The Chemical Vapor Deposition (CVD) process is a sophisticated method used to deposit high-quality thin films or solid materials onto substrates through chemical reactions in the gas phase. It involves introducing precursor gases into a reaction chamber, where they undergo activation (via heat, light, or plasma) and react to form a solid deposit on a substrate. The process is highly versatile, allowing for the deposition of a wide range of materials, including metals, ceramics, and semiconductors. Key steps include gas introduction, activation, chemical reaction, and deposition. The CVD process is distinguished by its ability to produce uniform, high-purity coatings and is widely used in industries such as electronics, optics, and materials science.
Key Points Explained:
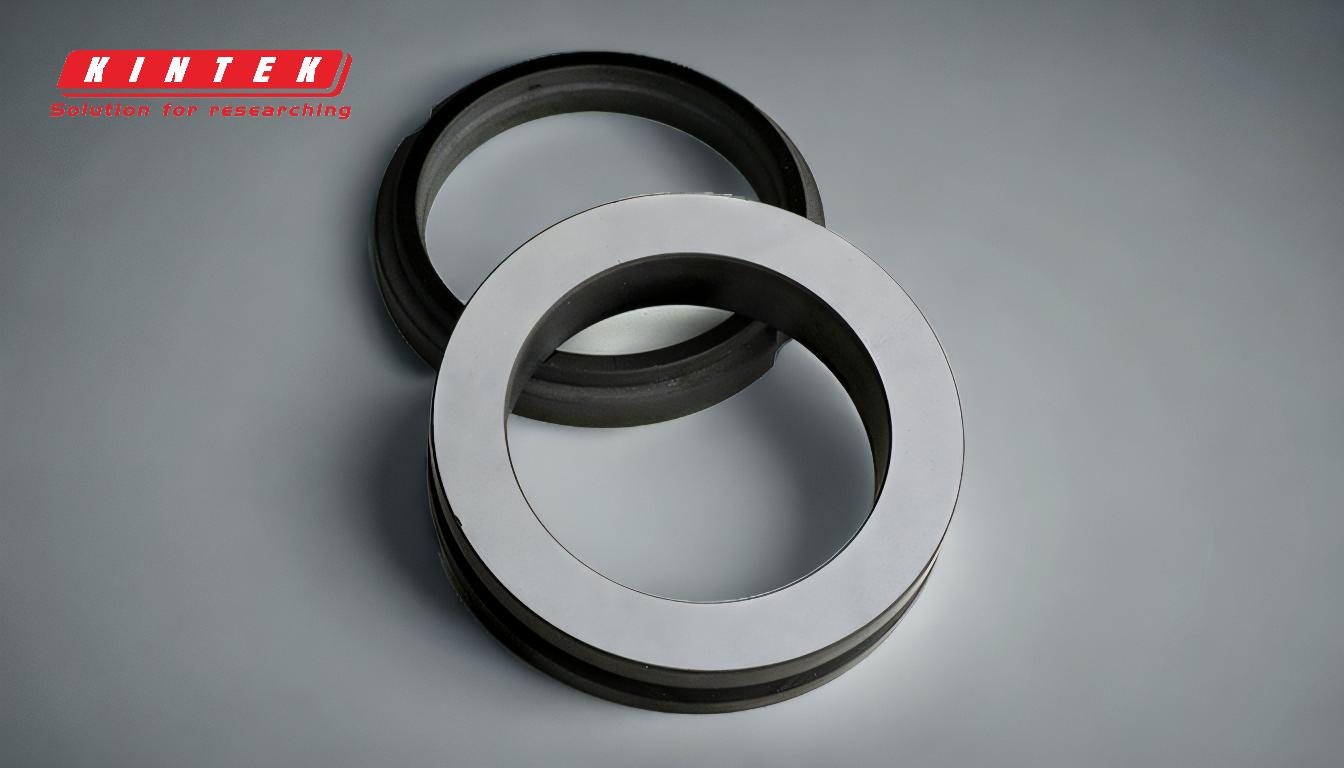
-
Introduction of Precursor Gases:
- Precursor gases, often diluted in carrier gases, are introduced into a reaction chamber. These gases contain the constituent atoms or molecules of the material to be deposited.
