Submerged arc furnaces (SAFs) and electric arc furnaces (EAFs) are both used for metal smelting and refining, but they differ significantly in design, operation, and application. SAFs are primarily used for producing ferroalloys and other non-ferrous metals, while EAFs are commonly employed in steelmaking. The key differences lie in their electrode configurations, heating mechanisms, and operational procedures. SAFs operate with submerged electrodes that generate heat through both arc energy and resistive heating, while EAFs rely on arc energy alone, with electrodes positioned above the charge. Additionally, SAFs are often continuous or semi-continuous processes, whereas EAFs are typically batch processes. Understanding these differences is crucial for selecting the appropriate furnace for specific industrial applications.
Key Points Explained:
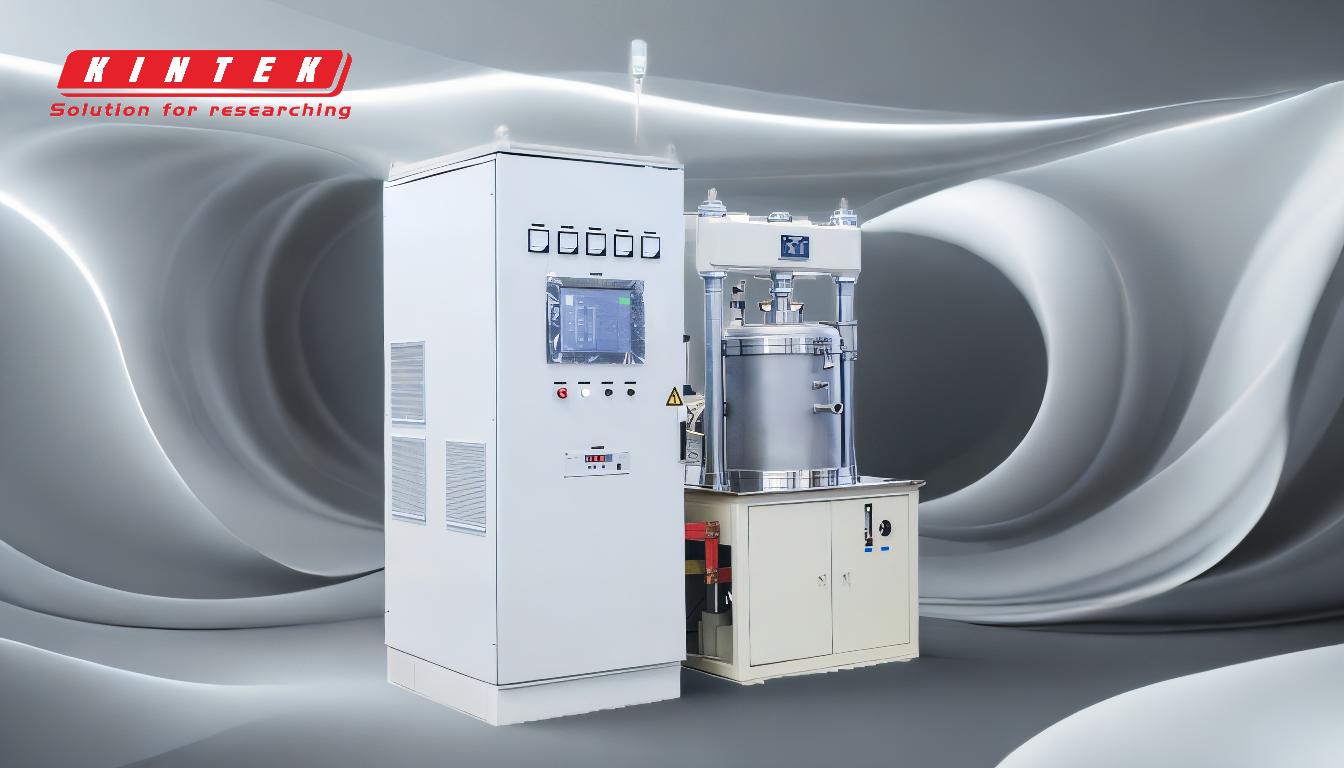
-
Electrode Configuration and Heating Mechanism:
-
Submerged Arc Furnace (SAF):
- Uses electrodes submerged in the charge material.
- Heat is generated through a combination of arc energy and resistive heating as current passes through the charge.
