The sintering process is a critical method in metallurgy and material science, used to create solid structures from powdered materials by applying heat and pressure without melting the material completely. The process involves several stages, including raw material preparation, compaction, controlled heating, and cooling. The goal is to achieve particle bonding and densification, resulting in a cohesive and rigid structure. Key steps include material mixing, ignition, sintering under controlled conditions, and final solidification. The process is widely used in industries such as metalworking, ceramics, and powder metallurgy to produce components with specific mechanical and thermal properties.
Key Points Explained:
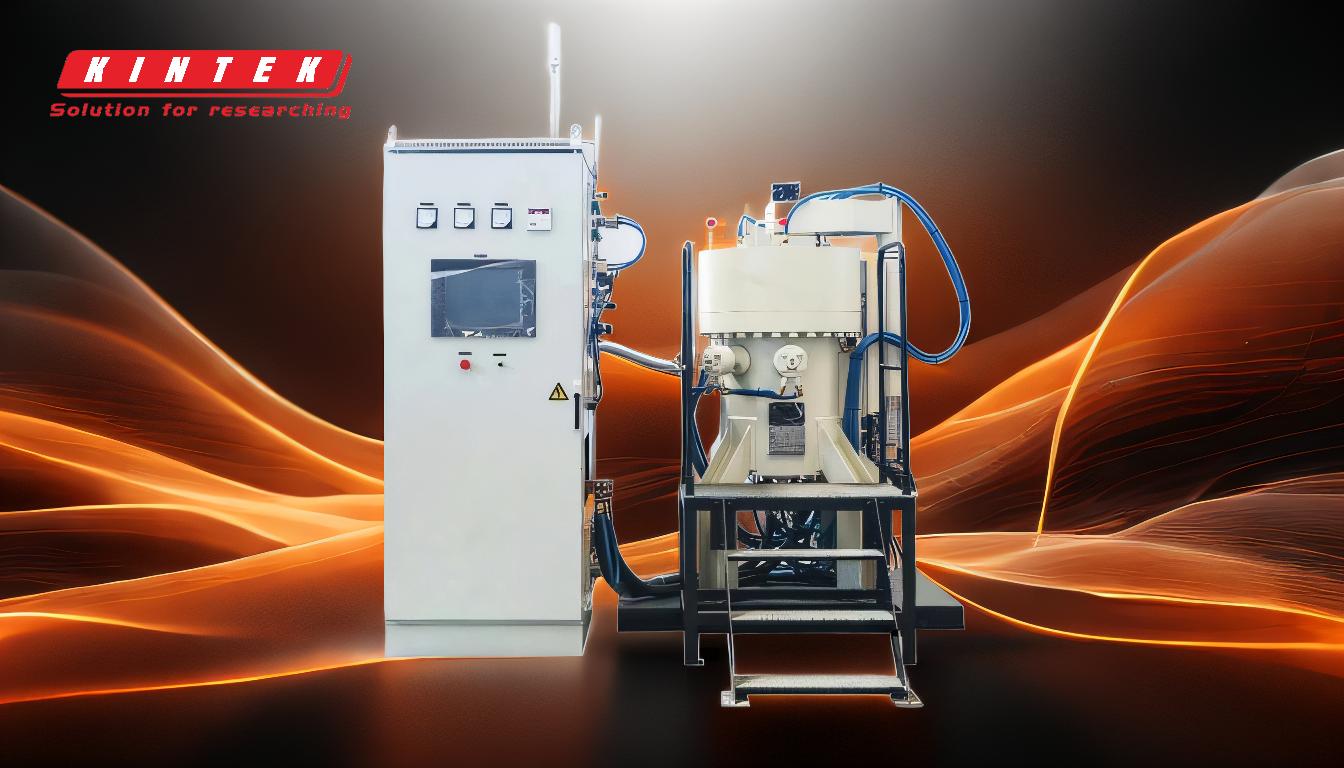
-
Preparation of Raw Materials:
- The process begins with the preparation of raw materials, typically in powder form. These materials are mixed with coupling agents, binders, and other additives to ensure uniformity and enhance bonding during sintering.
- The mixture is often spray-dried or mechanically pressed to create a homogeneous powder compact, which is then shaped into the desired form using cold or hot press machine techniques.
-
Compaction:
- The powder is compacted under high pressure to eliminate voids and ensure uniformity. This step is crucial for achieving the desired density and structural integrity in the final product.
- Compaction can be done using various methods, such as cold welds, 3D-printed lasers, or pressing tools, depending on the material and application.
-
Heating and Sintering:
- The compacted material is then subjected to controlled heating in a sintering furnace. The temperature is carefully regulated to facilitate particle bonding without causing complete melting.
- During this stage, particles undergo diffusion, leading to neck formation and densification. The process may involve transient or permanent liquid phase sintering to accelerate particle merging and densification.
-
Ignition and Controlled Sintering:
- In some sintering processes, such as those used in metallurgy, the surface of the material is ignited to initiate the sintering process. This step requires precise control of temperature, air volume, and vacuum to ensure uniform heating and sintering.
- The sintering process is carefully monitored to control parameters such as layer thickness, speed, and the sintering endpoint to achieve the desired material properties.
-
Cooling and Solidification:
- After sintering, the material is cooled to allow it to solidify into a rigid and cohesive structure. Cooling must be controlled to prevent cracking or warping and to ensure the material achieves the desired mechanical properties.
- During cooling, any remaining liquid or binder additives flow into open cracks or pores, further binding the mass together and enhancing the material's strength and durability.
-
Final Product Treatment:
- The sintered product may undergo additional treatments, such as machining, surface finishing, or heat treatment, to achieve the final desired properties and dimensions.
- These post-sintering treatments are essential for ensuring the product meets specific performance requirements and quality standards.
By following these steps, the sintering process transforms powdered materials into solid, high-performance components with tailored mechanical, thermal, and structural properties. This method is widely used in industries such as automotive, aerospace, and electronics to produce parts that are strong, durable, and resistant to wear and corrosion.
Summary Table:
Stage | Description |
---|---|
Raw Material Prep | Mix powders with binders and additives for uniformity and bonding. |
Compaction | Press powders under high pressure to eliminate voids and ensure density. |
Heating & Sintering | Heat compacted material to bond particles without melting. |
Ignition | Initiate sintering with controlled ignition for uniform heating. |
Cooling | Cool material to solidify and enhance strength and durability. |
Final Treatment | Machine or finish sintered product to meet performance standards. |
Discover how sintering can enhance your material production—contact our experts today!