The debinding process is a critical step in the manufacturing of parts using powder injection molding (PIM) or metal injection molding (MIM). It involves the removal of the binder, a temporary material used to hold the powder particles together during the initial shaping of the part. The debinding process is essential to ensure that the final product has the desired mechanical properties and dimensional accuracy. This process can be achieved through various methods, including thermal debinding, solvent debinding, or catalytic debinding, each with its own advantages and limitations. The choice of debinding method depends on the type of binder used, the material of the part, and the desired properties of the final product.
Key Points Explained:
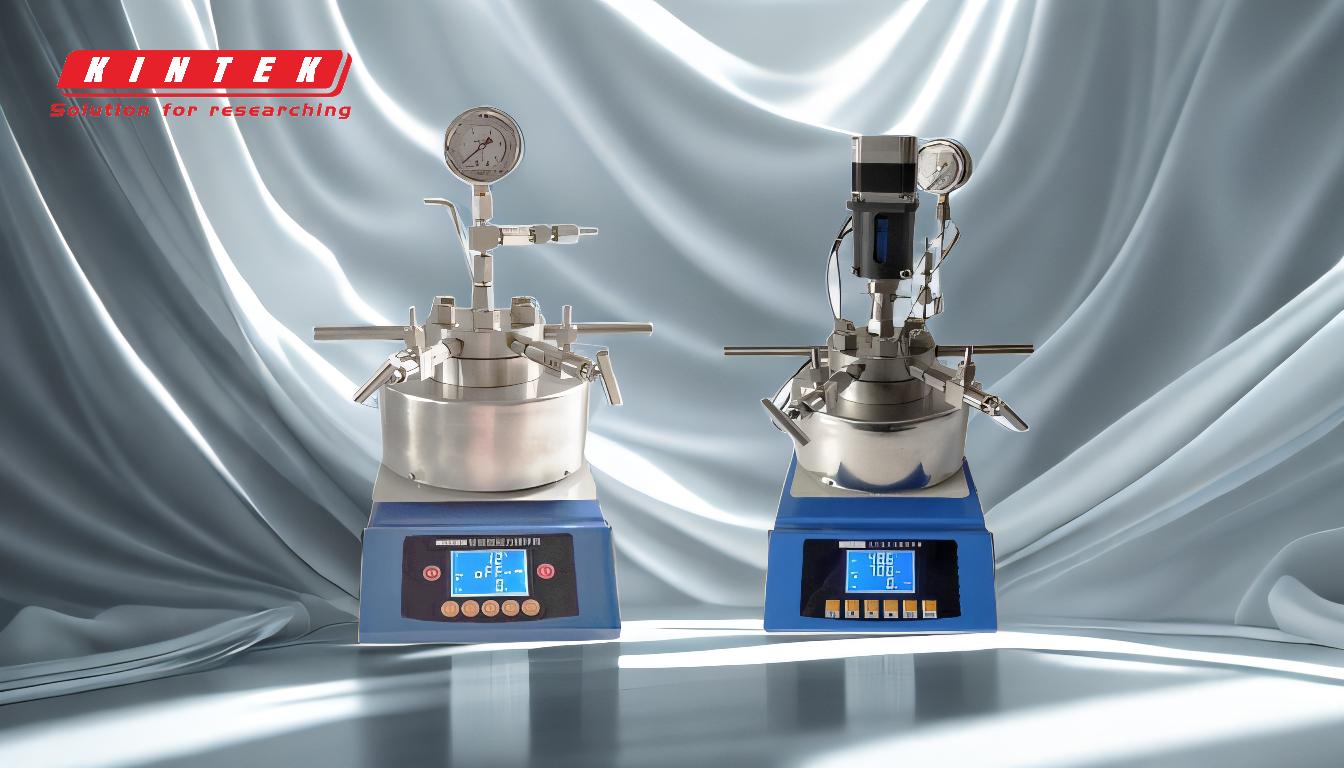
-
Definition of Debinding:
- Debinding is the process of removing the binder material from a green part (a part that has been shaped but not yet sintered) in powder injection molding. The binder is typically a polymer or wax that is mixed with the metal or ceramic powder to facilitate the shaping process. Once the part is shaped, the binder must be removed to allow the powder particles to sinter together during the final sintering process.
-
Importance of Debinding:
- The debinding process is crucial because any residual binder left in the part can lead to defects such as cracks, voids, or distortion during the sintering process. Proper debinding ensures that the final product has the desired mechanical properties, dimensional accuracy, and surface finish. It also helps in achieving a uniform density throughout the part, which is essential for its performance in applications.
-
Methods of Debinding:
- Thermal Debinding: This is the most common method, where the green part is heated in a controlled environment to decompose and evaporate the binder. The temperature is gradually increased to avoid rapid gas evolution, which could cause cracking or bloating. Thermal debinding is suitable for a wide range of materials but requires careful control of temperature and atmosphere.
- Solvent Debinding: In this method, the green part is immersed in a solvent that dissolves the binder. The solvent penetrates the part and dissolves the binder, which is then removed by evaporation or extraction. Solvent debinding is faster than thermal debinding but is limited to binders that are soluble in the chosen solvent.
- Catalytic Debinding: This method involves the use of a catalyst to break down the binder into smaller molecules that can be easily removed. Catalytic debinding is typically used for parts made with specific binders that are sensitive to catalytic decomposition. It offers a faster debinding rate and can be more energy-efficient than thermal debinding.
-
Challenges in Debinding:
- One of the main challenges in the debinding process is ensuring that the binder is removed uniformly throughout the part. Non-uniform debinding can lead to differential shrinkage during sintering, resulting in warping or cracking. Another challenge is controlling the rate of binder removal to prevent the formation of defects. Rapid removal of the binder can cause the part to collapse or develop cracks, while slow removal can prolong the manufacturing process.
-
Post-Debinding Considerations:
- After debinding, the part is in a fragile state known as the "brown part." It has a porous structure with the powder particles loosely held together. The brown part must be handled carefully to avoid damage before it undergoes the final sintering process. Sintering involves heating the part to a temperature below its melting point, causing the powder particles to bond together and form a dense, solid part.
-
Applications of Debinding:
- The debinding process is widely used in the production of complex-shaped parts for various industries, including automotive, aerospace, medical, and electronics. Parts produced using PIM or MIM often require intricate geometries and high precision, making debinding a critical step in achieving the desired final properties.
In summary, the debinding process is a vital step in powder injection molding that ensures the removal of the binder material from the green part. It plays a significant role in determining the quality and performance of the final product. The choice of debinding method depends on the material, binder, and desired properties, and careful control of the process is essential to avoid defects and achieve optimal results.
Summary Table:
Aspect | Details |
---|---|
Definition | Removal of binder material from a green part in powder injection molding. |
Importance | Ensures mechanical properties, dimensional accuracy, and uniform density. |
Methods | Thermal, solvent, and catalytic debinding, each with unique advantages. |
Challenges | Uniform binder removal, rate control, and avoiding defects. |
Post-Debinding | Fragile brown part requires careful handling before sintering. |
Applications | Automotive, aerospace, medical, and electronics industries. |
Need expert guidance on debinding for your powder injection molding process? Contact us today to learn more!