipment and Processes:
- Sintering Furnace: A sintering furnace is used to apply heat and pressure to compact materials into solid parts. The process involves heating the material to just below its melting point, reducing porosity and bonding particles together.
- Hot Press Sintering Furnace: This specialized furnace uses high temperature and pressure in a vacuum environment to fuse ceramic powders into solid materials. It includes components like a furnace body, heater, pressure system, and vacuum system.
-
Advantages of Sintering:
- Material Properties: Enhances properties like strength, stiffness, and toughness by bonding reinforcement materials with the matrix material.
- Complex Geometries: Enables the production of complex, intricate shapes that are difficult to achieve with traditional manufacturing methods.
- High Melting Point Materials: Suitable for materials that are challenging to melt due to their high melting points.
-
Advantages of Melting:
- Full Density: Achieves fully dense parts with minimal porosity, ideal for high-performance applications.
- Material Versatility: Can be used with a wide range of metals and alloys, providing flexibility in material selection.
-
Applications:
- Sintering: Widely used in the production of composite materials, such as MMCs and CMCs, and in additive manufacturing techniques like SLS and EBS.
- Melting: Central to PBF processes, used in industries like aerospace, automotive, and medical devices for creating high-strength, complex components.
By understanding the distinctions and applications of sintering and melting, manufacturers can choose the appropriate process based on material properties, desired outcomes, and application requirements. Both processes play a crucial role in advancing additive manufacturing technologies, enabling the production of innovative, high-performance parts.
Summary Table:
Aspect | Sintering | Melting |
---|---|---|
Definition | Bonds particles using heat/pressure below melting point. | Heats material until it transitions to a liquid state. |
Temperature | Lower temperatures, often with pressure. | Higher temperatures to achieve liquefaction. |
Liquefaction | No liquefaction; particles bond without melting. | Complete liquefaction of material. |
Applications | Ideal for high-melting-point materials (e.g., MMCs, CMCs). | Central to Powder Bed Fusion (PBF) for dense, high-strength parts. |
Equipment | Sintering furnace or hot press sintering furnace. | Powder Bed Fusion systems. |
Advantages | Enhances strength, stiffness; enables complex geometries. | Achieves full density; versatile for various metals/alloys. |
Need help choosing the right process for your additive manufacturing needs? Contact our experts today!