The pressing method in ceramics is a critical process used to shape ceramic materials into desired forms with high precision and uniformity. This method involves applying pressure to ceramic powders or preforms within a mold or die, often using specialized equipment like a pressing furnace. The process ensures that the ceramic material achieves optimal mechanical properties and dimensional accuracy. Key aspects include proper burnout cycles, precise control of time and temperature, and the use of techniques like semi-isostatic pressing to ensure uniformity. These steps are essential for producing high-quality ceramic components with consistent performance and structural integrity.
Key Points Explained:
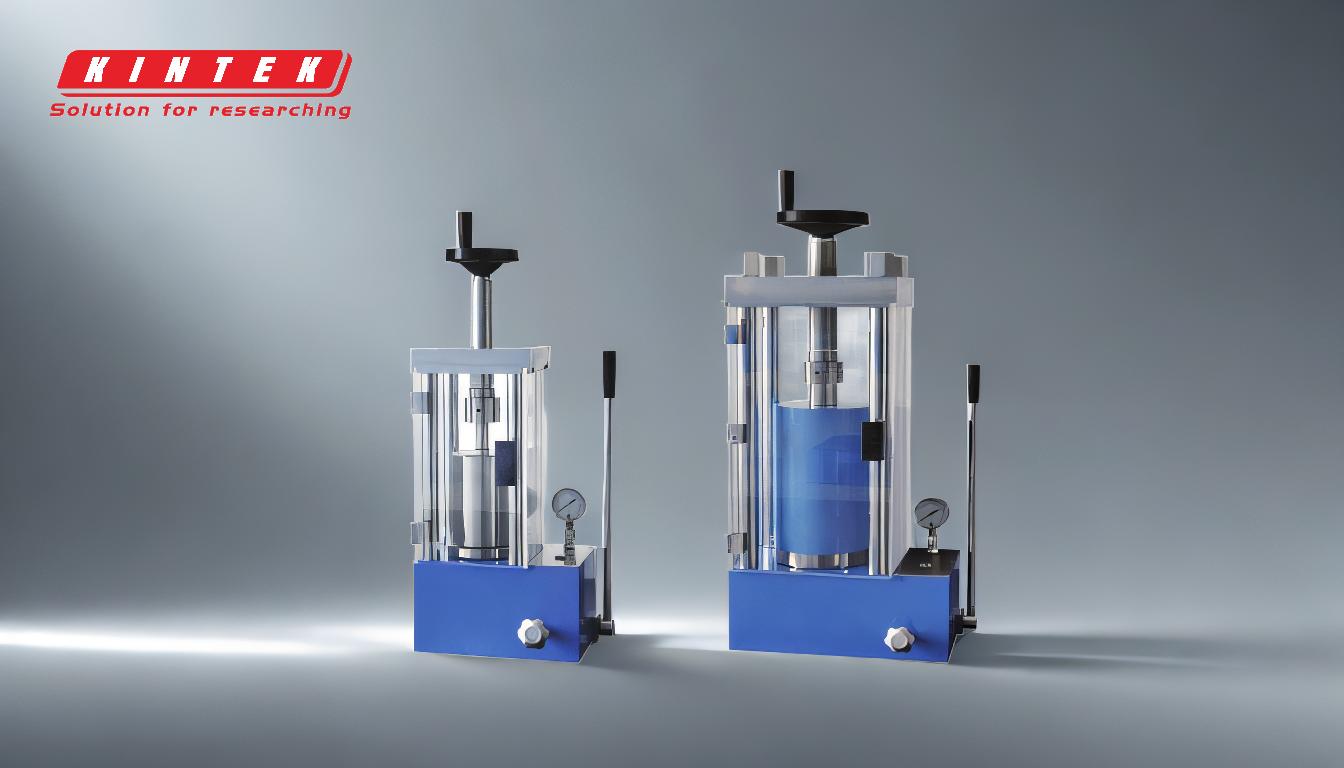
-
Pressing Process Overview:
- The pressing method in ceramics involves shaping ceramic materials by applying pressure within a mold or die. This is typically done using a pressing furnace, where ceramic powders or preforms are compressed to form the desired shape.
- The process includes inserting an ingot and plunger into the furnace, followed by applying controlled pressure to the ceramic material. This step ensures the material is densely packed and free of voids, which is crucial for achieving high mechanical strength.
-
Importance of Burnout:
- Proper burnout is a critical step in the pressing process. It involves heating the ceramic material to remove any organic binders or impurities that may have been introduced during the initial forming stages.
- Burnout must be carefully controlled in terms of time and temperature to prevent defects such as cracking or warping. This step ensures the final product has a uniform structure and optimal mechanical properties.
-
Semi-Isostatic Pressing:
- Semi-isostatic pressing is a specialized technique used to achieve uniform pressure distribution across the ceramic material. This method is particularly important for complex shapes or large components, where uneven pressure could lead to defects.
- By ensuring uniformity, semi-isostatic pressing enhances the mechanical performance and dimensional accuracy of the final product. This technique is widely used in industries requiring high-precision ceramic components, such as aerospace and electronics.
-
Time and Temperature Control:
- Precise control of time and temperature during the pressing process is essential for producing high-quality ceramics. Incorrect settings can lead to issues such as incomplete densification, cracking, or dimensional inaccuracies.
- Modern pressing furnaces are equipped with advanced controls to monitor and adjust these parameters in real-time, ensuring consistent results and reducing the risk of defects.
-
Applications and Benefits:
- The pressing method is widely used in the production of advanced ceramics for applications such as cutting tools, medical implants, and electronic components. These materials require high strength, wear resistance, and dimensional stability, all of which are achieved through precise pressing techniques.
- The benefits of this method include the ability to produce complex shapes with high accuracy, improved material properties, and reduced waste compared to traditional forming methods.
By understanding and optimizing these key aspects, manufacturers can produce high-quality ceramic components that meet the demanding requirements of modern applications.
Summary Table:
Aspect | Details |
---|---|
Pressing Process | Shapes ceramic materials using pressure in a mold or die with a pressing furnace. |
Burnout Importance | Removes organic binders and impurities, ensuring uniform structure and strength. |
Semi-Isostatic Pressing | Achieves uniform pressure distribution for complex shapes and large components. |
Time & Temperature | Precise control prevents defects like cracking and ensures dimensional accuracy. |
Applications | Used in cutting tools, medical implants, and electronics for high performance. |
Discover how the pressing method can enhance your ceramic production—contact our experts today!