Chemical Vapor Deposition (CVD) is a versatile process used to deposit high-quality thin films and coatings on various substrates. The substrate plays a critical role in the CVD process, as it must withstand the high temperatures and chemical reactions involved. Common substrates include silicon wafers, glass, metals, and ceramics, chosen based on their thermal stability, chemical compatibility, and intended application. The CVD process involves gas-phase reactions and surface reactions, which can be tailored using different methods like aerosol-assisted CVD, direct liquid injection, or plasma-based techniques to suit specific substrate requirements.
Key Points Explained:
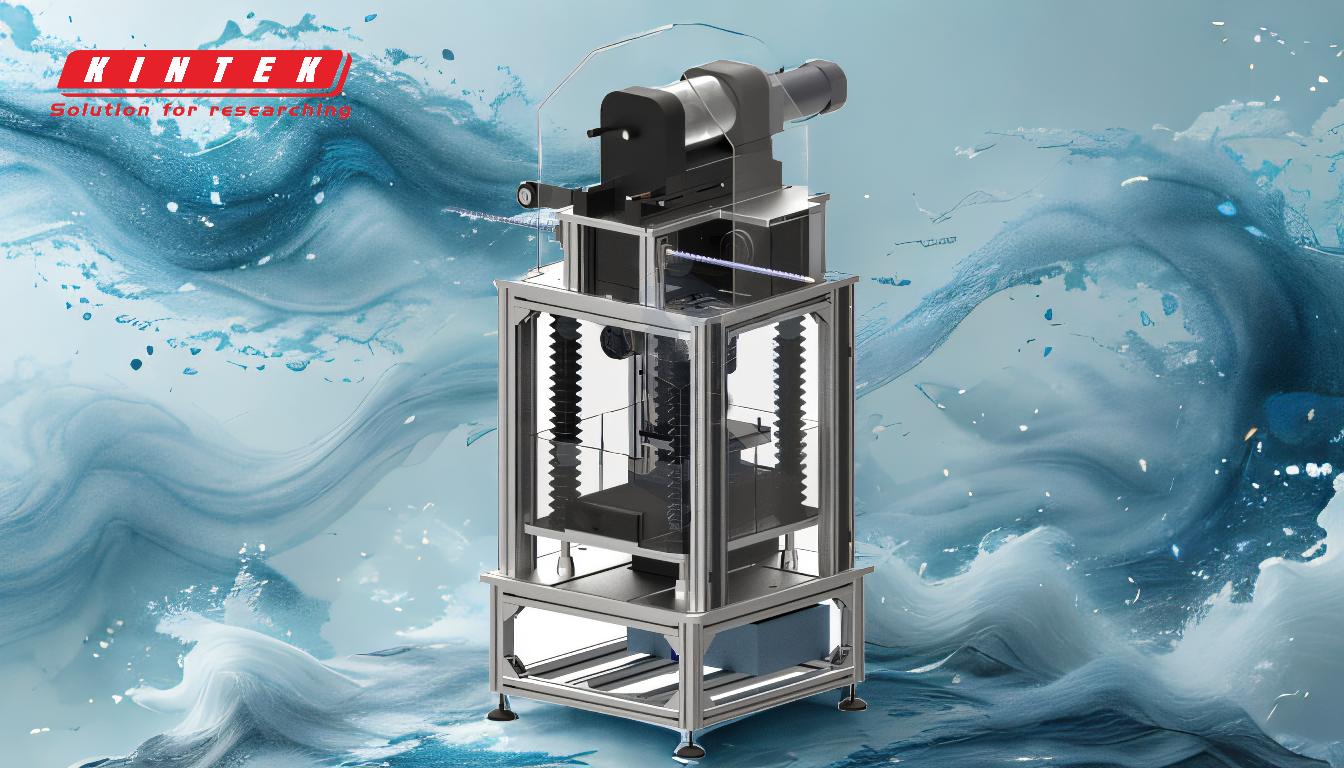
-
Role of Substrates in CVD:
- Substrates are the foundation for thin film deposition in CVD. They must be thermally stable, chemically compatible, and mechanically robust to withstand the process conditions.
- The choice of substrate depends on the application, such as semiconductors, optics, or protective coatings.
-
Common Substrate Materials:
- Silicon Wafers: Widely used in semiconductor manufacturing due to their excellent thermal and electrical properties.
- Glass: Used in optical and display applications because of its transparency and smooth surface.
- Metals: Often used for protective coatings or as conductive layers in electronic devices.
- Ceramics: Chosen for their high thermal stability and resistance to chemical reactions.
-
Thermal and Chemical Compatibility:
- CVD typically involves high temperatures (850-1100°C), so substrates must withstand these conditions without degrading.
- Plasma or laser-assisted CVD can reduce the temperature, expanding the range of suitable substrates.
-
Types of CVD and Substrate Considerations:
- Aerosol-Assisted CVD: Uses aerosolized precursors, suitable for substrates requiring uniform coatings.
- Direct Liquid Injection CVD: Involves liquid precursors, ideal for substrates needing precise control over film composition.
- Plasma-Based CVD: Utilizes plasma to lower deposition temperatures, enabling the use of temperature-sensitive substrates.
-
Applications of CVD Substrates:
- Semiconductors: Silicon wafers are the primary substrate for microelectronics and integrated circuits.
- Optics: Glass substrates are used for anti-reflective coatings and optical filters.
- Protective Coatings: Metals and ceramics are coated to enhance durability and resistance to wear or corrosion.
-
Challenges and Solutions:
- High-temperature limitations can restrict substrate choices. Advanced techniques like plasma-assisted CVD or laser-assisted CVD address this by enabling lower-temperature processing.
- Substrate surface preparation, such as cleaning and pre-treatment, is crucial to ensure proper adhesion and film quality.
By understanding the properties and requirements of different substrates, manufacturers can optimize the CVD process for specific applications, ensuring high-quality thin films and coatings.
Summary Table:
Substrate | Key Properties | Applications |
---|---|---|
Silicon Wafers | Thermal stability, electrical properties | Semiconductors, microelectronics |
Glass | Transparency, smooth surface | Optics, display coatings |
Metals | Conductivity, durability | Protective coatings, electronic devices |
Ceramics | Thermal stability, chemical resistance | High-temperature applications, coatings |
Need help selecting the right substrate for your CVD process? Contact our experts today for tailored solutions!