The choice of frequency for induction heating is a critical decision that depends on several factors, including the material properties, desired heating depth, efficiency, and application requirements. High-frequency induction heating (100–500 kHz) is typically used for smaller, thinner materials requiring shallow heating depths, while lower frequencies are better suited for larger, thicker materials needing deeper heat penetration. The selection also considers factors such as melting material, stirring effect, noise, efficiency, and cost. By adjusting the coil design and compensating capacitors, the frequency can be tailored to meet specific process needs, ensuring optimal performance and energy efficiency.
Key Points Explained:
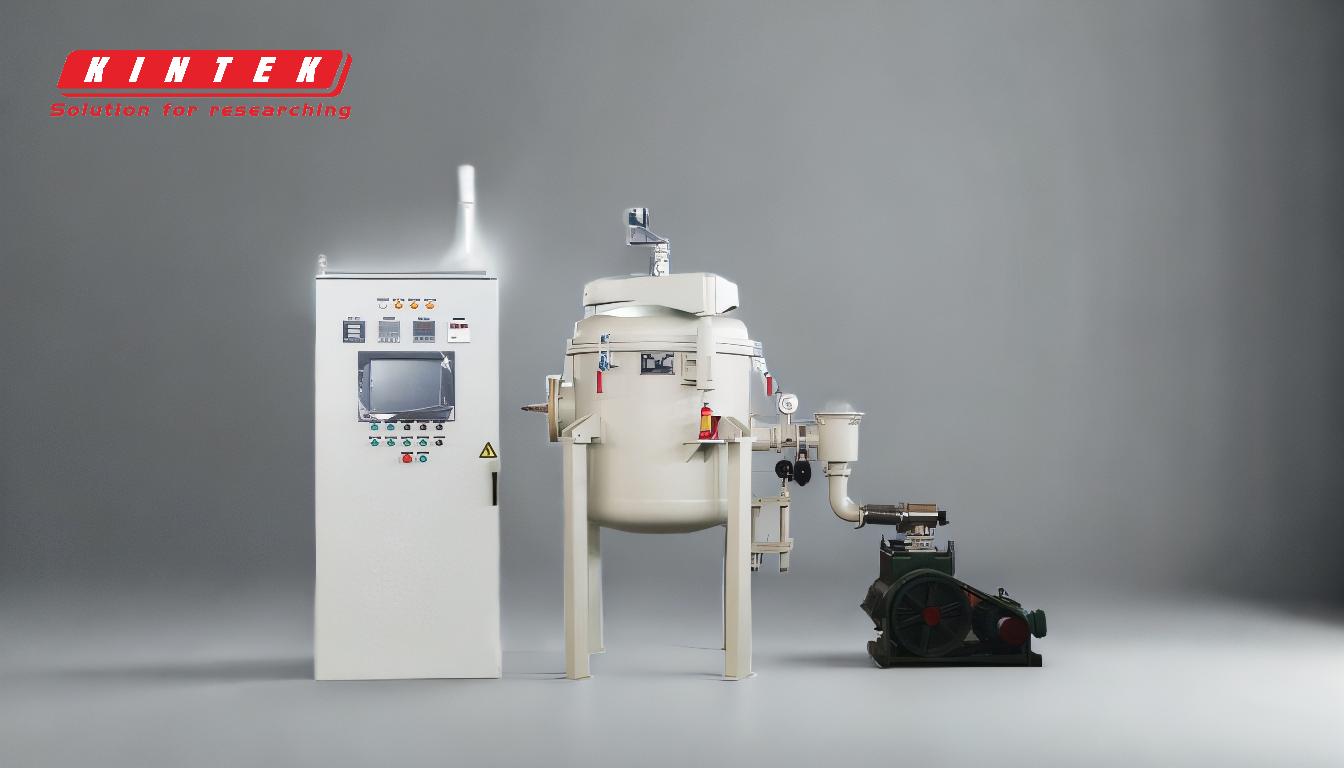
-
Frequency Range and Heating Depth:
- High-Frequency (100–500 kHz): Ideal for small, thin materials where shallow heating depths are required. Higher frequencies result in lower penetration depths, making them suitable for surface heating or thin cross-sections.
- Medium and Low Frequencies: Better for larger, thicker materials requiring deeper heat penetration. Lower frequencies allow heat to penetrate further into the material, which is essential for applications like forging or bulk heating.
-
Material Properties:
- Material Type: Metals and conductive materials are typically used in induction heating. The material's resistivity and magnetic properties influence the heating efficiency.
- Size and Thickness: Smaller and thinner materials heat faster, while larger and thicker materials require lower frequencies for effective heating.
-
Application Requirements:
- Melting Material: The choice of frequency depends on the material being melted. For example, certain metals may require specific frequencies to achieve optimal melting efficiency.
- Stirring Effect: Lower frequencies can induce a stronger stirring effect in molten metals, which is beneficial for uniform mixing and temperature distribution.
- Noise and Efficiency: Higher frequencies may produce more noise, while lower frequencies might offer better energy efficiency for certain applications.
-
Design Considerations:
- Coil and Capacitor Design: The frequency of an induction heating system can be adjusted by changing the coil and compensating capacitor. This allows customization based on the material and process requirements.
- Power Supply Capacity: The power supply must account for the material's specific heat, mass, required temperature rise, and heat loss due to conduction, convection, and radiation.
-
Cost and Practicality:
- Purchase Cost: The selection of frequency should balance performance with cost. For example, low-power high-frequency equipment might achieve the same heating effect as higher-power ultra-audio equipment for certain workpieces, potentially reducing costs.
- Process Requirements: The frequency must align with the specific heating process, such as hardening, annealing, or melting, to ensure consistent and reliable results.
-
Temperature Variation and Power Utilization:
- Degree of Temperature Variation: The efficiency of induction heating depends on the required temperature change. More power is typically utilized to achieve greater temperature variations.
- Energy Efficiency: Lower frequencies may offer better energy efficiency for applications requiring deep heating, while higher frequencies are more efficient for surface heating.
By carefully considering these factors, the appropriate frequency for induction heating can be selected to achieve optimal performance, efficiency, and cost-effectiveness for the specific application.
Summary Table:
Factor | High-Frequency (100–500 kHz) | Medium/Low Frequencies |
---|---|---|
Heating Depth | Shallow (surface heating) | Deep (bulk heating) |
Material Size | Small, thin materials | Large, thick materials |
Applications | Surface hardening, thin sections | Forging, bulk heating |
Energy Efficiency | Higher for surface heating | Better for deep heating |
Stirring Effect | Minimal | Strong |
Noise Level | Higher | Lower |
Need help selecting the right frequency for your induction heating process? Contact our experts today for tailored solutions!