Ceramics are renowned for their thermal stability, making them suitable for high-temperature applications. The maximum temperature a ceramic can withstand depends on its composition, structure, and intended use. Traditional ceramics, such as those used in cooking vessels and serving dishes, typically have a maximum operating temperature of around 1,200°C to 1,400°C. However, advanced ceramics, like alumina or silicon carbide, can endure much higher temperatures, often exceeding 1,600°C to 2,000°C. The thermal stability of ceramics is influenced by factors such as purity, porosity, and the presence of additives. Below, we explore the key points in detail to understand the maximum temperature limits for ceramics and the factors affecting them.
Key Points Explained:
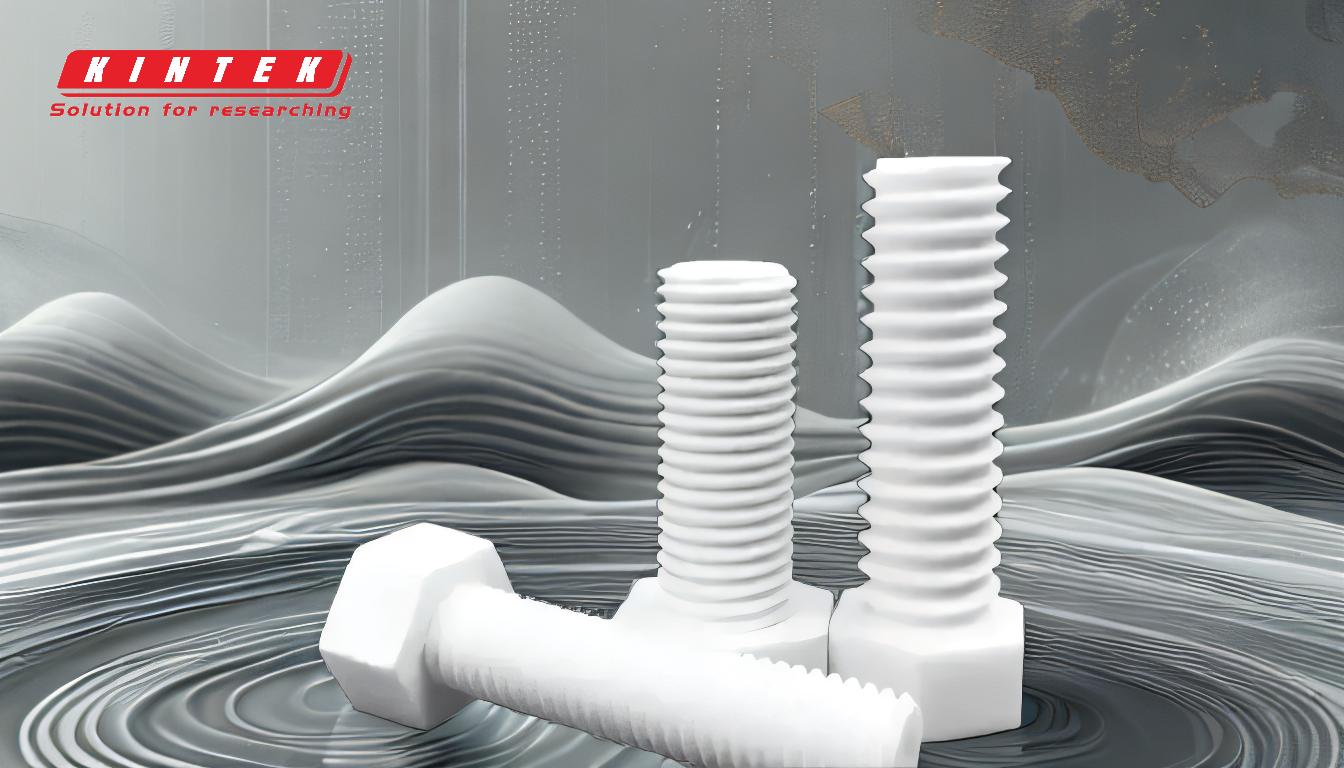
-
Definition of Ceramics and Their Thermal Properties
- Ceramics are inorganic, non-metallic materials that are typically crystalline in structure.
- Their thermal stability arises from strong ionic and covalent bonds, which provide high melting points and resistance to heat.
- Traditional ceramics, such as clay-based products, are stable up to 1,200°C to 1,400°C, while advanced ceramics can withstand significantly higher temperatures.
-
Types of Ceramics and Their Temperature Limits
-
Traditional Ceramics:
- Made from naturally occurring materials like clay, silica, and feldspar.
- Used in pottery, bricks, and tiles.
- Maximum temperature: 1,200°C to 1,400°C.
-
Advanced Ceramics:
- Engineered for high-performance applications.
- Examples include alumina (Al₂O₃), silicon carbide (SiC), and zirconia (ZrO₂).
- Maximum temperature: 1,600°C to 2,000°C or higher, depending on the material.
-
Traditional Ceramics:
-
Factors Affecting Maximum Temperature
-
Composition:
- Pure ceramics with fewer impurities generally have higher melting points.
- For example, alumina (99.5% pure) can withstand temperatures up to 2,000°C.
-
Porosity:
- Dense ceramics with low porosity are more resistant to thermal shock and high temperatures.
-
Additives:
- Certain additives can enhance thermal stability or lower the melting point, depending on the application.
-
Composition:
-
Applications and Temperature Requirements
-
Traditional Applications:
- Cooking vessels and serving dishes typically operate below 1,200°C.
-
Industrial Applications:
- Advanced ceramics are used in aerospace, automotive, and energy sectors, where temperatures can exceed 1,600°C.
- Examples include turbine blades, heat shields, and kiln linings.
-
Traditional Applications:
-
Thermal Shock Resistance
- Ceramics must not only withstand high temperatures but also resist sudden temperature changes.
- Materials with low thermal expansion coefficients, like silicon carbide, are better suited for applications involving rapid heating or cooling.
-
Limitations and Challenges
- Even advanced ceramics have limits; prolonged exposure to extreme temperatures can lead to degradation.
- Factors like oxidation, creep, and chemical reactions at high temperatures can reduce the lifespan of ceramic components.
By understanding these key points, purchasers of ceramic equipment and consumables can make informed decisions based on the specific temperature requirements of their applications. Advanced ceramics offer superior performance for high-temperature environments, while traditional ceramics remain cost-effective for lower-temperature uses.
Summary Table:
Type of Ceramic | Maximum Temperature | Key Applications |
---|---|---|
Traditional Ceramics | 1,200°C – 1,400°C | Pottery, bricks, tiles, cooking vessels |
Advanced Ceramics | 1,600°C – 2,000°C+ | Aerospace, automotive, energy sectors |
Factors Affecting Temperature Limits | Details |
---|---|
Composition | Pure ceramics (e.g., 99.5% alumina) withstand higher temperatures. |
Porosity | Dense ceramics with low porosity resist thermal shock and high temperatures. |
Additives | Additives can enhance stability or lower melting points. |
Need high-temperature ceramics for your application? Contact our experts today to find the perfect solution!