Sintering in ceramic materials is a critical process that transforms powdered ceramics into a dense, solid structure through heat treatment below the melting point. This process involves several stages, including preparation of the powder compact, heating to remove binders, and high-temperature sintering to fuse particles. Key variables influencing sintering include temperature, atmosphere, pressure, and particle size, which collectively determine the final material properties such as strength, porosity, and density. The sintering process can be optimized by controlling these parameters to achieve desired characteristics in the final ceramic product.
Key Points Explained:
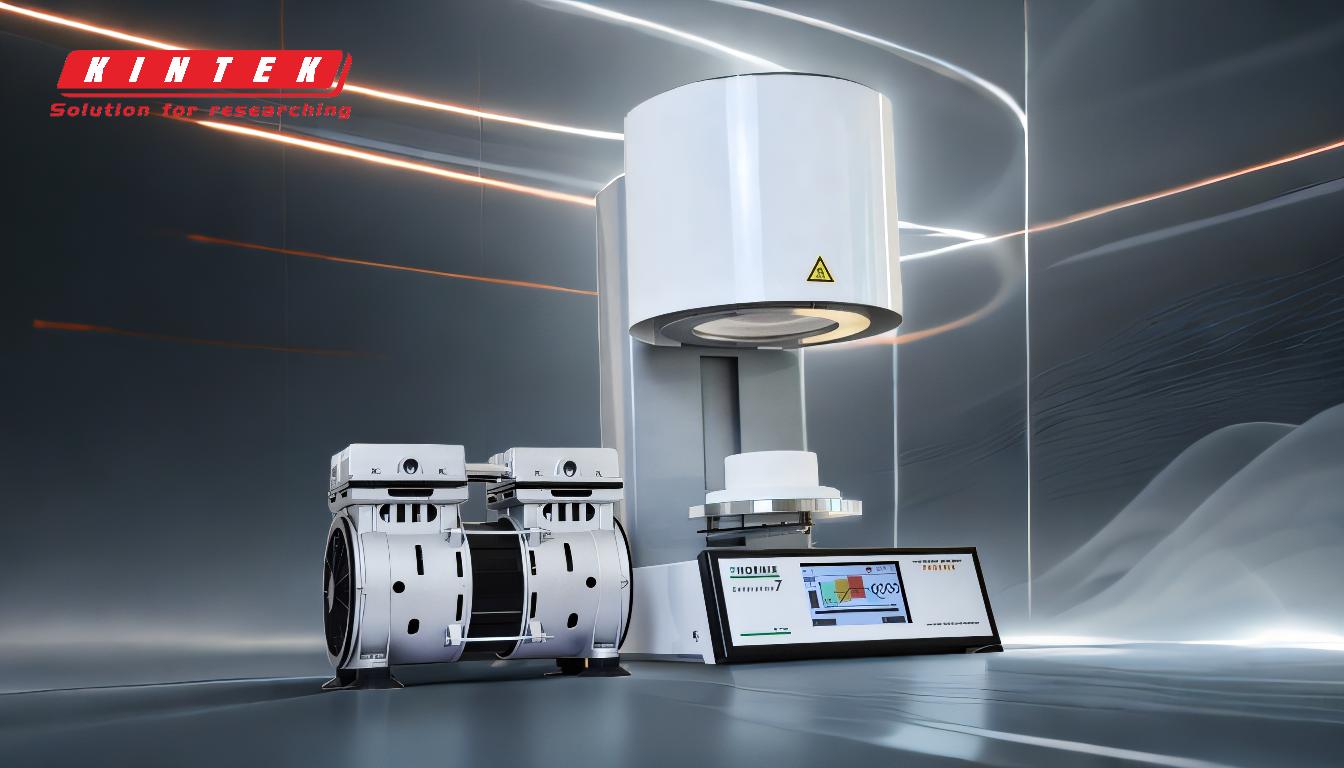
-
Preparation of the Powder Compact:
- Mixing and Slurry Formation: The process begins by mixing unfired ceramic powder with water, binders, and deflocculants to form a slurry. This slurry is then spray-dried to produce a free-flowing powder.
- Pressing into Green Body: The spray-dried powder is pressed into a mold to form a "green body," which is a shaped but unfired ceramic part. This step is crucial for achieving the desired shape and initial density.
-
Binder Removal:
- Low-Temperature Heating: The green body is heated at a low temperature to burn off the binder. This step is essential to prevent defects in the final product, as residual binders can cause porosity or cracking during high-temperature sintering.
-
High-Temperature Sintering:
- Heating to Just Below Melting Point: The green body is then heated to a high temperature, just below the melting point of the ceramic material. This step allows the particles to diffuse and bond together, reducing porosity and increasing density.
- Particle Merging and Densification: During sintering, particles densify and merge, which can be accelerated using techniques like liquid phase sintering (LPS). The process involves the diffusion of material from particle surfaces to the contact points between particles, leading to neck formation and eventual fusion.
-
Cooling and Solidification:
- Controlled Cooling: After sintering, the material is cooled in a controlled manner to solidify into a unified mass. The cooling rate can influence the final microstructure and properties of the ceramic.
-
Factors Influencing Sintering:
- Temperature: Higher temperatures generally increase the rate of sintering and improve material properties such as tensile strength and impact energy. However, excessive temperatures can lead to undesirable grain growth.
- Atmosphere: The sintering atmosphere (e.g., air, vacuum, or inert gases like argon or nitrogen) can affect the oxidation state of the ceramic and the rate of particle diffusion.
- Pressure: Applying pressure during sintering can enhance particle rearrangement and reduce porosity, leading to a denser final product.
- Particle Size and Composition: Smaller particles and homogeneous compositions promote better densification and more uniform sintering. The choice of sintering process and parameters depends on the desired properties of the final ceramic product.
-
Optimization of Sintering Process:
- Control of Parameters: The sintering process can be optimized by carefully controlling parameters such as sintering temperature, applied pressure, and the gaseous atmosphere. Finer powders and higher temperatures can increase compaction, but the amount of liquid phase must be carefully managed to avoid defects.
- Final Porosity: The final porosity of the sintered ceramic depends on the initial porosity of the green compact, as well as the temperature and duration of the sintering process. Pure oxide ceramics, for example, require longer sintering times and higher temperatures due to solid-state diffusion.
By understanding and controlling these key aspects, manufacturers can produce high-quality ceramic materials with tailored properties for various applications.
Summary Table:
Stage | Key Process | Purpose |
---|---|---|
Powder Preparation | Mixing ceramic powder with binders, water, and deflocculants to form a slurry. | Creates a free-flowing powder for shaping. |
Green Body Formation | Pressing the powder into a mold to form an unfired ceramic part. | Achieves the desired shape and initial density. |
Binder Removal | Low-temperature heating to burn off binders. | Prevents defects like porosity or cracking during sintering. |
High-Temperature Sintering | Heating just below the melting point to fuse particles. | Reduces porosity and increases density through particle diffusion. |
Cooling | Controlled cooling to solidify the material. | Influences final microstructure and properties. |
Key Variables | Temperature, atmosphere, pressure, and particle size. | Determines final material properties like strength and porosity. |
Optimize your ceramic sintering process for superior results—contact our experts today!