Simulated annealing is a probabilistic optimization technique inspired by the physical process of annealing in metallurgy, where a material is heated and then slowly cooled to reduce defects and achieve a stable, low-energy state. In optimization, it is used to find a near-optimal solution to complex problems by exploring the solution space, allowing for occasional uphill moves (worse solutions) to escape local optima. The method balances exploration and exploitation using a temperature parameter that decreases over time, controlling the probability of accepting worse solutions. It is particularly useful for solving combinatorial optimization problems where traditional methods struggle due to high complexity.
Key Points Explained:
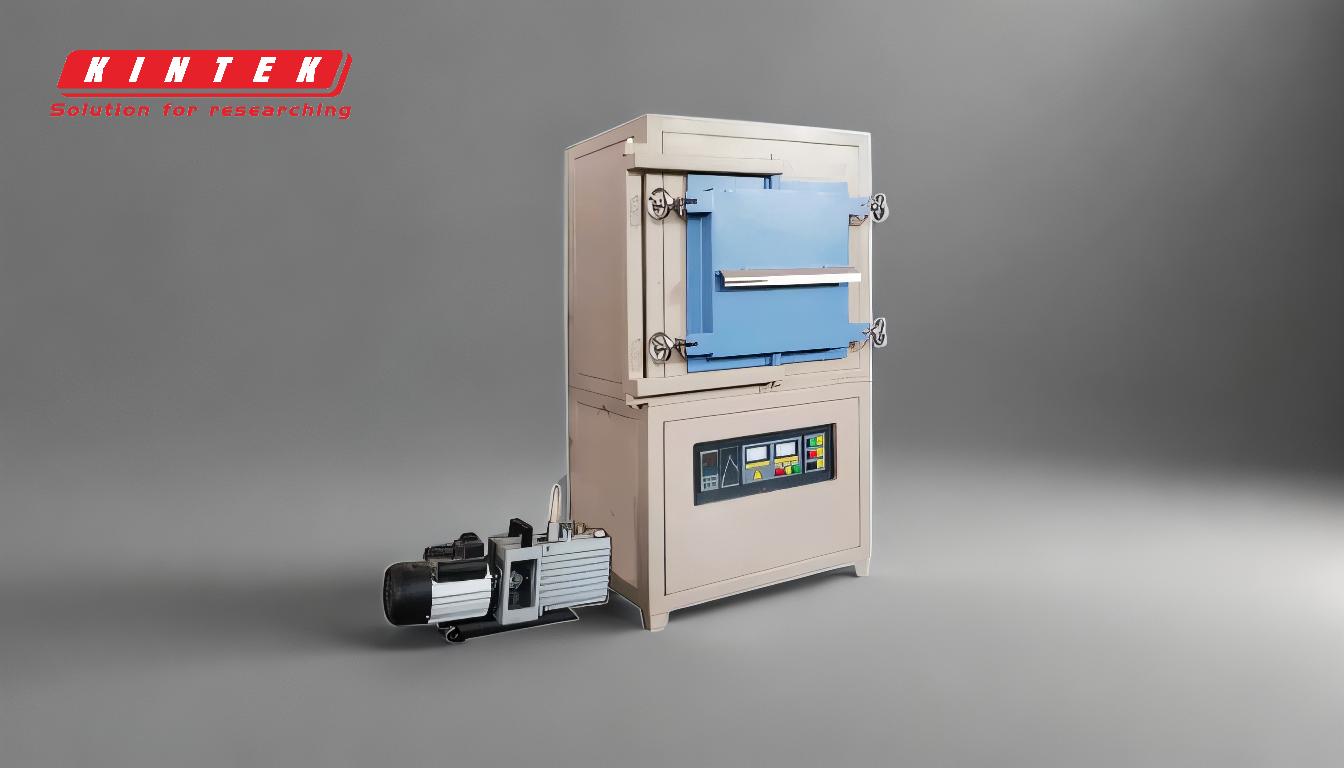
-
Inspiration from Metallurgy:
- Simulated annealing is based on the annealing process in metallurgy, where a material is heated to a high temperature and then gradually cooled to reduce defects and achieve a stable, low-energy state.