- The electrodes are typically made of graphite and are inserted into the charge to maintain a stable arc.
-
Electric Arc Furnace (EAF):
- Uses electrodes positioned above the charge material.
- Heat is generated primarily through arc energy between the electrodes and the charge.
- EAFs can be either AC (using three electrodes) or DC (using a single electrode with a bottom anode).
-
Submerged Arc Furnace (SAF):
-
Operational Procedure:
-
Submerged Arc Furnace (SAF):
- Operates in a continuous or semi-continuous manner.
- Materials are intermittently fed into the furnace, and a pounding machine maintains the material surface.
- Molten metal and slag accumulate at the bottom and are periodically discharged through a tap hole.
- The process is designed for high-temperature reactions, making it suitable for producing ferroalloys and other non-ferrous metals.
-
Electric Arc Furnace (EAF):
- Operates in a batch process.
- Scrap metal or other raw materials are loaded into the furnace, and the electrodes are lowered to create an arc.
- The charge is melted, refined, and then tapped for further processing.
- EAFs are commonly used in steelmaking, where they offer flexibility in terms of raw materials and energy efficiency.
-
Submerged Arc Furnace (SAF):
-
Design and Components:
-
Submerged Arc Furnace (SAF):
- Comprises a power supply system (e.g., submerged arc furnace transformer), high current conductor (short net), electrodes, electric furnace body, cooling system, feeding system, discharging system, and dust removal system.
- The furnace body is designed to handle high temperatures and corrosive environments.
-
Electric Arc Furnace (EAF):
- Typically includes a refractory-lined vessel, electrodes, a roof that can be swung aside for charging, and a tilting mechanism for tapping.
- DC EAFs may have a water-cooled metal anode or a conducting hearth at the bottom.
-
Submerged Arc Furnace (SAF):
-
Applications:
-
Submerged Arc Furnace (SAF):
- Primarily used for producing ferroalloys (e.g., ferrosilicon, ferromanganese) and non-ferrous metals (e.g., silicon metal, calcium carbide).
- Suitable for processes requiring high temperatures and controlled reduction reactions.
-
Electric Arc Furnace (EAF):
- Mainly used in steelmaking, particularly for recycling scrap metal.
- Also used for producing specialty steels and alloys.
-
Submerged Arc Furnace (SAF):
-
Energy Efficiency and Environmental Impact:
-
Submerged Arc Furnace (SAF):
- Generally more energy-efficient for specific applications due to the combined heating mechanism.
- Dust and gas emissions are managed through dust removal systems.
-
Electric Arc Furnace (EAF):
- Offers high energy efficiency in steelmaking, especially when using scrap metal.
- Modern EAFs are equipped with advanced emission control systems to minimize environmental impact.
-
Submerged Arc Furnace (SAF):
In summary, while both submerged arc furnaces and electric arc furnaces utilize electric arcs for heating, their design, operation, and applications differ significantly. SAFs are optimized for continuous or semi-continuous processes in ferroalloy and non-ferrous metal production, leveraging both arc and resistive heating. In contrast, EAFs are designed for batch processes in steelmaking, relying solely on arc heating. Understanding these differences is essential for selecting the appropriate furnace for specific industrial needs.
Summary Table:
Aspect | Submerged Arc Furnace (SAF) | Electric Arc Furnace (EAF) |
---|---|---|
Electrode Configuration | Submerged in charge material; heat from arc + resistive heating. | Positioned above charge; heat primarily from arc energy. |
Operational Procedure | Continuous or semi-continuous; intermittent feeding; periodic discharge of molten metal/slag. | Batch process; scrap metal loaded, melted, refined, and tapped for further processing. |
Design & Components | Includes power supply, electrodes, cooling, feeding, discharging, and dust removal systems. | Features refractory-lined vessel, electrodes, tilting mechanism, and optional DC anode. |
Applications | Produces ferroalloys (e.g., ferrosilicon) and non-ferrous metals (e.g., silicon metal). | Primarily used in steelmaking, especially for recycling scrap metal and producing specialty steels. |
Energy Efficiency | Energy-efficient for high-temperature reactions; dust/gas emissions managed. | High energy efficiency in steelmaking; modern systems minimize environmental impact. |
Need help choosing the right furnace for your industrial needs? Contact our experts today for personalized advice!