The powder sintering process is a manufacturing technique used to transform powdery materials into dense, solid bodies by applying heat and pressure without reaching the material's melting point. This process is widely used in industries such as powder metallurgy, ceramics, and plastics to create strong, durable, and complex-shaped components. The process typically involves several key steps, including powder preparation, mixing, forming, sintering, and post-treatment. Sintering relies on the diffusion of atoms across particle boundaries, which fuses the particles together into a cohesive mass. This method is particularly useful for materials with high melting points, such as metals like tungsten and molybdenum, as well as ceramics and polymers.
Key Points Explained:
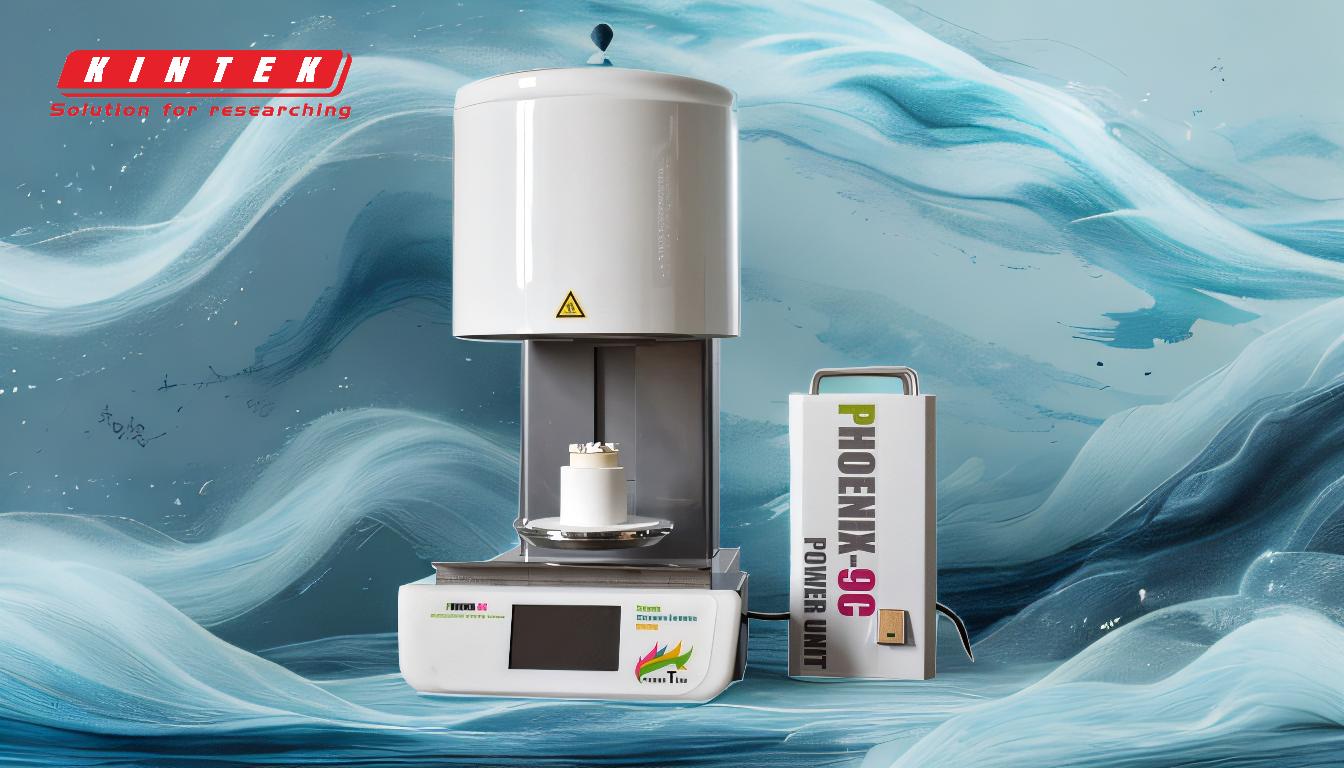
-
Definition of Sintering:
- Sintering is a process that transforms powdery materials into dense, solid bodies by applying heat and pressure below the material's melting point.
- It is used in various industries, including powder metallurgy, ceramics, and plastics, to create durable and complex-shaped components.
-
Key Steps in the Sintering Process:
- Powder Making: The process begins with the production of fine metal, ceramic, or plastic powders. These powders are often produced through methods like atomization, chemical reduction, or mechanical milling.
- Mixing: The powders are then mixed with binders or other additives to improve flowability and ensure uniform distribution of particles.
- Forming: The mixed powder is compacted into a desired shape using techniques such as die pressing, isostatic pressing, or injection molding. This step creates a "green compact," which is a fragile, pre-sintered shape.
- Sintering: The green compact is heated in a controlled environment (e.g., a furnace) at temperatures below the material's melting point. During this stage, atomic diffusion occurs, causing the particles to bond and densify into a solid mass.
- Post-Treatment: After sintering, additional processes such as machining, heat treatment, or surface finishing may be applied to achieve the final product's desired properties and dimensions.
-
Mechanism of Sintering:
- Sintering relies on the diffusion of atoms across the boundaries of adjacent particles. As the temperature increases, atoms migrate from areas of high energy to low energy, causing the particles to fuse together.
- This atomic diffusion reduces porosity and increases the density of the material, resulting in a stronger and more durable final product.
-
Applications of Sintering:
- Powder Metallurgy: Sintering is widely used to produce metal components such as gears, bearings, and filters. It allows for the creation of complex shapes with high precision and minimal waste.
- Ceramics: Sintering is essential in the production of ceramic materials, including tiles, insulators, and advanced ceramics used in electronics and aerospace.
- Plastics: Sintering is used in additive manufacturing (e.g., selective laser sintering) to create plastic parts with intricate geometries.
-
Advantages of Sintering:
- Material Efficiency: Sintering minimizes material waste, as the process uses powders that can be precisely shaped and compacted.
- Complex Shapes: It enables the production of complex and intricate shapes that would be difficult or impossible to achieve with traditional machining methods.
- High Strength and Durability: The sintering process results in materials with high density, strength, and wear resistance.
-
Challenges and Considerations:
- Temperature Control: Precise control of temperature and heating rates is critical to avoid defects such as warping or incomplete sintering.
- Material Selection: Not all materials are suitable for sintering, as some may oxidize or degrade at high temperatures.
- Post-Processing: Additional steps such as machining or coating may be required to achieve the desired surface finish or dimensional accuracy.
-
Examples of Sintered Materials:
- Metals: Tungsten, molybdenum, iron, and stainless steel are commonly sintered to produce high-performance components.
- Ceramics: Alumina, zirconia, and silicon carbide are sintered for use in high-temperature and wear-resistant applications.
- Plastics: Polyamide (nylon) and other polymers are sintered in additive manufacturing processes to create lightweight and durable parts.
By understanding the powder sintering process, manufacturers can leverage its advantages to produce high-quality components with tailored properties for a wide range of applications.
Summary Table:
Key Aspect | Details |
---|---|
Definition | Transforms powders into dense solids using heat and pressure below melting point. |
Key Steps | Powder making, mixing, forming, sintering, post-treatment. |
Mechanism | Atomic diffusion fuses particles, reducing porosity and increasing density. |
Applications | Powder metallurgy, ceramics, plastics. |
Advantages | Material efficiency, complex shapes, high strength and durability. |
Challenges | Temperature control, material selection, post-processing. |
Examples | Metals (tungsten, molybdenum), ceramics (alumina), plastics (nylon). |
Discover how the powder sintering process can enhance your manufacturing capabilities—contact us today!