- Example: For diamond synthesis, gases like methane (CH₄) and hydrogen (H₂) are used.
- The gases flow over or around the substrate, ensuring uniform exposure.
-
Activation of Gaseous Reactants:
- The precursor gases are activated using energy sources such as heat, light, or electric discharge (plasma).
- Activation methods:
- Thermal CVD: Uses high temperatures (e.g., 800°C to 1400°C) to break chemical bonds.
- Plasma-Assisted CVD (PECVD): Uses plasma to generate reactive species at lower temperatures.
- Laser-Assisted CVD: Uses laser energy to initiate reactions.
- Activation dissociates the precursor gases into reactive radicals or ions, enabling chemical reactions.
-
Chemical Reactions:
- The activated gases undergo chemical reactions, which can occur:
- Homogeneously in the gas phase, forming intermediate species.
- Heterogeneously on the substrate surface, leading to film formation.
- Common reactions include pyrolysis (thermal decomposition), reduction, oxidation, and hydrolysis.
- Example: In diamond CVD, methane decomposes to release carbon atoms, which then bond to form diamond crystals.
- The activated gases undergo chemical reactions, which can occur:
-
Deposition of Thin Films:
- The products of the chemical reactions deposit onto the substrate, forming a thin film or solid layer.
- Deposition can occur in various forms:
- Crystalline: Ordered atomic structures (e.g., diamond, silicon).
- Amorphous: Non-crystalline structures (e.g., silicon dioxide).
- The process is multidirectional, ensuring uniform coverage even on complex geometries.
-
Substrate Heating:
- The substrate is typically heated to facilitate the chemical reactions and improve adhesion.
- Temperature ranges vary depending on the material and process:
- Low-temperature CVD: Below 500°C (e.g., for organic materials).
- High-temperature CVD: 800°C to 1400°C (e.g., for diamond or silicon carbide).
-
Chamber Environment:
- The reaction chamber is often operated under vacuum or controlled atmospheric conditions to minimize contamination and optimize reaction kinetics.
- Pressure and gas flow rates are carefully regulated to ensure consistent deposition.
-
Applications and Advantages:
- CVD is used to produce high-performance materials for:
- Electronics: Semiconductor devices, integrated circuits.
- Optics: Anti-reflective coatings, optical fibers.
- Materials Science: Diamond films, ceramics, and composites.
- Advantages include:
- High purity and uniformity of deposited films.
- Ability to coat complex shapes and multiple substrates simultaneously.
- Scalability for industrial production.
- CVD is used to produce high-performance materials for:
-
Challenges and Considerations:
- Process Complexity: Requires precise control of temperature, pressure, and gas flow.
- Cost: High energy consumption and equipment expenses.
- Safety: Handling of toxic or flammable precursor gases requires stringent safety measures.
By understanding these key points, one can appreciate the intricate mechanisms of the CVD process and its critical role in modern material science and technology.
Summary Table:
Key Aspect | Details |
---|---|
Precursor Gases | Introduced into a reaction chamber, often diluted in carrier gases. |
Activation Methods | Heat, light, or plasma to dissociate gases into reactive species. |
Chemical Reactions | Homogeneous (gas phase) or heterogeneous (substrate surface) reactions. |
Deposition | Forms thin films or solid layers, crystalline or amorphous. |
Substrate Heating | Facilitates reactions and adhesion; temperature varies by material. |
Chamber Environment | Operated under vacuum or controlled conditions for optimal deposition. |
Applications | Electronics, optics, materials science (e.g., semiconductors, diamond films). |
Advantages | High purity, uniformity, scalability, and ability to coat complex shapes. |
Challenges | Process complexity, high costs, and safety concerns with precursor gases. |
Discover how the CVD process can revolutionize your material applications—contact our experts today!