The efficiency of an induction furnace is influenced by several factors, including the design of the furnace, the characteristics of the material being heated, the inductor design, and the power supply capacity. Induction furnaces, particularly those using IGBT technology, are known for their high efficiency due to precise control over heating processes and reduced energy losses. The efficiency can be further enhanced by features like a double rail trolley system, which optimizes material handling and heat distribution. Overall, induction furnaces are highly efficient for applications requiring precise temperature control and rapid heating.
Key Points Explained:
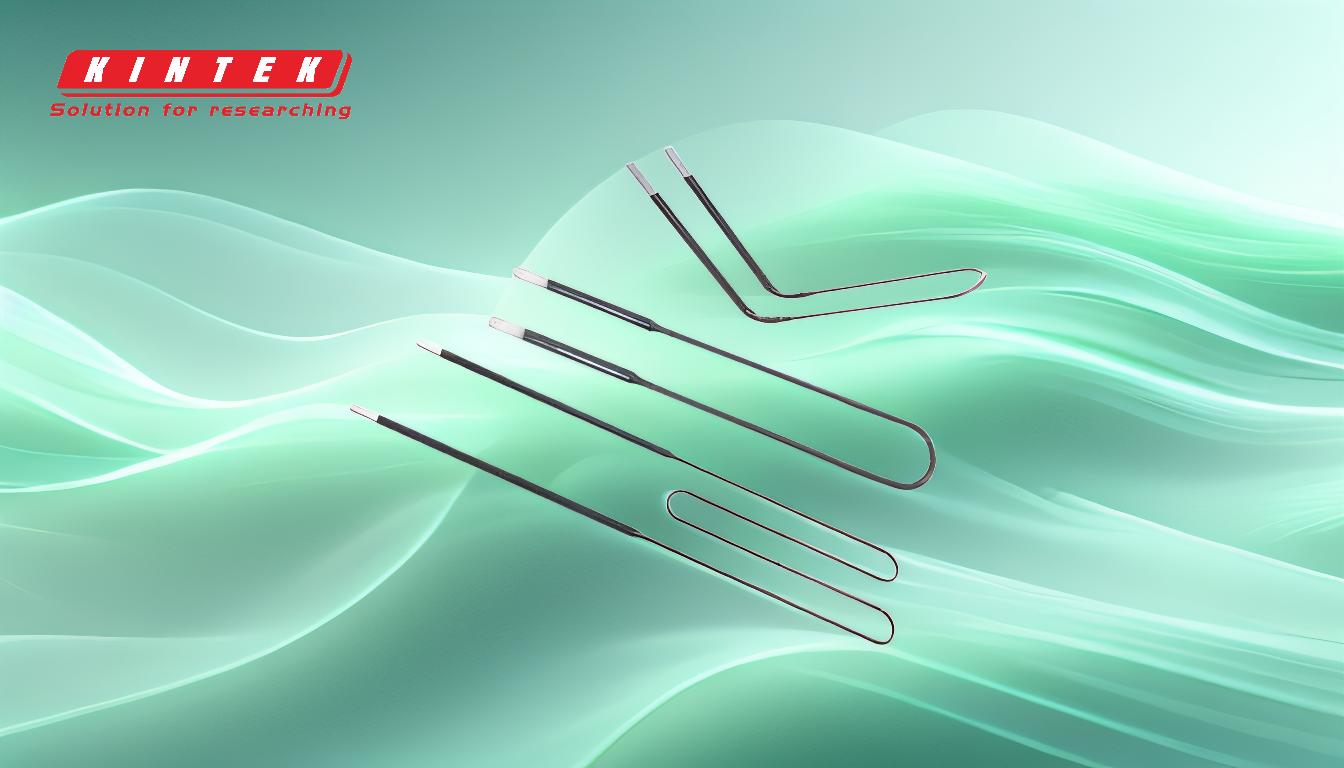
-
Efficiency Factors in Induction Furnaces:
- The efficiency of an induction furnace depends on several variables, including:
- Material Characteristics: The type and properties of the material being heated (e.g., conductivity, magnetic permeability) significantly impact efficiency.
- Inductor Design: The shape and configuration of the inductor coil affect how effectively energy is transferred to the material.
- Power Supply Capacity: A higher capacity power supply allows for faster heating and better efficiency, especially in applications requiring large temperature changes.
- Temperature Variation Requirements: Applications requiring a wide range of temperature changes may utilize more power, which can influence overall efficiency.
- The efficiency of an induction furnace depends on several variables, including:
-
Role of IGBT Technology:
- Induction furnaces equipped with IGBT (Insulated Gate Bipolar Transistor) technology are highly efficient due to their ability to provide precise control over the heating process. IGBTs enable rapid switching and minimize energy losses, making them ideal for applications requiring high-frequency induction heating.
-
Double Rail Trolley System:
- The inclusion of a double rail trolley system enhances efficiency by improving material handling and heat distribution. This feature reduces downtime and ensures consistent heating, which is particularly beneficial in industrial settings.
-
Applications and Efficiency:
- Induction furnaces are highly efficient for applications requiring precise temperature control, such as metal melting, heat treatment, and forging. Their ability to accommodate a wide range of temperature variations makes them versatile and energy-efficient.
-
Energy Savings:
- Compared to traditional heating methods, induction furnaces offer significant energy savings due to their direct heating mechanism, which minimizes heat loss to the surroundings. This makes them a cost-effective solution for high-temperature industrial processes.
By considering these factors, an induction furnace can achieve high efficiency, making it a preferred choice for various industrial applications.
Summary Table:
Factor | Impact on Efficiency |
---|---|
Material Characteristics | Conductivity and magnetic permeability of the material affect heating efficiency. |
Inductor Design | Coil shape and configuration influence energy transfer effectiveness. |
Power Supply Capacity | Higher capacity enables faster heating and better efficiency. |
IGBT Technology | Provides precise control, rapid switching, and minimizes energy losses. |
Double Rail Trolley System | Improves material handling and heat distribution, reducing downtime. |
Applications | Ideal for metal melting, heat treatment, and forging with precise temperature control. |
Energy Savings | Direct heating mechanism reduces heat loss, offering significant cost savings. |
Maximize your industrial heating efficiency with our advanced induction furnaces—contact us today to learn more!