Atmospheric pressure sintering is a method of sintering materials, such as silicon carbide, at high temperatures (2000–2150°C) under normal atmospheric pressure (1.01×10⁵ Pa) in an inert environment without applying external pressure. Developed in 1974 by S. Prochazka and others at GE Company, this technique can be categorized into solid-phase and liquid-phase sintering. Solid-phase sintering yields high-density materials with excellent high-temperature mechanical properties, while liquid-phase sintering reduces sintering temperatures and enhances material properties by introducing a liquid phase that accelerates sintering and modifies fracture modes. This method is cost-effective, allows for versatile product shapes and sizes, and produces materials with uniform microstructures, making it ideal for precision structural components like seals, bearings, and semiconductor clamps.
Key Points Explained:
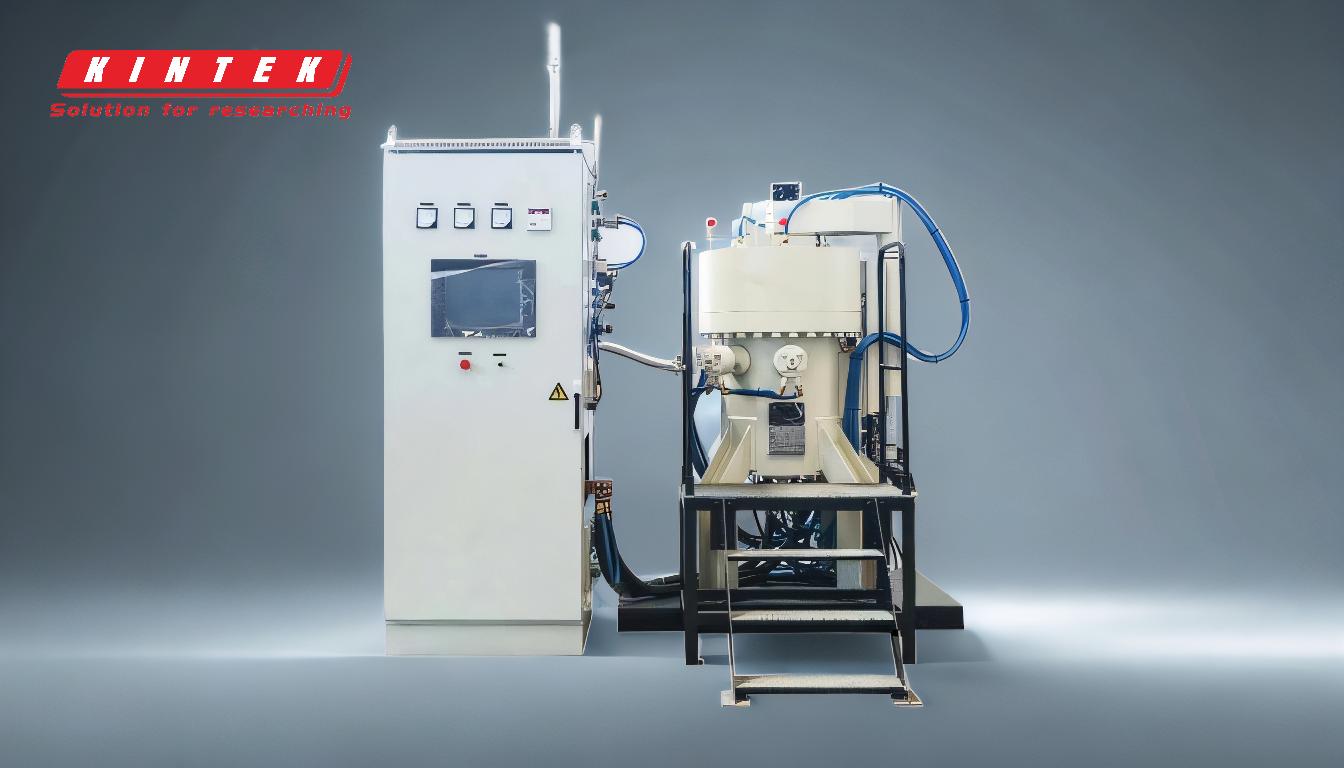
-
Definition and Development:
- Atmospheric pressure sintering is a process that involves sintering materials, such as silicon carbide, at high temperatures (2000–2150°C) under normal atmospheric pressure (1.01×10⁵ Pa) in an inert atmosphere.
- It was developed in 1974 by S. Prochazka and others at GE Company, marking a significant advancement in sintering technology.
-
Types of Atmospheric Pressure Sintering:
- Solid-Phase Sintering: Achieves high-density materials with excellent high-temperature mechanical properties. This method relies on atomic diffusion to bond particles without the presence of a liquid phase.
- Liquid-Phase Sintering: Introduces a liquid phase that lowers the sintering temperature, accelerates the sintering process, and modifies the material's fracture modes, resulting in improved overall properties.
-
Process Conditions:
- Conducted under normal atmospheric pressure (1.01×10⁵ Pa), eliminating the need for external pressure.
- Requires an inert atmosphere to prevent oxidation or contamination during sintering.
- Operates at high temperatures (2000–2150°C), which are typically lower than the melting point of the material being sintered.
-
Advantages:
- Cost-Effectiveness: Lower production costs compared to pressure-assisted sintering methods.
- Versatility: No limitations on the shape and size of the product, making it suitable for a wide range of applications.
- High Densification: Produces materials with high density and uniform microstructures.
- Material Performance: Results in excellent mechanical and thermal properties, ideal for precision structural components.
-
Applications:
- Precision structural components such as seals in mechanical pumps, plain bearings, bulletproof armor, optical mirrors, and semiconductor wafer clamps.
- Suitable for industries requiring high-performance materials with consistent quality and reliability.
-
Comparison with Other Sintering Methods:
- Unlike pressure-assisted sintering methods (e.g., hot isostatic pressing or spark plasma sintering), atmospheric pressure sintering does not require external pressure, simplifying the process and reducing equipment costs.
- Compared to conventional sintering, it offers better control over microstructure and material properties, especially in liquid-phase sintering.
-
Material Properties:
- Solid-phase sintering results in materials with high density and excellent high-temperature mechanical properties, making them suitable for demanding applications.
- Liquid-phase sintering enhances material properties by introducing a liquid phase, which improves sintering speed and modifies fracture behavior, leading to better overall performance.
-
Industrial Relevance:
- Atmospheric pressure sintering is widely used in industries requiring high-performance ceramics and composites, such as aerospace, automotive, and electronics.
- Its ability to produce materials with uniform microstructures and excellent mechanical properties makes it a preferred method for manufacturing precision components.
By understanding these key points, purchasers of equipment and consumables can make informed decisions about the suitability of atmospheric pressure sintering for their specific needs, ensuring optimal performance and cost-effectiveness in their applications.
Summary Table:
Aspect | Details |
---|---|
Definition | Sintering at 2000–2150°C under normal atmospheric pressure in an inert environment. |
Types | Solid-phase (high density) and liquid-phase (lower temperature, enhanced properties). |
Process Conditions | 1.01×10⁵ Pa, inert atmosphere, 2000–2150°C. |
Advantages | Cost-effective, versatile shapes, high densification, excellent performance. |
Applications | Seals, bearings, bulletproof armor, optical mirrors, semiconductor clamps. |
Industrial Relevance | Aerospace, automotive, electronics, and precision components. |
Discover how atmospheric pressure sintering can optimize your material processing—contact our experts today!