The hot pressing process for polymers involves the application of heat and pressure to shape and consolidate polymer materials into a desired form. This technique is widely used in manufacturing to produce high-density, high-strength polymer components with precise dimensions. The process typically involves placing polymer powder or preforms in a mold, heating them to a temperature above their glass transition or melting point, and applying pressure to achieve the desired shape and density. The combination of heat and pressure ensures that the polymer flows and fills the mold, resulting in a uniform and dense final product. Hot pressing is commonly used in industries such as aerospace, automotive, and electronics for producing components like seals, gaskets, and insulators.
Key Points Explained:
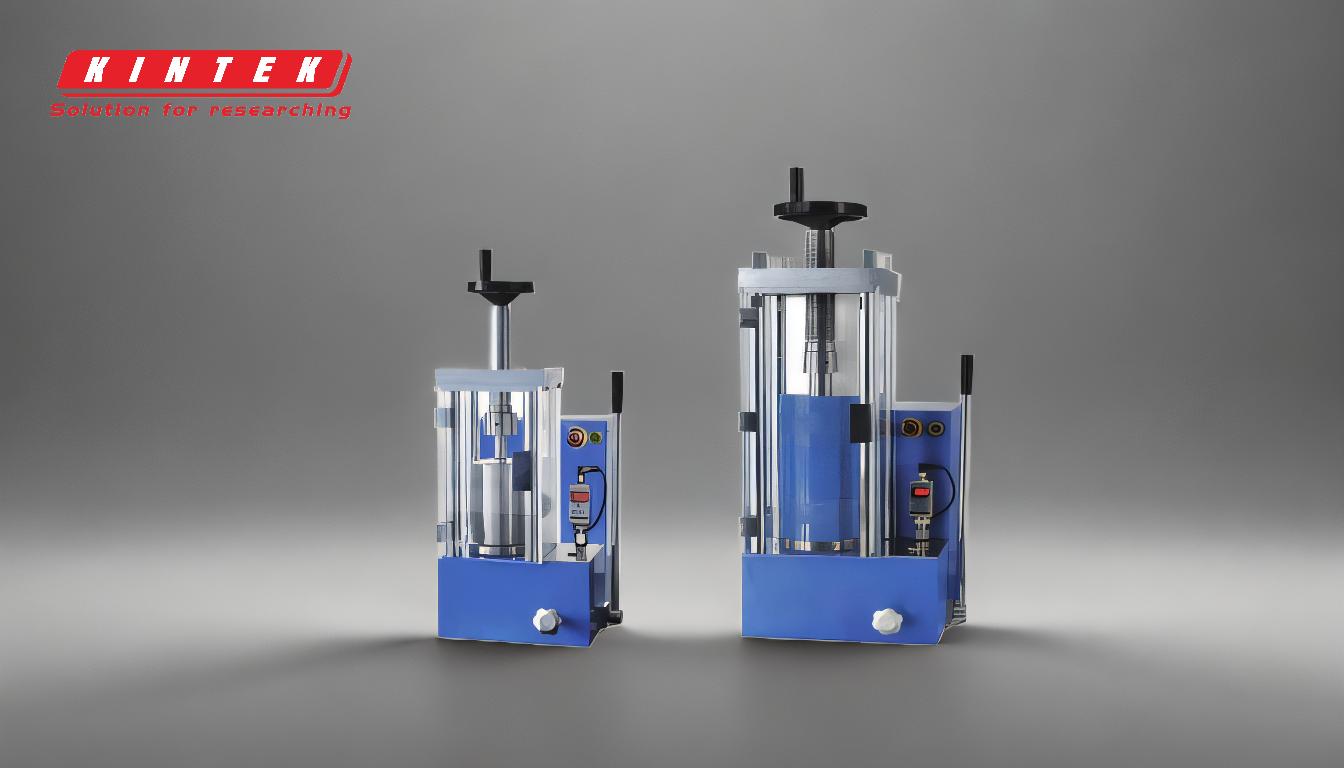
-
Definition of Hot Pressing Process for Polymers:
- The hot pressing process for polymers is a manufacturing technique that combines heat and pressure to shape and consolidate polymer materials. This method is particularly effective for producing high-density, high-strength polymer components with precise dimensions. The process is widely used in various industries due to its ability to produce parts with excellent mechanical properties and dimensional accuracy.
