Chemical deposition is a technique used to create thin films or coatings on substrates through chemical reactions. It involves the use of fluid precursors that undergo chemical changes at the surface of a substrate, resulting in the deposition of a solid layer. This method is widely used in industries such as electronics, solar energy, and cutting tools due to its ability to produce conformal coatings that evenly cover all surfaces. Common types of chemical deposition include Chemical Vapor Deposition (CVD), Chemical Solution Deposition (CSD), and plating. Each method has unique processes and applications, making chemical deposition a versatile and essential technique in material science and engineering.
Key Points Explained:
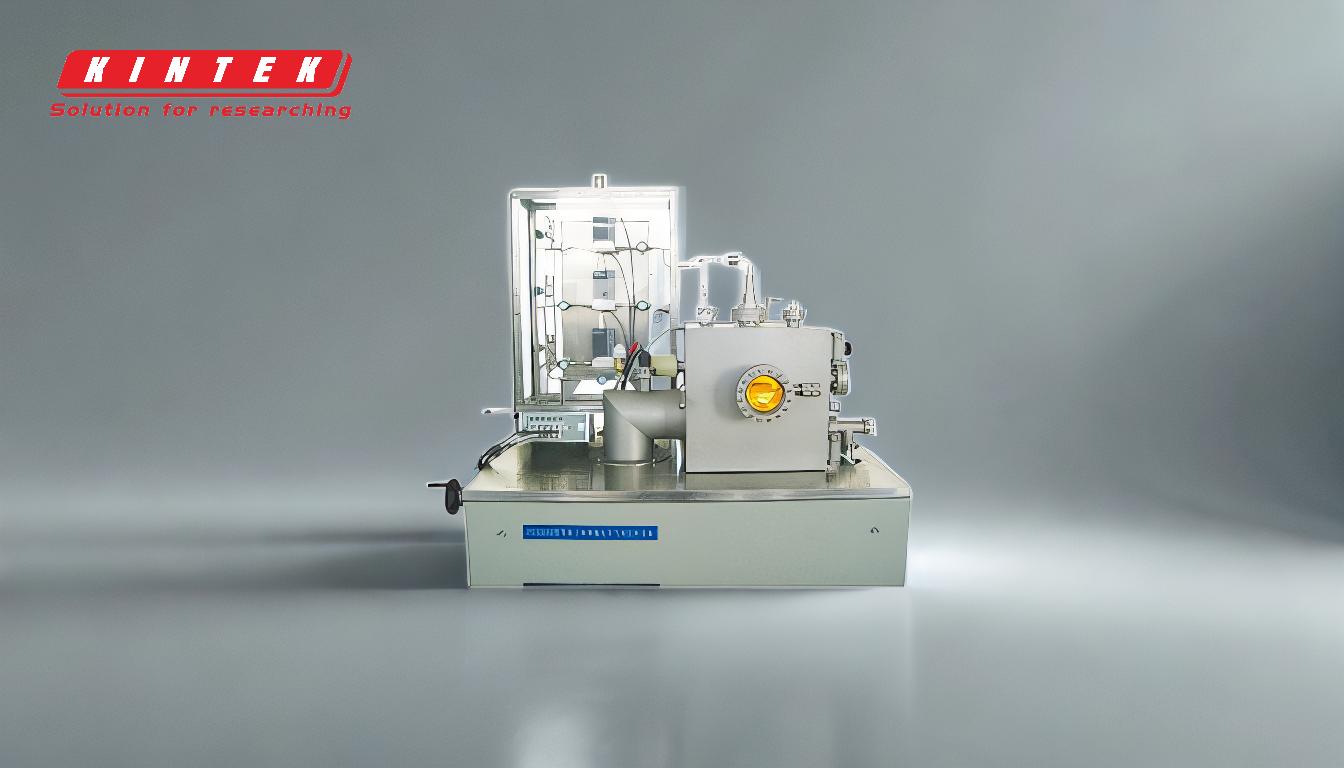
-
Definition of Chemical Deposition:
- Chemical deposition is a process where a fluid precursor undergoes a chemical reaction at the surface of a substrate, resulting in the formation of a solid layer.
- This technique is used to create thin films or coatings that are conformal, meaning they evenly cover all surfaces of the substrate.
-
Types of Chemical Deposition:
-
Chemical Vapor Deposition (CVD):
- CVD involves the use of gaseous precursors that react or decompose on the substrate surface to form a solid film.
- It is widely used in the electronics industry for depositing thin films on semiconductors, in cutting tools to prevent corrosion and wear, and in the manufacture of thin-film solar cells.
