Heat treatment is a critical process in metallurgy and materials science, aimed at altering the physical and sometimes chemical properties of materials, particularly metals. The critical point of heat treatment refers to the specific temperature at which a material undergoes a phase change, enabling the desired transformation of its microstructure. For steel, this critical temperature is around 724°C, where it transforms into austenite, a phase that allows for further manipulation of its properties. Understanding and controlling this critical point is essential for achieving the desired mechanical properties, such as hardness, toughness, and ductility, in the final product.
Key Points Explained:
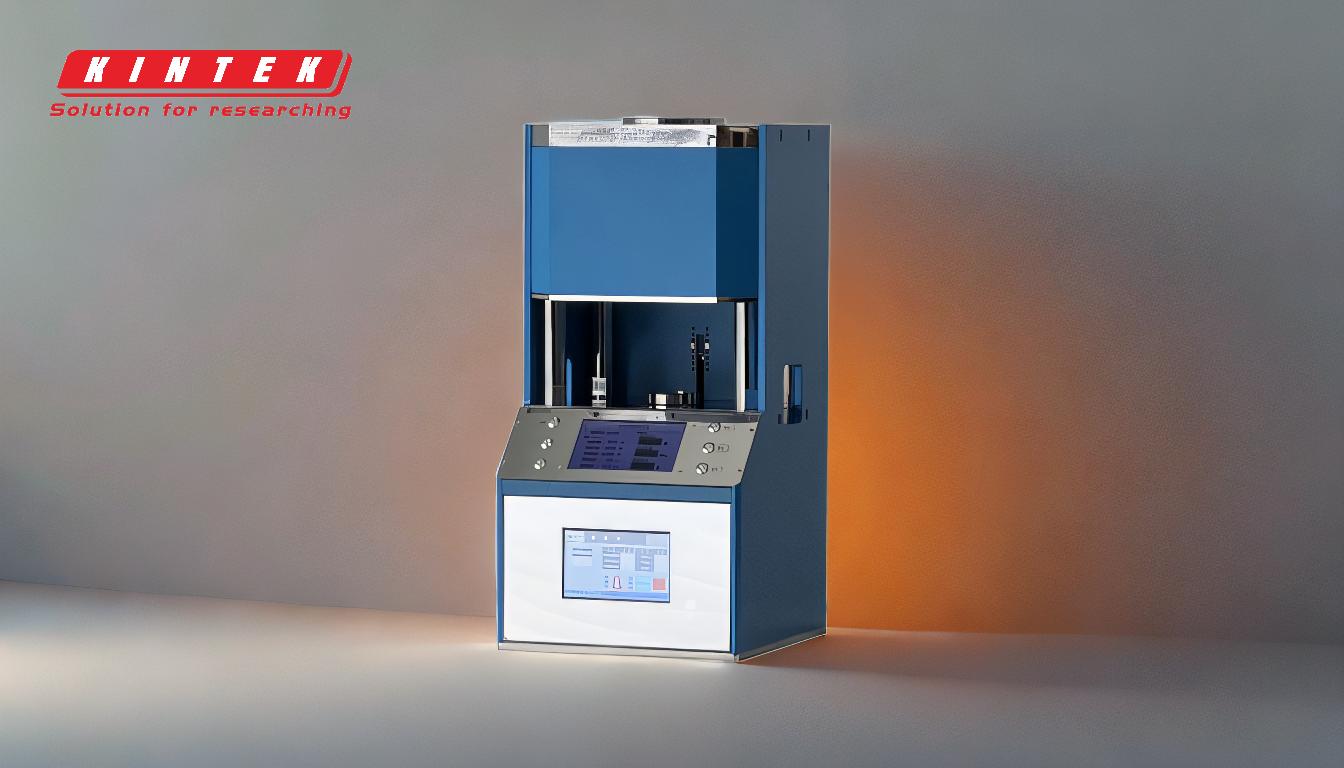
-
Definition of the Critical Temperature in Heat Treatment
- The critical temperature is the specific temperature at which a material undergoes a phase change, making its constituents miscible in all proportions. For steel, this is approximately 724°C, where it transforms into austenite. This phase change is crucial as it allows for the homogenization of the material's microstructure, setting the stage for subsequent heat treatment processes.
-
Importance of the Critical Temperature
- The critical temperature is pivotal because it marks the point at which the material's microstructure becomes malleable and can be altered to achieve desired properties. Without reaching this temperature, the material cannot undergo the necessary transformations to improve its mechanical properties, such as hardness, toughness, and ductility.
-
Phase Change and Microstructural Transformation
- When steel is heated above its critical temperature, it transforms into austenite, a face-centered cubic (FCC) structure. This transformation is essential for processes like quenching and tempering, which rely on the ability to manipulate the austenitic phase to achieve specific material properties.
-
Applications of Heat Treatment Processes
- Heat treatment encompasses a variety of processes, each designed to achieve specific characteristics in materials:
- Annealing: Softens metal or plastic, making it more ductile and less brittle.
- Hardening: Increases the hardness of metal through processes like through hardening, case hardening, carburizing, and nitriding.
- Localized Hardening or Softening: Techniques like induction and flame hardening allow for targeted treatment of specific areas on a part.
- Stress Relief: Removes internal stresses from materials before or after machining, forming, extruding, cutting, or bending.
- Resilience Addition: Processes like austempering and marquenching add spring-like resilience to metals.
- Magnetic Permeability Alteration: Techniques such as magnetic annealing and mu metal annealing change the magnetic properties of materials.
- Heat treatment encompasses a variety of processes, each designed to achieve specific characteristics in materials:
-
Control and Precision in Heat Treatment
- Achieving the desired material properties requires precise control over the heat treatment process, particularly the temperature and cooling rates. The critical temperature must be carefully monitored and maintained to ensure the material undergoes the correct phase transformations. This precision is crucial for applications where material performance is critical, such as in aerospace, automotive, and construction industries.
-
Impact on Material Properties
- The heat treatment process, guided by the critical temperature, significantly impacts the final properties of the material. For example, quenching steel from the austenitic phase results in a hard but brittle martensitic structure, which can then be tempered to achieve a balance of hardness and toughness. The ability to control these transformations allows for the customization of material properties to meet specific application requirements.
-
Technological and Industrial Relevance
- Understanding and applying the principles of heat treatment, particularly the critical temperature, is essential in various industries. It enables the production of materials with tailored properties, enhancing the performance and longevity of components. This knowledge is also crucial for innovation in material science, leading to the development of new alloys and treatment techniques.
In summary, the critical point of heat treatment is a fundamental concept that underpins the ability to manipulate and enhance the properties of materials. By understanding and controlling this critical temperature, engineers and material scientists can achieve the desired mechanical and physical properties in metals and other materials, making heat treatment a cornerstone of modern manufacturing and material science.
Summary Table:
Key Aspect | Details |
---|---|
Critical Temperature | ~724°C for steel, where it transforms into austenite. |
Importance | Enables phase change and microstructural transformation for desired properties. |
Applications | Annealing, hardening, stress relief, resilience addition, and more. |
Impact on Properties | Determines hardness, toughness, and ductility of materials. |
Industrial Relevance | Essential in aerospace, automotive, and construction industries. |
Ready to optimize your heat treatment processes? Contact our experts today for tailored solutions!