Sintering in ceramics is a critical process that transforms powdered materials into a solid, cohesive structure through the application of heat, typically below the melting point of the primary material. This process involves several stages, including powder preparation, shaping, and controlled heating in a sintering furnace, which facilitates particle bonding and densification. The result is a durable, low-porosity ceramic product with improved mechanical and thermal properties. Understanding the sintering process is essential for optimizing ceramic production and achieving desired material characteristics.
Key Points Explained:
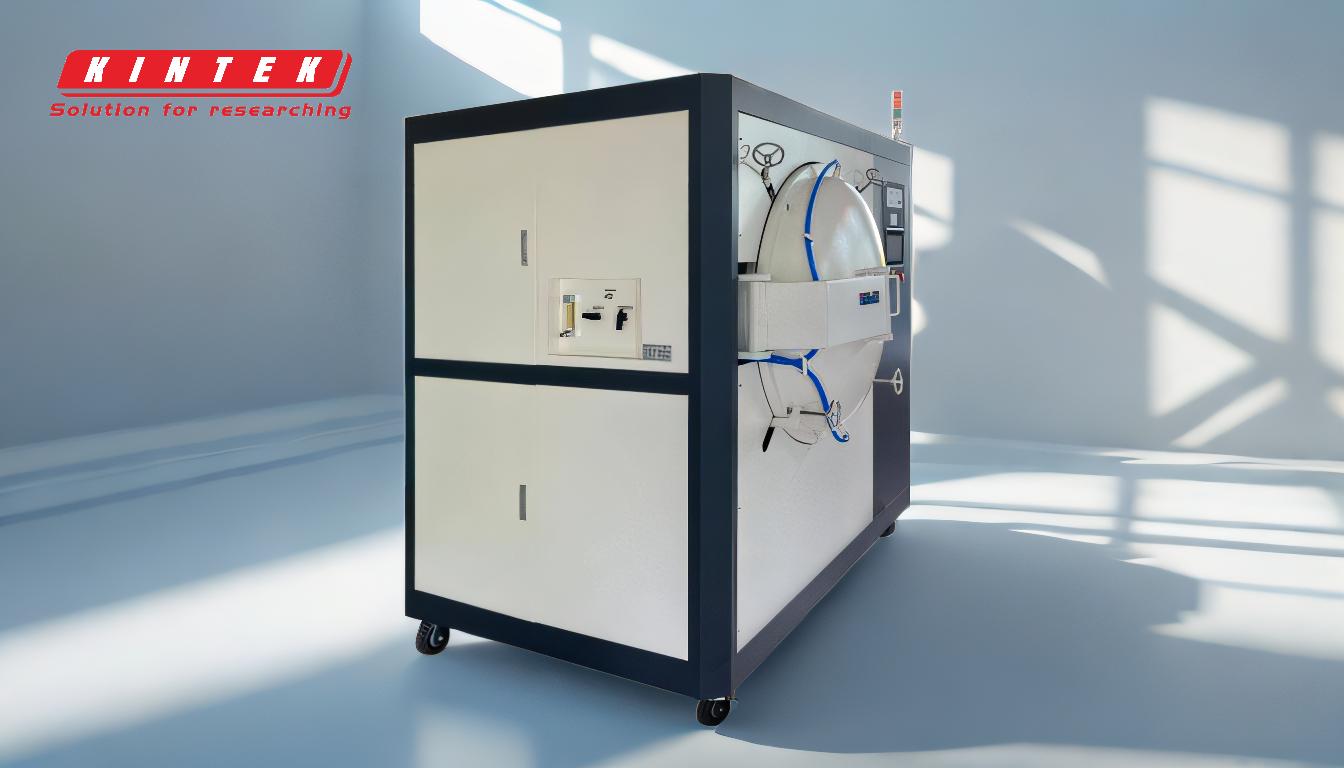
-
Definition and Purpose of Sintering in Ceramics:
- Sintering is a thermal treatment process used to bond ceramic particles into a solid structure without melting the primary material.
- The primary goal is to reduce porosity, increase density, and enhance the mechanical strength and thermal stability of the ceramic product.
-
Stages of the Sintering Process:
- Powder Preparation: Raw ceramic materials are ground into fine powders and mixed with additives like binders or coupling agents to improve handling and shaping.
- Shaping: The powder is compacted into a desired shape using techniques such as pressing or molding, forming a "green body."
- Binder Removal: The green body is heated at a low temperature to burn off or evaporate the binder, leaving behind a porous structure.
- High-Temperature Sintering: The material is heated in a sintering furnace to a temperature below its melting point, allowing particles to bond through diffusion and neck formation.
- Cooling: The sintered product is cooled gradually to solidify into a rigid, cohesive structure.
-
Role of the Sintering Furnace:
- A sintering furnace provides controlled heating and cooling environments essential for the sintering process.
- It ensures uniform temperature distribution, preventing defects like warping or cracking.
- Advanced furnaces allow precise control over heating rates, dwell times, and cooling rates, which are critical for achieving optimal material properties.
-
Mechanisms of Sintering:
- Diffusion: Atoms move across particle surfaces, leading to neck formation and particle bonding.
- Grain Growth: Particles coalesce, reducing porosity and increasing density.
- Liquid Phase Sintering: In some cases, a small amount of liquid phase forms, aiding particle rearrangement and bonding.
-
Factors Influencing Sintering:
- Temperature: Higher temperatures accelerate diffusion and bonding but must be controlled to avoid melting.
- Time: Longer sintering times allow for more complete densification but may lead to excessive grain growth.
- Atmosphere: The sintering environment (e.g., air, vacuum, or inert gas) can affect oxidation, reduction, or contamination.
- Particle Size and Shape: Smaller, uniform particles sinter more efficiently due to increased surface area and contact points.
-
Applications of Sintered Ceramics:
- Sintered ceramics are used in industries such as electronics (insulators, substrates), aerospace (thermal barriers), automotive (brake discs), and medical (implants, prosthetics).
- The process enables the production of complex shapes with high precision and consistency.
-
Advantages of Sintering:
- Produces materials with high strength, wear resistance, and thermal stability.
- Allows for the creation of intricate geometries and near-net-shape components.
- Reduces material waste compared to traditional machining processes.
-
Challenges and Considerations:
- Controlling shrinkage and dimensional changes during sintering.
- Avoiding defects such as cracks, voids, or warping.
- Balancing sintering parameters to achieve desired properties without excessive energy consumption.
By understanding the sintering process and its key stages, manufacturers can optimize ceramic production, ensuring high-quality, durable products tailored to specific applications. The sintering furnace plays a pivotal role in this process, providing the controlled environment necessary for successful sintering.
Summary Table:
Key Aspect | Details |
---|---|
Purpose | Bonds ceramic particles, reduces porosity, and enhances strength. |
Stages | Powder preparation, shaping, binder removal, high-temperature sintering, cooling. |
Role of Sintering Furnace | Provides controlled heating/cooling for uniform temperature distribution. |
Mechanisms | Diffusion, grain growth, and liquid phase sintering. |
Applications | Electronics, aerospace, automotive, and medical industries. |
Advantages | High strength, wear resistance, and thermal stability. |
Optimize your ceramic production with expert guidance—contact us today!