The maximum temperature for a SiC (silicon carbide) heating element is typically 1625°C (2927°F), as indicated by multiple references. However, some sources suggest that SiC heating elements can operate at temperatures up to 1550°C under standard conditions, with the potential to withstand even higher temperatures if required by specific processes. These elements are highly versatile and suitable for high-temperature applications, such as industrial furnaces, due to their ability to maintain structural integrity and performance at extreme temperatures.
Key Points Explained:
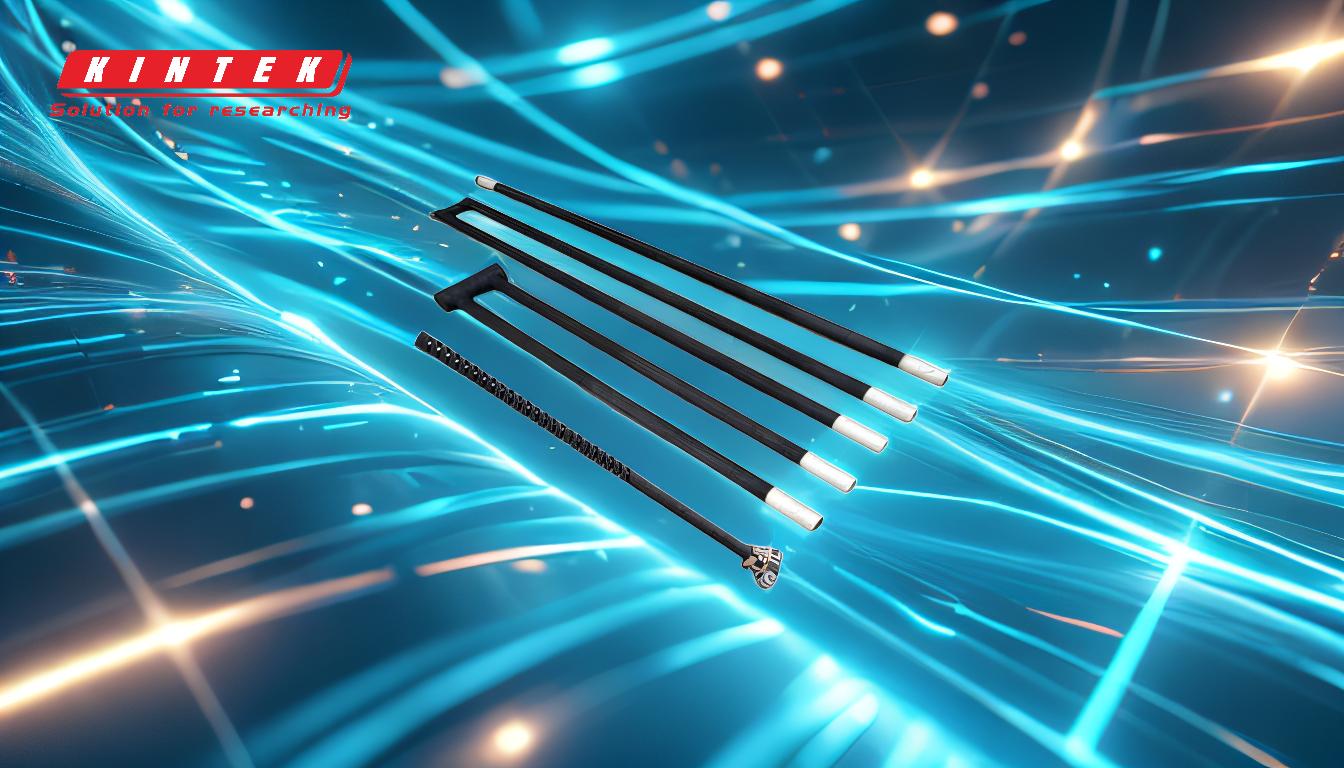
-
Maximum Temperature of SiC Heating Elements:
- The most commonly cited maximum temperature for SiC heating elements is 1625°C (2927°F). This is supported by multiple references, indicating that SiC elements are designed to operate reliably at this temperature.
- Some sources mention a slightly lower maximum temperature of 1550°C, which may reflect variations in manufacturing standards, element design, or specific application requirements.
-
Versatility in High-Temperature Applications:
- SiC heating elements are ideal for high-temperature environments, such as industrial furnaces, due to their ability to withstand extreme heat without significant degradation.
- They are commonly used in processes that require consistent and stable heating at temperatures well above 1000°C.
-
Operating Temperature Range:
- SiC heating elements typically operate within a range of 600°C to 1600°C, making them suitable for a wide variety of industrial and laboratory applications.
- Some specialized furnaces and processes may push the upper limit to 1625°C or beyond, depending on the specific requirements.
-
Customization and Design Flexibility:
- SiC heating elements are available in standard sizes and geometries, but they can also be customized to meet the unique needs of specific processes or equipment.
- This flexibility allows them to be tailored for optimal performance in high-temperature environments.
-
Factors Influencing Maximum Temperature:
- The maximum temperature a SiC heating element can withstand may vary based on factors such as:
- Element design and geometry.
- The specific application and process requirements.
- Environmental conditions, such as the presence of oxidizing or reducing atmospheres.
- For example, some processes may require elements to operate at temperatures slightly above the standard maximum, which can be accommodated with specialized designs.
- The maximum temperature a SiC heating element can withstand may vary based on factors such as:
-
Comparison to Other Heating Elements:
- SiC heating elements are preferred over other materials (e.g., metal or ceramic heating elements) for high-temperature applications due to their superior thermal stability, resistance to oxidation, and long service life.
- Their ability to operate at temperatures exceeding 1500°C makes them a reliable choice for demanding industrial processes.
-
Practical Considerations for Purchasers:
- When selecting SiC heating elements, consider:
- The maximum operating temperature required for your process.
- The element's compatibility with the furnace or equipment design.
- The expected service life and maintenance requirements under high-temperature conditions.
- Customized designs may be necessary for processes that require temperatures beyond the standard maximum.
- When selecting SiC heating elements, consider:
In summary, SiC heating elements are capable of withstanding temperatures up to 1625°C (2927°F), making them an excellent choice for high-temperature applications. Their versatility, durability, and ability to be customized for specific needs ensure reliable performance in demanding environments.
Summary Table:
Key Feature | Details |
---|---|
Maximum Temperature | 1625°C (2927°F) under optimal conditions |
Standard Operating Range | 600°C to 1600°C |
Versatility | Ideal for industrial furnaces and high-temperature processes |
Customization | Available in standard and custom designs for specific applications |
Durability | Resistant to oxidation and thermal degradation, ensuring long service life |
Need SiC heating elements for your high-temperature processes? Contact our experts today to find the perfect solution!