- This physical process is analogous to the optimization problem, where the goal is to find a solution with the minimum cost or maximum efficiency.
-
Optimization Framework:
- The method is used to solve optimization problems, particularly those with a large and complex solution space where finding the global optimum is computationally expensive.
- It is a metaheuristic approach, meaning it provides a high-level strategy for exploring the solution space without guaranteeing the optimal solution.
-
Temperature Parameter:
- A key feature of simulated annealing is the use of a temperature parameter, which controls the probability of accepting worse solutions during the search process.
- Initially, the temperature is high, allowing the algorithm to explore a wide range of solutions, including those that are worse than the current solution.
- As the temperature decreases over time, the algorithm becomes more selective, favoring solutions that improve the objective function.
-
Acceptance Probability:
- The probability of accepting a worse solution is determined by the Metropolis criterion, which is based on the difference in the objective function value between the current and new solutions.
- Mathematically, the acceptance probability ( P ) is given by: [ P = \exp\left(-\frac{\Delta E}{T}\right) ] where ( \Delta E ) is the change in the objective function value, and ( T ) is the current temperature.
- This probabilistic approach allows the algorithm to escape local optima and explore a broader solution space.
-
Cooling Schedule:
- The cooling schedule determines how the temperature decreases over time. Common schedules include exponential, logarithmic, and linear cooling.
- The choice of cooling schedule affects the balance between exploration and exploitation. A slower cooling rate allows for more exploration but increases computational time.
-
Applications:
- Simulated annealing is widely used in combinatorial optimization problems, such as the traveling salesman problem, job scheduling, and network design.
- It is also applied in continuous optimization problems, where the solution space is continuous rather than discrete.
-
Advantages:
- Simulated annealing is relatively simple to implement and does not require gradient information, making it suitable for problems where the objective function is non-differentiable or discontinuous.
- It is effective in escaping local optima and finding near-optimal solutions in complex solution spaces.
-
Limitations:
- The performance of simulated annealing depends heavily on the choice of parameters, such as the initial temperature and cooling schedule.
- It may require a large number of iterations to converge, especially for problems with a large solution space.
- The method does not guarantee finding the global optimum, and the quality of the solution depends on the problem and parameter settings.
-
Comparison with Other Methods:
- Compared to gradient-based methods, simulated annealing does not rely on derivatives and is more robust to non-convex and noisy objective functions.
- Compared to other metaheuristic methods like genetic algorithms, simulated annealing is simpler and requires fewer parameters, but it may be less effective in exploring diverse regions of the solution space.
-
Practical Considerations:
- When implementing simulated annealing, it is important to carefully choose the initial temperature, cooling schedule, and stopping criteria to balance exploration and exploitation.
- The method can be combined with other optimization techniques, such as local search, to improve its performance.
In summary, simulated annealing is a powerful and flexible optimization method inspired by the physical process of annealing. It is particularly useful for solving complex problems with large solution spaces, where traditional methods may struggle. By carefully controlling the temperature and acceptance probability, the method effectively balances exploration and exploitation, making it a valuable tool in both discrete and continuous optimization.
Summary Table:
Aspect | Description |
---|---|
Inspiration | Based on metallurgical annealing process to reduce defects and achieve stability. |
Optimization Framework | Solves complex problems with large solution spaces, using a metaheuristic approach. |
Temperature Parameter | Controls the probability of accepting worse solutions, balancing exploration and exploitation. |
Acceptance Probability | Determined by the Metropolis criterion: ( P = \exp(-\Delta E / T) ). |
Cooling Schedule | Determines how temperature decreases over time (e.g., exponential, logarithmic). |
Applications | Traveling salesman problem, job scheduling, network design, and more. |
Advantages | Simple to implement, no gradient required, effective in escaping local optima. |
Limitations | Performance depends on parameters; may require many iterations to converge. |
Comparison | More robust than gradient-based methods; simpler than genetic algorithms. |
Practical Tips | Choose initial temperature, cooling schedule, and stopping criteria carefully. |
Ready to optimize complex problems with simulated annealing? Contact our experts today for tailored solutions!