Brazing is a metal-joining process that involves melting a filler metal into a joint to bond two or more metal pieces together. The process is widely used in various industries due to its ability to create strong, leak-proof, and durable joints. The basic steps of brazing include preparation of the metal surfaces, assembly and filling with the filler metal, and post-brazing inspection. The preparation phase is crucial as it ensures that the surfaces are clean and free from contaminants, which is essential for achieving a strong bond. The filler metal, which has a lower melting point than the base metals, is then applied and heated until it melts and flows into the joint by capillary action. After cooling, the joint is inspected to ensure it meets the required standards.
Key Points Explained:
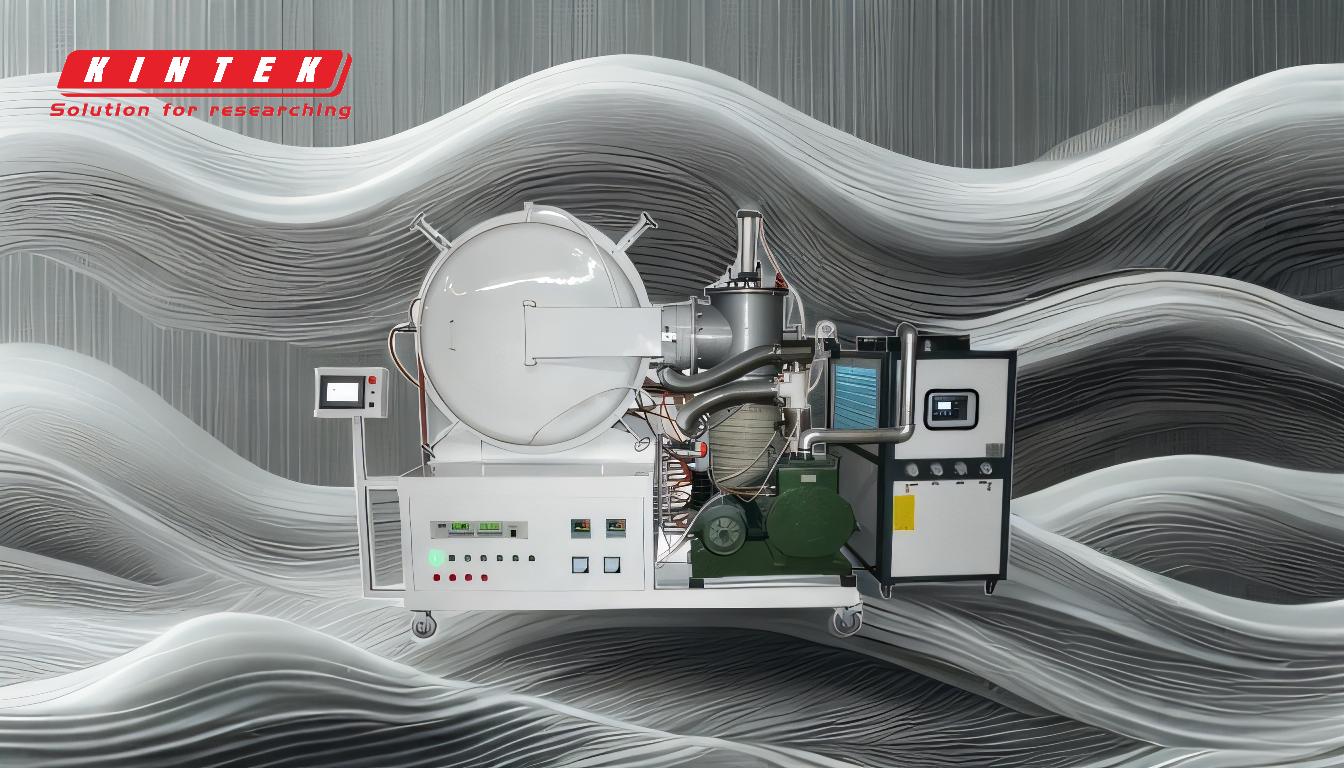
-
Preparation Before Brazing:
- Surface Cleaning: The surfaces to be joined must be thoroughly cleaned to remove any oxides, oils, or other contaminants. This can be done using mechanical methods like grinding or chemical methods like acid cleaning.
- Flux Application: A flux is often applied to the surfaces to prevent oxidation during the heating process. The flux also helps the filler metal flow more easily into the joint.
-
Assembling and Filling with Filler Metal:
- Assembly: The metal pieces are assembled in the desired configuration, ensuring that the joint is properly aligned and that there is adequate space for the filler metal to flow.
- Filler Metal Application: The filler metal, which is chosen based on its compatibility with the base metals and the required joint properties, is placed in or near the joint.
- Heating: The assembly is heated to a temperature above the melting point of the filler metal but below the melting point of the base metals. This can be done using various heat sources, such as a torch, furnace, or induction heating.
-
Inspection of the Brazed Joint:
- Visual Inspection: The joint is visually inspected for any defects such as cracks, voids, or incomplete filling.
- Non-Destructive Testing: Techniques like X-ray or ultrasonic testing may be used to detect internal defects that are not visible to the naked eye.
- Mechanical Testing: The joint may be subjected to mechanical tests like tensile or shear tests to ensure it meets the required strength standards.
-
Post-Brazing Treatments:
- Cleaning: Any residual flux or oxide layer is removed from the joint, often using chemical cleaning methods.
- Heat Treatment: In some cases, the brazed assembly may undergo additional heat treatment to improve the mechanical properties of the joint or the base metals.
-
Advantages of Brazing:
- Strong Joints: Brazing produces joints that are strong and durable, often stronger than the base metals themselves.
- Versatility: Brazing can join a wide range of metals, including dissimilar metals, which are difficult to weld.
- Leak-Proof Joints: The capillary action ensures that the joint is completely filled, making it leak-proof, which is essential for applications like plumbing or refrigeration.
-
Applications of Brazing:
- Automotive Industry: Brazing is used to join components in engines, transmissions, and exhaust systems.
- Aerospace Industry: The process is used to join complex assemblies in aircraft engines and structures.
- Electronics: Brazing is used to join components in electronic devices, where precision and reliability are critical.
By following these steps and understanding the principles behind brazing, one can achieve high-quality, reliable joints suitable for a wide range of applications.
Summary Table:
Step | Key Actions |
---|---|
Preparation | Clean surfaces, apply flux to prevent oxidation. |
Assembling & Filling | Align metal pieces, apply filler metal, and heat to melt it into the joint. |
Inspection | Visually inspect, use non-destructive testing, and conduct mechanical tests. |
Post-Brazing Treatments | Clean residual flux, apply heat treatment if needed. |
Advantages | Strong joints, versatility, and leak-proof connections. |
Applications | Automotive, aerospace, and electronics industries. |
Discover how brazing can enhance your metal-joining processes—contact our experts today for more insights!