Hot press molding is a manufacturing process used to shape materials by applying heat and pressure simultaneously. It is commonly used for producing composite materials, plastics, ceramics, and metals. The process involves placing the material in a mold, heating it to a specific temperature, and then applying pressure to shape it into the desired form. This method ensures uniform density, improved mechanical properties, and precise dimensions. The key steps include material preparation, mold setup, heating, pressing, cooling, and demolding. Hot press molding is widely used in industries such as automotive, aerospace, and electronics due to its efficiency and ability to produce high-quality components.
Key Points Explained:
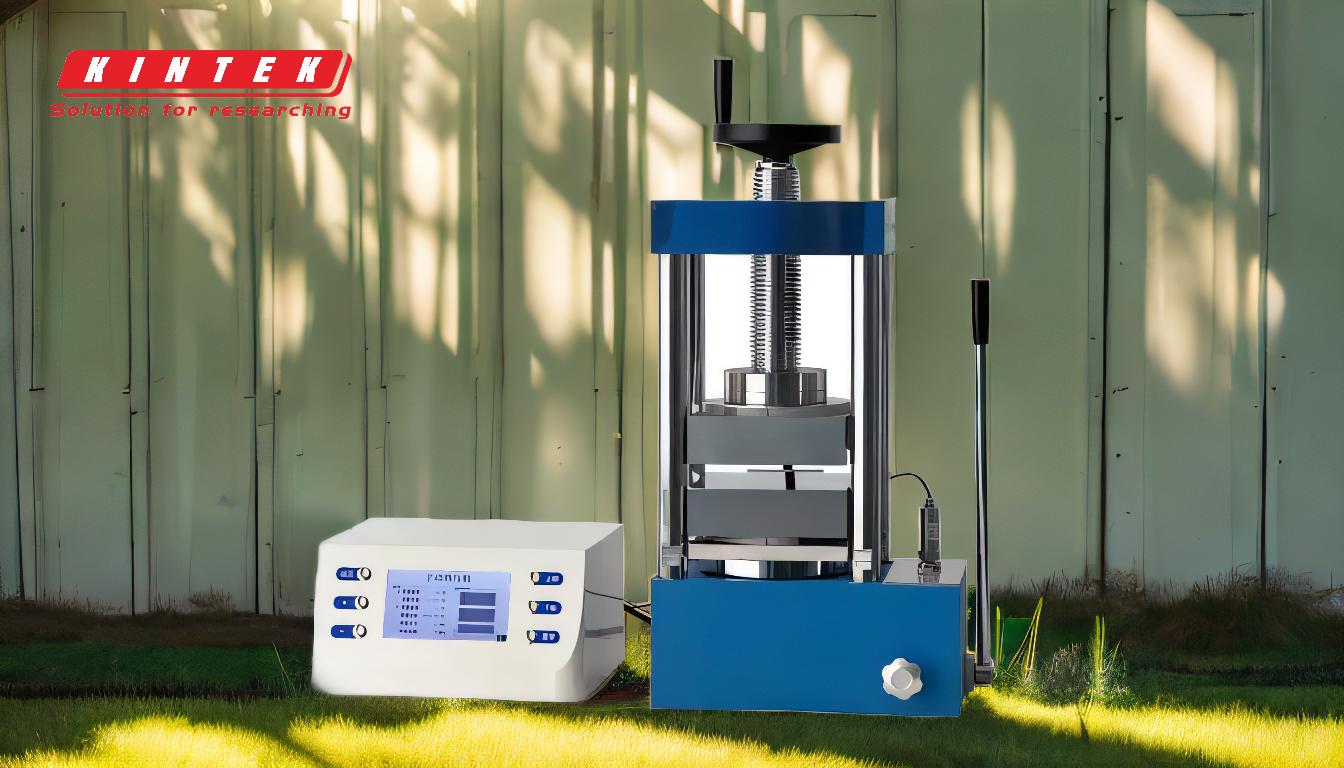
-
Material Preparation:
- The first step in hot press molding is preparing the raw material. This could be a composite, plastic, ceramic, or metal powder. The material is often pre-treated to ensure uniformity and to remove any impurities.
- For composite materials, fibers such as carbon or glass are often combined with a resin matrix. The resin is typically in a semi-solid state, which allows it to flow and fill the mold under pressure.
-
Mold Setup:
- The mold is designed according to the final product's specifications. It is usually made from high-strength materials like steel to withstand the high temperatures and pressures involved.
- The mold is cleaned and coated with a release agent to prevent the material from sticking to the mold surfaces. This ensures easy demolding after the process.
-
Heating:
- The material is placed inside the mold, and the assembly is then heated to a specific temperature. The temperature depends on the material being used and is critical for achieving the desired properties.
- Heating can be done using various methods, including electric heaters, steam, or oil. The heat softens the material, making it pliable and easier to shape under pressure.
-
Pressing:
- Once the material reaches the required temperature, pressure is applied using a hot press machine. The pressure ensures that the material fills the mold completely and achieves the desired density and shape.
- The amount of pressure applied depends on the material and the complexity of the mold. High pressure is often used to eliminate air pockets and ensure a uniform structure.
-
Cooling:
- After the pressing stage, the mold is cooled down. Cooling can be done naturally or using cooling systems like water or air jets. The cooling rate is controlled to prevent warping or internal stresses in the final product.
- Proper cooling ensures that the material solidifies in the desired shape and retains its mechanical properties.
-
Demolding:
- Once the material has cooled and solidified, the mold is opened, and the final product is removed. Care is taken during demolding to avoid damaging the product.
- The product may undergo additional post-processing steps such as trimming, polishing, or surface treatment to achieve the final specifications.
-
Applications:
- Hot press molding is widely used in various industries. In the automotive industry, it is used to produce lightweight and strong components like body panels and structural parts.
- In the aerospace industry, it is used to manufacture high-strength composite parts that can withstand extreme conditions.
- The electronics industry uses hot press molding to produce insulating components and circuit boards.
-
Advantages:
- Uniform Density: The application of heat and pressure ensures that the material has a uniform density, which improves its mechanical properties.
- Precision: Hot press molding allows for the production of parts with precise dimensions and complex shapes.
- Efficiency: The process is relatively fast and can be automated, making it suitable for high-volume production.
-
Limitations:
- Cost: The initial setup cost for hot press molding can be high due to the need for specialized molds and hot press machines.
- Material Limitations: Not all materials are suitable for hot press molding. The material must be able to withstand the high temperatures and pressures involved.
- Complexity: Designing and manufacturing molds for complex shapes can be challenging and may require advanced engineering expertise.
In conclusion, hot press molding is a versatile and efficient manufacturing process that offers numerous advantages, especially in industries requiring high-strength and precision components. However, it also has some limitations that need to be considered when selecting it as a manufacturing method.
Summary Table:
Step | Description |
---|---|
Material Preparation | Prepare raw materials (composites, plastics, ceramics, metals) by pre-treating. |
Mold Setup | Design and clean molds, apply release agents for easy demolding. |
Heating | Heat material to a specific temperature for pliability. |
Pressing | Apply pressure using a hot press machine to shape the material. |
Cooling | Cool the mold to solidify the material and prevent warping. |
Demolding | Remove the final product and perform post-processing if needed. |
Applications | Used in automotive, aerospace, and electronics for high-strength components. |
Advantages | Uniform density, precision, and efficiency in high-volume production. |
Limitations | High initial costs, material restrictions, and complex mold designs. |
Discover how hot press molding can enhance your production process—contact our experts today!