The basic lining of an induction furnace is a critical component designed to contain molten metal, isolate it from the furnace's outer structure (such as the coil), and protect the furnace body during operation. It is typically made of refractory materials and is layered with other components like insulating mica, an alarm network, and asbestos insulation boards to ensure insulation, heat resistance, and safety. The lining's primary function is to withstand high temperatures and chemical reactions with molten metals while maintaining structural integrity. Proper selection and maintenance of the lining are essential for the efficient and safe operation of the induction furnace.
Key Points Explained:
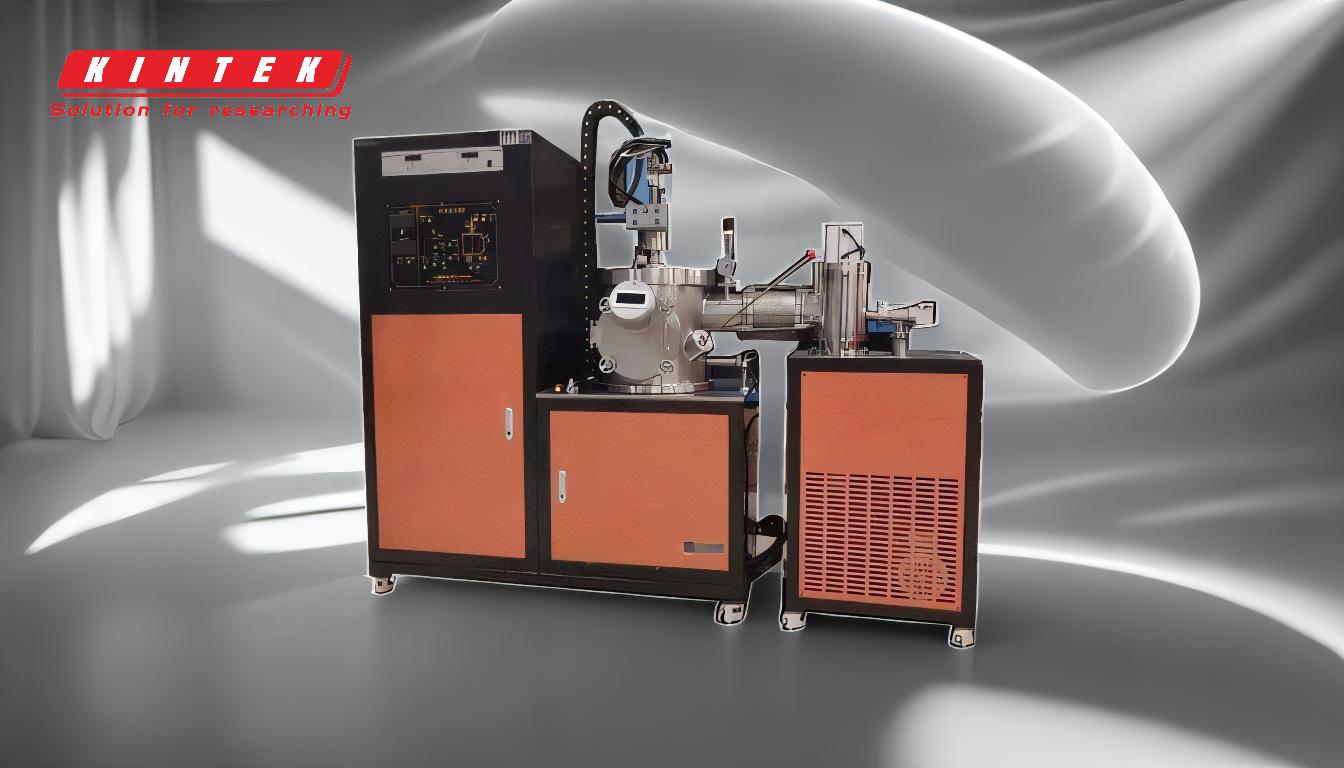
-
Purpose of the Induction Furnace Lining:
- The lining serves as a barrier to contain molten metal, preventing it from coming into contact with the furnace's outer structure, such as the induction coil.
- It protects the furnace body from thermal and chemical damage during operation.
- The lining is crucial for maintaining the furnace's structural integrity and ensuring safe and efficient melting processes.
-
Composition of the Lining:
- The lining is primarily made of refractory materials, which are chosen for their ability to withstand extreme temperatures and resist chemical reactions with molten metals.
- It is layered with other components:
- Insulating mica: Provides electrical insulation.
- Alarm network: Acts as a safety feature to warn of potential issues.
- Asbestos insulation board: Offers heat insulation to protect the outer structure of the furnace.
-
Layered Structure of the Furnace Body:
- From the outside to the inside, the furnace body typically consists of:
- Insulating mica: Ensures electrical insulation.
- Alarm network: Detects and alerts operators to potential problems.
- Asbestos insulation board: Provides thermal insulation.
- Refractory lining: The innermost layer that directly contacts the molten metal.
- From the outside to the inside, the furnace body typically consists of:
-
Role of the Crucible:
- The crucible, made of refractory materials, is a key part of the lining and holds the metal charge.
- It acts as the secondary winding of a transformer in the induction furnace setup, facilitating the melting process through electromagnetic induction.
-
Importance of Proper Lining Maintenance:
- The lining is subject to wear and tear due to high temperatures and chemical interactions with molten metals.
- Regular inspection and maintenance are necessary to prevent cracks, erosion, or failure, which could lead to safety hazards or operational inefficiencies.
-
Selection of Refractory Materials:
- The choice of refractory materials depends on the type of metal being melted, operating temperatures, and the specific requirements of the furnace.
- Common materials include alumina, silica, and magnesia-based refractories, each offering different properties such as thermal stability, resistance to thermal shock, and chemical inertness.
-
Integration with Other Furnace Components:
- The lining works in conjunction with other furnace components, such as the power supply, induction coil, and cooling systems, to ensure efficient melting and safe operation.
- Proper alignment and installation of the lining are essential to avoid gaps or weak points that could compromise performance.
-
Safety Considerations:
- The lining must be designed to handle thermal expansion and contraction without cracking.
- The alarm network integrated into the lining provides an additional layer of safety by detecting issues such as overheating or lining failure.
By understanding the composition, structure, and function of the induction furnace lining, operators can make informed decisions about material selection, maintenance, and safety protocols to optimize furnace performance and longevity.
Summary Table:
Key Aspect | Details |
---|---|
Purpose | Contains molten metal, protects furnace structure, ensures safety. |
Composition | Refractory materials, insulating mica, alarm network, asbestos insulation. |
Layered Structure | Insulating mica → Alarm network → Asbestos insulation → Refractory lining. |
Crucible Role | Holds metal charge, acts as a secondary winding in the induction process. |
Maintenance Importance | Prevents cracks, erosion, and failure; ensures safe and efficient operation. |
Refractory Material Choice | Alumina, silica, magnesia-based materials for thermal and chemical resistance. |
Safety Features | Alarm network detects overheating or lining failure. |
Optimize your induction furnace performance with the right lining—contact our experts today!