-
Chemical Solution Deposition (CSD):
- CSD involves the use of liquid precursors, such as solutions or gels, which are applied to the substrate and then undergo a chemical reaction to form a solid film.
- Common CSD methods include the sol-gel technique and chemical bath deposition.
-
Plating:
- Plating involves the deposition of a metal layer onto a substrate using either electrochemical (electroplating) or chemical (electroless deposition) processes.
- Electroplating uses an electric current to reduce metal ions in a solution onto the substrate, while electroless deposition relies on chemical reactions to deposit the metal without an external power source.
-
Chemical Vapor Deposition (CVD):
-
Common Chemical Deposition Methods:
-
Sol-Gel Technique:
- This method involves the formation of a gel from a solution, which is then dried to create a thin film.
- The sol-gel process is used to produce coatings with high purity and homogeneity.
-
Spray Pyrolysis:
- Spray pyrolysis involves the high-pressure spraying of a solution onto a heated substrate, where the solvent evaporates and the solute undergoes a chemical reaction to form a thin film.
- This method is often used for depositing metal oxide films.
-
Chemical Bath Deposition:
- In this method, the substrate is submerged in a chemical solution, and a thin film is deposited through a chemical reaction at the substrate surface.
- This technique is commonly used for depositing semiconductor films.
-
Chemical Vapor Evaporation:
- This method uses thermally induced chemical reactions to deposit a thin film on the substrate.
- It is similar to CVD but typically involves lower temperatures and simpler equipment.
-
Sol-Gel Technique:
-
Applications of Chemical Deposition:
-
Electronics:
- Chemical deposition is used to deposit thin films on semiconductors, which are essential for the fabrication of electronic devices such as transistors and integrated circuits.
-
Cutting Tools:
- Thin films deposited by chemical deposition techniques are used to enhance the durability and performance of cutting tools by preventing corrosion and wear.
-
Solar Cells:
- Chemical deposition is used in the manufacture of thin-film solar cells, where one or more layers of photovoltaic materials are deposited on a substrate to convert sunlight into electricity.
-
Electronics:
-
Advantages of Chemical Deposition:
-
Conformal Coatings:
- Chemical deposition techniques produce coatings that evenly cover all surfaces of the substrate, including complex geometries.
-
High Purity and Homogeneity:
- The chemical reactions involved in deposition processes often result in films with high purity and uniform composition.
-
Versatility:
- Chemical deposition can be used to deposit a wide range of materials, including metals, semiconductors, and ceramics, making it a versatile technique for various applications.
-
Conformal Coatings:
-
Considerations for Equipment and Consumable Purchasers:
-
Precursor Selection:
- The choice of precursor is critical for achieving the desired film properties. Purchasers should consider the purity, reactivity, and compatibility of precursors with the substrate and deposition method.
-
Equipment Compatibility:
- Different chemical deposition methods require specific equipment, such as CVD reactors, spray pyrolysis systems, or plating baths. Purchasers should ensure that the equipment is compatible with the desired deposition process and substrate materials.
-
Process Control:
- Precise control of process parameters, such as temperature, pressure, and precursor flow rate, is essential for achieving consistent film quality. Purchasers should consider equipment with advanced control systems to optimize the deposition process.
-
Safety and Environmental Impact:
- Chemical deposition processes may involve hazardous chemicals and byproducts. Purchasers should consider the safety features of the equipment and the environmental impact of the deposition process, including waste management and emissions control.
-
Precursor Selection:
In summary, chemical deposition is a versatile and essential technique for creating thin films and coatings with a wide range of applications in electronics, cutting tools, and solar energy. Understanding the different types of chemical deposition methods, their processes, and their advantages can help equipment and consumable purchasers make informed decisions when selecting materials and equipment for their specific needs.
Summary Table:
Aspect | Details |
---|---|
Definition | Process where fluid precursors form solid layers on substrates via chemical reactions. |
Types | CVD, CSD, Plating (electroplating and electroless deposition). |
Common Methods | Sol-Gel, Spray Pyrolysis, Chemical Bath Deposition, Chemical Vapor Evaporation. |
Applications | Electronics (semiconductors), Cutting Tools (corrosion resistance), Solar Cells. |
Advantages | Conformal coatings, high purity, versatility in material deposition. |
Key Considerations | Precursor selection, equipment compatibility, process control, safety. |
Ready to enhance your materials with chemical deposition? Contact our experts today to find the right solution for your needs!