Induction heating systems operate at varying frequencies depending on the application, material properties, and desired outcomes. The frequency of an induction heating system typically ranges from utility frequencies (50 or 60 Hz) to high frequencies (up to 500 kHz or higher). Lower frequencies are used for larger, thicker materials and applications requiring deeper heat penetration, while higher frequencies are suitable for smaller, thinner materials and surface heating. The choice of frequency is influenced by factors such as material type, size, resistivity, and the desired heating depth, which is governed by the skin effect. Understanding these principles helps in selecting the appropriate frequency for specific induction heating needs.
Key Points Explained:
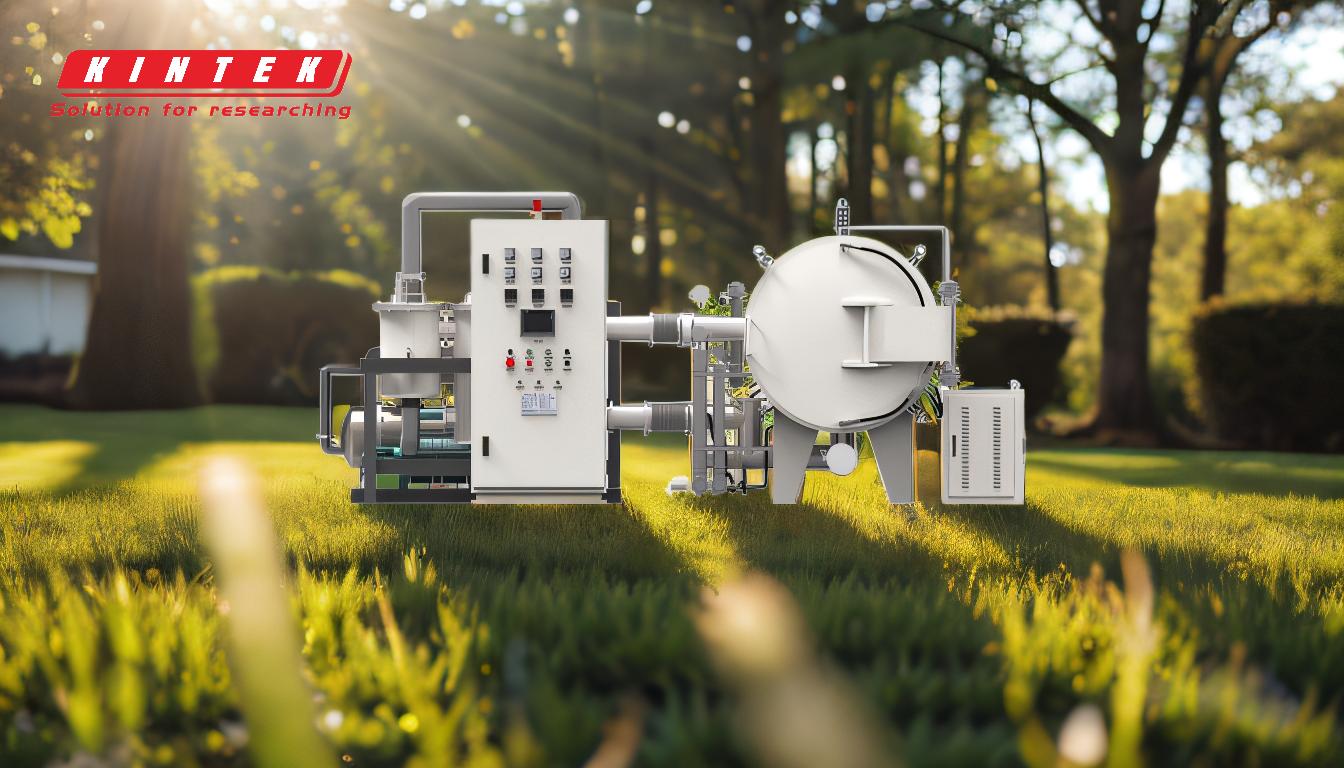
-
Frequency Range of Induction Heating Systems:
- Induction heating systems operate across a wide frequency spectrum, from utility frequencies (50 or 60 Hz) to high frequencies (up to 500 kHz or higher).
- Lower frequencies (50–60 Hz) are commonly used for large-scale industrial applications, such as melting large volumes of metal in induction furnaces.
- Medium frequencies (1–10 kHz) are often used for applications requiring moderate heating depths, such as forging or heat treatment of medium-sized components.
- High frequencies (100–500 kHz) are ideal for small, thin materials or surface heating applications, such as hardening or brazing.
-
Factors Influencing Frequency Selection:
- Material Type and Size: Smaller and thinner materials require higher frequencies due to the skin effect, which causes higher frequencies to generate heat closer to the surface. Larger and thicker materials benefit from lower frequencies for deeper heat penetration.
- Skin Depth Effect: The skin depth is the distance from the surface of a conductor where the current density drops to about 37% of its surface value. Higher frequencies result in shallower skin depths, making them suitable for surface heating.
- Desired Heating Depth: Applications requiring deep heating, such as melting large metal volumes, use lower frequencies. Conversely, surface treatments like hardening or annealing use higher frequencies.
- Material Resistivity: Materials with higher resistivity heat more efficiently at higher frequencies, while lower resistivity materials may require lower frequencies for effective heating.
-
Applications and Frequency Correlation:
- Low Frequency (50–60 Hz): Used for large-scale melting, such as in induction furnaces for steel or iron. These frequencies are also suitable for applications requiring significant stirring or turbulence in the melt.
- Medium Frequency (1–10 kHz): Ideal for heat treatment, forging, and melting medium-sized components. These frequencies balance heating depth and efficiency for a wide range of industrial applications.
- High Frequency (100–500 kHz): Best for surface heating applications, such as hardening, brazing, or annealing thin materials. High frequencies ensure rapid and localized heating.
-
Power Supply and Efficiency Considerations:
- The efficiency of an induction heating system depends on the power supply capacity, inductor design, and the required temperature change.
- Higher frequencies generally require more sophisticated and expensive power supplies but offer faster heating rates and better control for small or complex parts.
- Lower frequencies are more energy-efficient for large-scale applications but may lack the precision needed for smaller components.
-
Practical Implications for Equipment Selection:
- When selecting an induction heating system, consider the material properties (e.g., resistivity, size, and shape) and the desired outcome (e.g., surface hardening vs. deep heating).
- The inductor coil design and compensating capacitors can be adjusted to optimize performance for specific frequencies and applications.
- Noise levels, melting efficiency, and stirring effects are additional factors that may influence frequency selection in induction melting machines.
By understanding these key points, equipment and consumable purchasers can make informed decisions about the appropriate frequency for their specific induction heating needs, ensuring optimal performance and efficiency.
Summary Table:
Frequency Range | Applications | Key Characteristics |
---|---|---|
Low (50–60 Hz) | Large-scale melting, deep heating | Ideal for thick materials, energy-efficient for large volumes |
Medium (1–10 kHz) | Heat treatment, forging, medium-sized components | Balances heating depth and efficiency |
High (100–500 kHz) | Surface heating, hardening, brazing | Best for thin materials, rapid and localized heating |
Need help selecting the right induction heating frequency? Contact our experts today for tailored solutions!