Sintering and heat treatment are both thermal processes used in materials science, but they serve different purposes and operate under different principles. Sintering involves heating powdered materials below their melting point to form a solid object, often used in powder metallurgy and ceramics. Heat treatment, on the other hand, involves heating and cooling metals or alloys to alter their physical and mechanical properties, such as hardness, strength, and ductility. While sintering focuses on bonding particles together to create a cohesive structure, heat treatment aims to modify the microstructure of a material to achieve desired properties. Both processes are essential in manufacturing but are applied based on the specific requirements of the material and the intended outcome.
Key Points Explained:
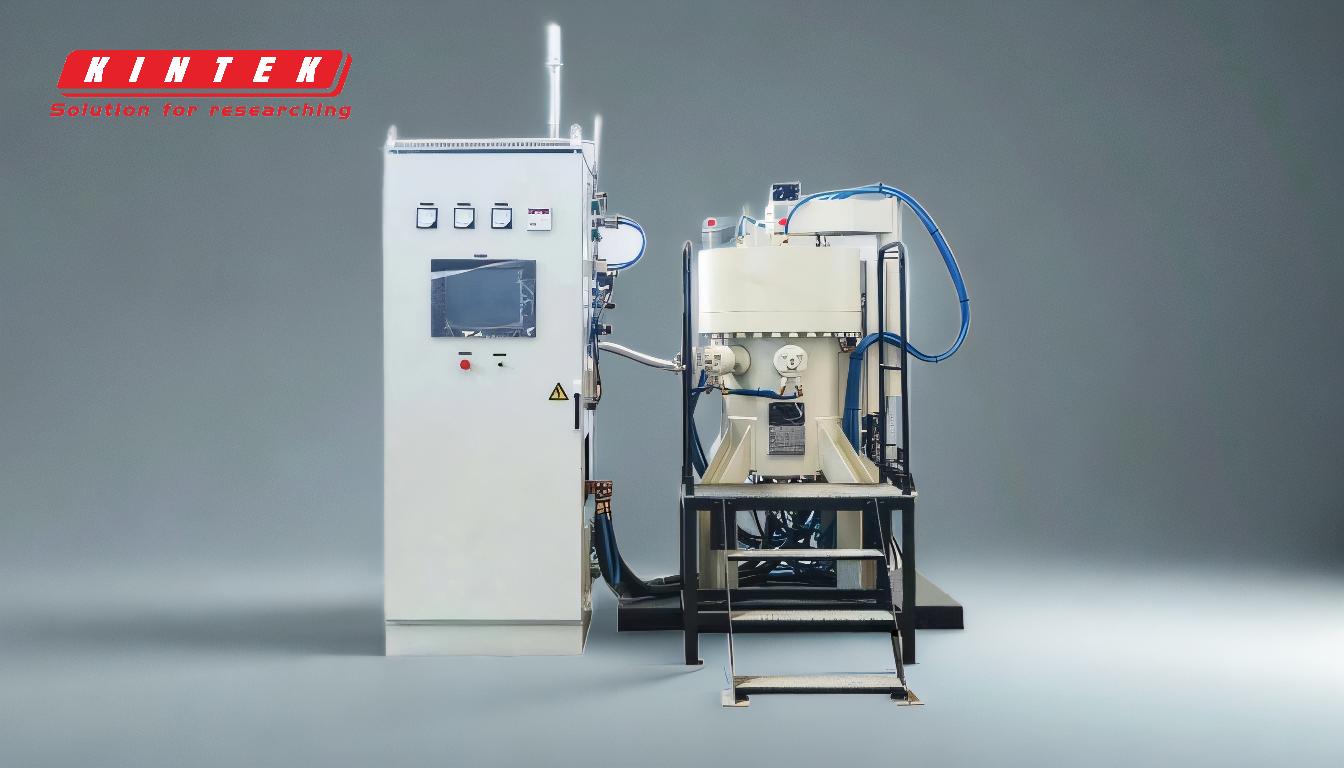
-
Definition and Purpose:
- Sintering: A process where powdered materials are heated below their melting point to form a solid object. This is commonly used in powder metallurgy and ceramics to create components with specific shapes and properties.
- Heat Treatment: A process that involves heating and cooling metals or alloys to alter their physical and mechanical properties. This can include processes like annealing, quenching, and tempering, which are used to achieve desired hardness, strength, and ductility.
-
Temperature Range:
- Sintering: Occurs at temperatures below the melting point of the material. This allows the particles to bond together without fully melting, which is energy-efficient and helps maintain the material's original properties.
- Heat Treatment: Can involve a wide range of temperatures, from below the melting point to just above it, depending on the specific treatment process. For example, annealing typically involves heating the material to a specific temperature and then allowing it to cool slowly.
-
Applications:
- Sintering: Primarily used in the production of complex shapes and components from powdered metals, ceramics, and other materials. It is also used in the manufacturing of filters, bearings, and other porous materials.
- Heat Treatment: Used to enhance the mechanical properties of metals and alloys, making them suitable for various applications such as automotive parts, tools, and structural components.
-
Process Complexity:
- Sintering: Generally involves fewer complex parameters and is more straightforward, especially in cases where the process conditions are well-defined and controllable.
- Heat Treatment: Can be more complex, involving multiple stages of heating and cooling, and often requires precise control over temperature, time, and cooling rates to achieve the desired material properties.
-
Energy Consumption:
- Sintering: Typically requires less energy compared to melting, as it occurs at lower temperatures. This makes it a more energy-efficient process for certain applications.
- Heat Treatment: Can be more energy-intensive, especially in processes that require high temperatures and rapid cooling, such as quenching.
-
Material Properties:
- Sintering: Focuses on creating a cohesive structure from powdered materials, often resulting in components with good dimensional accuracy and controlled porosity.
- Heat Treatment: Aims to modify the microstructure of the material, leading to changes in hardness, strength, and ductility. This can significantly improve the performance of the material in its intended application.
In summary, while both sintering and heat treatment involve the application of heat to materials, they serve different purposes and are used in different contexts. Sintering is primarily used to form solid objects from powdered materials, while heat treatment is used to alter the properties of metals and alloys. Understanding the differences between these processes is crucial for selecting the appropriate method for a given application.
Summary Table:
Aspect | Sintering | Heat Treatment |
---|---|---|
Purpose | Bonds powdered materials to form solid objects | Alters physical and mechanical properties of metals/alloys |
Temperature Range | Below melting point | Below to above melting point |
Applications | Powder metallurgy, ceramics, filters, bearings | Automotive parts, tools, structural components |
Process Complexity | Straightforward, fewer parameters | Complex, involves precise control of temperature and cooling rates |
Energy Consumption | Lower energy use due to lower temperatures | Higher energy use, especially in high-temperature processes like quenching |
Material Properties | Creates cohesive structures with controlled porosity | Modifies microstructure to enhance hardness, strength, and ductility |
Need help choosing the right thermal process for your materials? Contact our experts today for tailored solutions!