-
Steps Involved in the Hot Pressing Process:
- Preparation of Polymer Material: The process begins with the preparation of the polymer material, which can be in the form of powder, pellets, or preforms. The material is selected based on the desired properties of the final product.
- Molding: The polymer material is placed in a mold that is designed to the shape of the final product. The mold is typically made of a material that can withstand high temperatures and pressures.
- Heating: The mold containing the polymer material is heated to a temperature above the polymer's glass transition or melting point. This allows the polymer to become pliable and flowable.
- Application of Pressure: Once the polymer reaches the appropriate temperature, pressure is applied to the mold. The pressure helps to consolidate the polymer material, ensuring that it fills the mold completely and achieves the desired density.
- Cooling and Solidification: After the polymer has been shaped and consolidated, the mold is cooled to allow the polymer to solidify and retain its new shape. The cooling process must be controlled to prevent warping or other defects.
- Demolding: Once the polymer has solidified, the final product is removed from the mold. The product may undergo additional post-processing steps, such as trimming or surface finishing, to achieve the desired final specifications.
-
Advantages of Hot Pressing for Polymers:
- High Density and Strength: The combination of heat and pressure results in a final product with high density and strength, making it suitable for demanding applications.
- Precision and Consistency: Hot pressing allows for the production of components with precise dimensions and consistent properties, which is critical for applications in industries like aerospace and electronics.
- Versatility: The process can be used with a wide range of polymer materials, including thermoplastics, thermosets, and composites, making it versatile for various applications.
- Efficiency: Hot pressing is a relatively fast and efficient process, capable of producing high-quality parts in a short amount of time.
-
Applications of Hot Pressed Polymer Components:
- Aerospace: Hot pressed polymer components are used in aerospace applications for their high strength-to-weight ratio and resistance to extreme conditions. Examples include seals, gaskets, and insulators.
- Automotive: In the automotive industry, hot pressing is used to produce components such as bushings, bearings, and structural parts that require high durability and precision.
- Electronics: Polymer components produced through hot pressing are used in electronics for their insulating properties and ability to be molded into complex shapes. Examples include connectors, housings, and insulators.
- Medical Devices: The process is also used in the production of medical devices, where precision and biocompatibility are critical. Examples include surgical instruments and implantable devices.
-
Considerations for the Hot Pressing Process:
- Material Selection: The choice of polymer material is crucial, as it determines the properties of the final product. Factors to consider include thermal stability, mechanical properties, and compatibility with the intended application.
- Mold Design: The design of the mold must take into account the flow characteristics of the polymer, as well as the required shape and dimensions of the final product.
- Temperature and Pressure Control: Precise control of temperature and pressure is essential to ensure that the polymer flows properly and achieves the desired density and strength.
- Cooling Rate: The rate at which the polymer is cooled after pressing can affect the final properties of the product. Rapid cooling may lead to internal stresses, while slow cooling can result in better dimensional stability.
In summary, the hot pressing process for polymers is a versatile and efficient manufacturing technique that produces high-quality, high-strength components with precise dimensions. It is widely used in industries such as aerospace, automotive, electronics, and medical devices, where the properties of the final product are critical to performance. The process involves careful control of temperature, pressure, and cooling to achieve the desired results, making it a valuable method for producing advanced polymer components.
Summary Table:
Aspect | Details |
---|---|
Process Overview | Combines heat and pressure to shape and consolidate polymer materials. |
Steps | 1. Preparation 2. Molding 3. Heating 4. Pressure 5. Cooling 6. Demolding |
Advantages | High density, strength, precision, versatility, and efficiency. |
Applications | Aerospace, automotive, electronics, and medical devices. |
Key Considerations | Material selection, mold design, temperature/pressure control, cooling rate. |
Discover how hot pressing can elevate your polymer manufacturing—contact us today for expert guidance!